To answer the question about the materials used for coating on carbides, it is essential to understand the purpose and properties of these coatings. Carbides, such as tungsten carbide, are widely used in industrial applications due to their hardness and wear resistance. However, to further enhance their performance, coatings are applied to improve properties like corrosion resistance, thermal stability, and friction reduction. Common coating materials include titanium nitride (TiN), titanium carbonitride (TiCN), aluminum titanium nitride (AlTiN), and diamond-like carbon (DLC). These coatings are typically applied using physical vapor deposition (PVD) or chemical vapor deposition (CVD) techniques. The choice of coating material depends on the specific application requirements, such as operating temperature, wear conditions, and chemical exposure.
Key Points Explained:
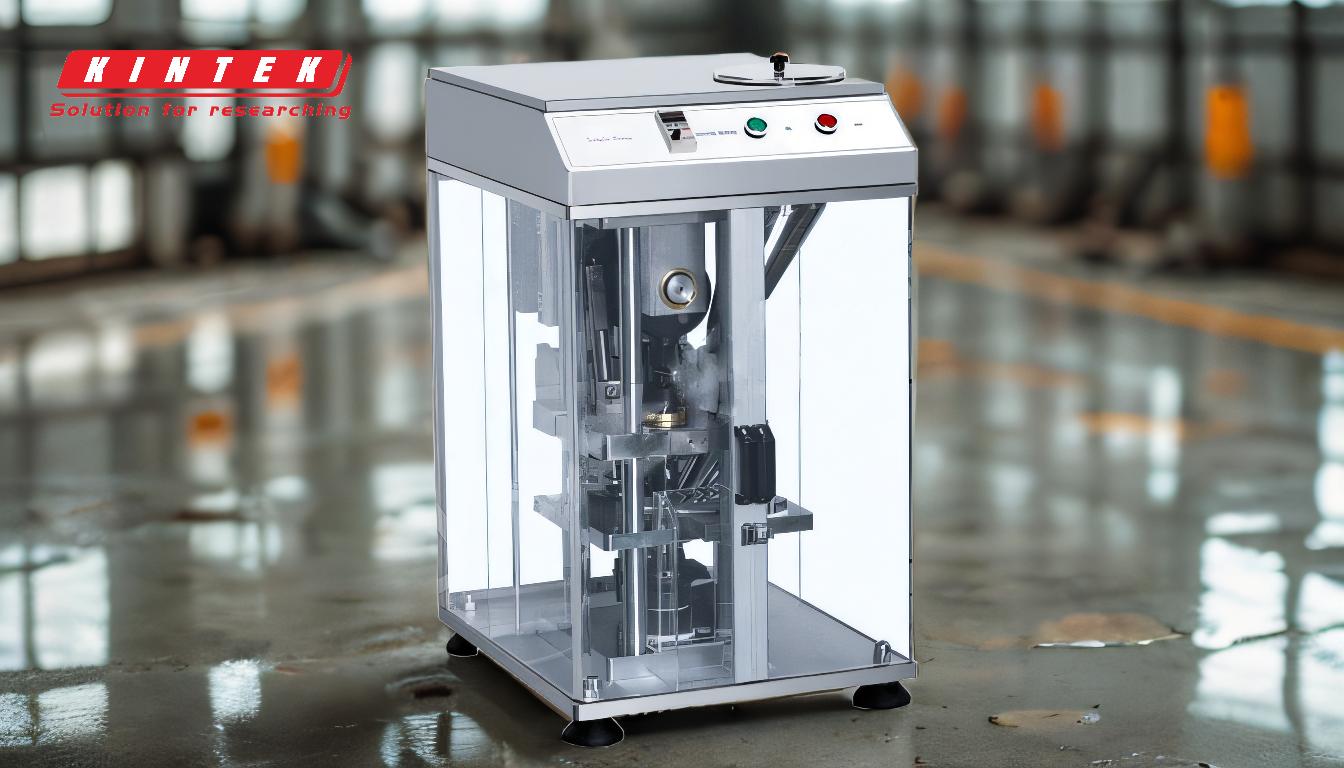
-
Purpose of Coatings on Carbides
- Carbides, such as tungsten carbide, are inherently hard and wear-resistant but may lack other desirable properties like corrosion resistance or thermal stability.
- Coatings are applied to enhance these properties, making carbides suitable for demanding applications like cutting tools, molds, and wear-resistant components.
-
Common Coating Materials
- Titanium Nitride (TiN): Provides excellent hardness, wear resistance, and a distinctive gold color. It is widely used in cutting tools and decorative applications.
- Titanium Carbonitride (TiCN): Offers higher hardness and wear resistance than TiN, making it suitable for high-speed machining and abrasive environments.
- Aluminum Titanium Nitride (AlTiN): Known for its high thermal stability and oxidation resistance, AlTiN is ideal for high-temperature applications like dry machining.
- Diamond-Like Carbon (DLC): Exhibits low friction, high hardness, and excellent wear resistance, making it suitable for applications requiring reduced friction and improved durability.
-
Coating Techniques
- Physical Vapor Deposition (PVD): A process where the coating material is vaporized in a vacuum and deposited onto the carbide substrate. PVD coatings are thin, dense, and adhere well to the substrate.
- Chemical Vapor Deposition (CVD): Involves chemical reactions to produce a coating on the substrate. CVD coatings are thicker and can withstand higher temperatures, making them suitable for heavy-duty applications.
-
Factors Influencing Coating Selection
- Operating Temperature: High-temperature applications require coatings like AlTiN, which can withstand heat without degrading.
- Wear Conditions: Abrasive environments benefit from harder coatings like TiCN or DLC.
- Chemical Exposure: Coatings like TiN provide good resistance to chemical corrosion.
- Application-Specific Requirements: Decorative coatings may prioritize aesthetics, while industrial coatings focus on performance.
-
Advantages of Coated Carbides
- Enhanced durability and lifespan of tools and components.
- Improved performance in extreme conditions, such as high temperatures or corrosive environments.
- Reduced friction and wear, leading to energy efficiency and cost savings.
-
Applications of Coated Carbides
- Cutting tools for machining metals, composites, and other materials.
- Molds and dies for manufacturing processes.
- Wear-resistant components in industries like aerospace, automotive, and mining.
By understanding the materials and techniques used for coating carbides, purchasers can make informed decisions based on the specific needs of their applications. The choice of coating material and method directly impacts the performance, durability, and cost-effectiveness of carbide-based products.
Summary Table:
Coating Material | Key Properties | Applications |
---|---|---|
Titanium Nitride (TiN) | Hardness, wear resistance, gold color | Cutting tools, decorative uses |
Titanium Carbonitride (TiCN) | Higher hardness, wear resistance | High-speed machining, abrasive environments |
Aluminum Titanium Nitride (AlTiN) | Thermal stability, oxidation resistance | High-temperature applications |
Diamond-Like Carbon (DLC) | Low friction, high hardness, wear resistance | Friction reduction, durability |
Need the right coating for your carbide tools? Contact our experts today for tailored solutions!