Twin-screw compounding is a highly efficient and widely used method for mixing polymers with fillers, fibers, and additives. This process primarily utilizes a corotating intermeshing twin-screw extruder (TSE), which operates at high speeds and features tight geometric tolerances for screws and barrels. The TSE's design allows for precise control over the mixing process, ensuring uniform dispersion of materials and high-quality end products. Twin-screw compounding is favored in industries requiring consistent and tailored material properties, such as plastics, pharmaceuticals, and food processing.
Key Points Explained:
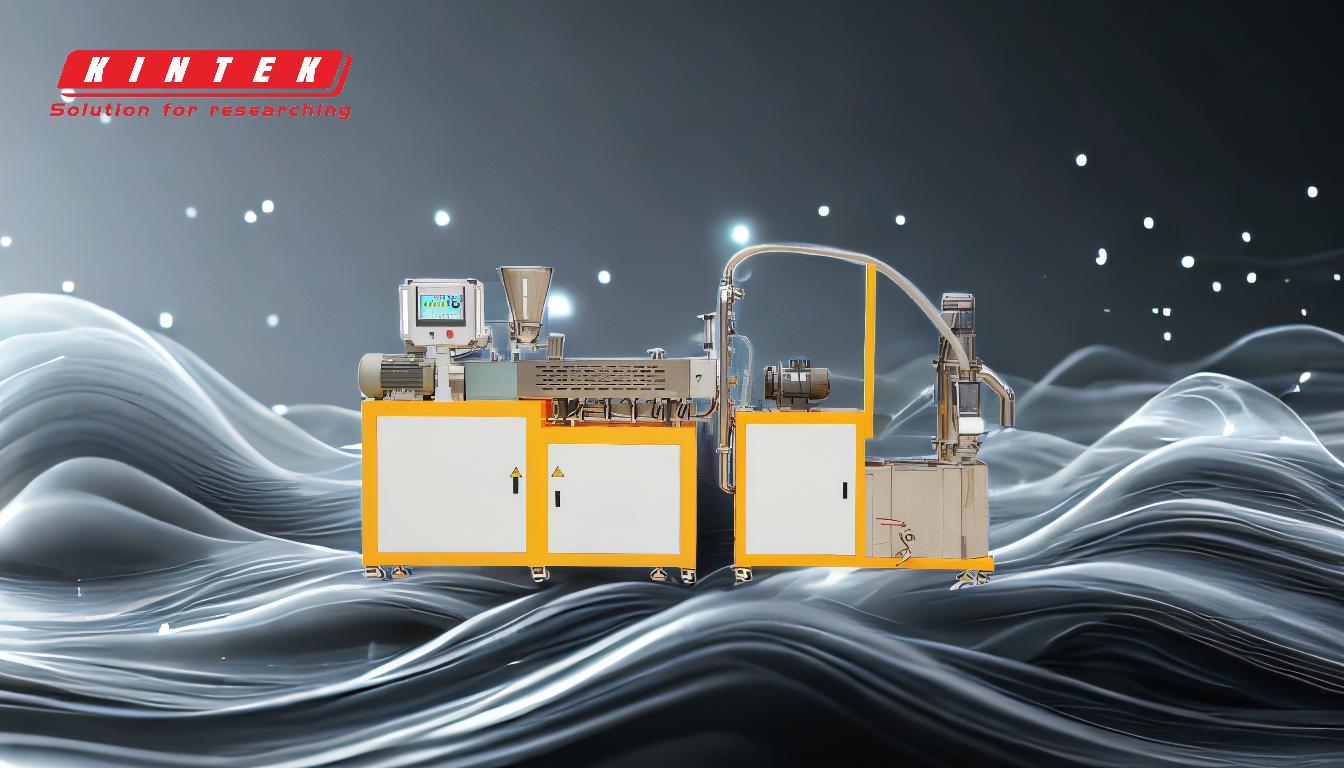
-
Definition of Twin-Screw Compounding
- Twin-screw compounding refers to the process of blending polymers with additives, fillers, or fibers using a twin-screw extruder (TSE).
- The TSE consists of two screws that rotate in the same direction (corotating) and intermesh, creating a highly efficient mixing environment.
- This method is widely used in industries that require precise control over material properties, such as polymer engineering, pharmaceuticals, and food production.
-
Core Components of a Twin-Screw Extruder (TSE)
- Screws: The twin screws are the heart of the system, designed with specific geometries to achieve optimal mixing. The intermeshing design ensures thorough material interaction.
- Barrels: The barrels house the screws and are engineered with tight tolerances to maintain consistent processing conditions.
- High-Speed Operation: The TSE operates at high speeds, enabling rapid and efficient mixing of materials.
-
Advantages of Twin-Screw Compounding
- Uniform Mixing: The intermeshing screws ensure even distribution of fillers, fibers, and additives within the polymer matrix.
- Flexibility: The modular design of TSEs allows for customization of screw configurations and processing parameters to meet specific material requirements.
- High Throughput: The high-speed operation enables large-scale production with consistent quality.
- Versatility: Suitable for a wide range of materials, including thermoplastics, thermosets, and reactive polymers.
-
Applications of Twin-Screw Compounding
- Polymer Blending: Used to create polymer blends with enhanced mechanical, thermal, or chemical properties.
- Filler and Fiber Incorporation: Ideal for mixing polymers with fillers (e.g., glass fibers, carbon fibers) to improve strength, stiffness, or conductivity.
- Additive Dispersion: Ensures uniform distribution of additives such as UV stabilizers, flame retardants, or colorants.
- Reactive Extrusion: Facilitates chemical reactions during the extrusion process, such as polymerization or grafting.
-
Key Considerations for Equipment Selection
- Screw Design: The geometry and configuration of the screws must align with the specific mixing requirements of the materials.
- Barrel Configuration: Modular barrels allow for customization of heating, cooling, and venting zones to optimize processing conditions.
- Throughput Capacity: The size and speed of the TSE should match the production volume and material characteristics.
- Material Compatibility: Ensure the TSE is compatible with the types of polymers, fillers, and additives being processed.
-
Challenges and Solutions in Twin-Screw Compounding
- Material Degradation: High shear rates and temperatures can lead to degradation of sensitive materials. Solution: Optimize screw speed and temperature profiles.
- Wear and Tear: Abrasive fillers can cause wear on screws and barrels. Solution: Use wear-resistant materials for screw and barrel construction.
- Process Control: Maintaining consistent quality requires precise control over processing parameters. Solution: Implement advanced monitoring and automation systems.
-
Future Trends in Twin-Screw Compounding
- Sustainability: Increasing focus on using recycled materials and reducing energy consumption in compounding processes.
- Advanced Materials: Development of new polymers and composites with enhanced properties, driving innovation in TSE design.
- Automation and Digitalization: Integration of IoT and AI technologies for real-time monitoring and optimization of compounding processes.
By understanding these key points, equipment and consumable purchasers can make informed decisions about selecting and utilizing twin-screw compounding systems for their specific needs. This method offers unparalleled flexibility, efficiency, and quality in material processing, making it a cornerstone of modern manufacturing.
Summary Table:
Key Aspect | Details |
---|---|
Definition | Blending polymers with additives, fillers, or fibers using a twin-screw extruder (TSE). |
Core Components | Screws, barrels, and high-speed operation for efficient mixing. |
Advantages | Uniform mixing, flexibility, high throughput, and material versatility. |
Applications | Polymer blending, filler/fiber incorporation, additive dispersion, reactive extrusion. |
Equipment Selection | Screw design, barrel configuration, throughput capacity, material compatibility. |
Challenges & Solutions | Material degradation, wear and tear, process control. |
Future Trends | Sustainability, advanced materials, automation, and digitalization. |
Optimize your polymer mixing process with twin-screw compounding—contact our experts today!