Vibrating screens are essential equipment in various industries, including mining, construction, and recycling, used for separating materials by size. The size of a vibrating screen is a critical factor that determines its capacity, efficiency, and suitability for specific applications. Vibrating screens come in a wide range of sizes, from small, portable units to large, industrial-grade machines. The size of the screen is typically defined by its width, length, and the number of screening decks. Smaller screens are ideal for light-duty applications, while larger screens are designed for heavy-duty operations. The choice of screen size depends on the volume of material to be processed, the desired throughput, and the specific screening requirements of the application.
Key Points Explained:
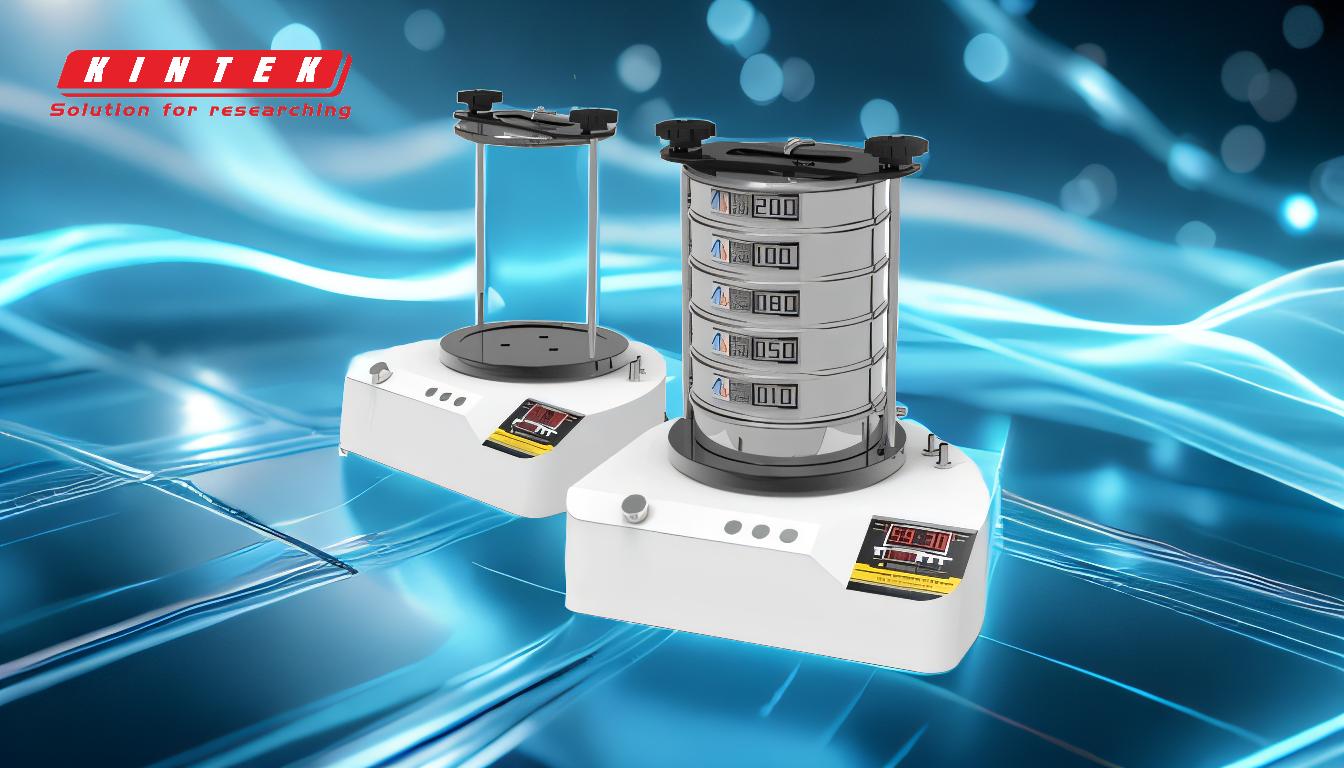
-
Definition of Vibrating Screen Size:
- The size of a vibrating screen is generally described by its width and length, often measured in millimeters or inches. For example, a screen might be described as 1200mm x 2400mm (4ft x 8ft).
- The size also includes the number of decks, which can range from single-deck to multi-deck configurations. Multi-deck screens allow for the separation of materials into multiple size fractions in a single pass.
-
Common Sizes of Vibrating Screens:
- Small Screens: These are typically used in laboratories or small-scale operations. They might measure around 600mm x 1200mm (2ft x 4ft) and are designed for low-capacity applications.
- Medium Screens: These are more commonly used in industrial settings and can measure around 1200mm x 2400mm (4ft x 8ft). They are suitable for medium-capacity operations.
- Large Screens: These are used in heavy-duty applications, such as mining or large-scale construction projects. They can measure up to 2400mm x 4800mm (8ft x 16ft) or larger and are designed to handle high volumes of material.
-
Factors Influencing Screen Size Selection:
- Material Volume: The amount of material to be processed is a primary consideration. Larger screens are necessary for high-volume operations to ensure efficient processing.
- Desired Throughput: The required throughput, or the amount of material processed per unit of time, will influence the size of the screen. Higher throughput requirements typically necessitate larger screens.
- Screening Specifications: The specific size fractions required will also affect the choice of screen size. For example, if multiple size fractions are needed, a multi-deck screen may be required.
- Space Constraints: The available space for the vibrating screen installation may limit the size of the screen that can be used.
-
Applications and Screen Size:
- Mining: In mining operations, large vibrating screens are often used to process bulk materials such as ore. These screens are designed to handle large volumes and are typically multi-deck to separate different size fractions.
- Construction: In construction, medium-sized screens are commonly used for sorting aggregates and other materials. These screens are often portable and can be moved between job sites.
- Recycling: In recycling operations, smaller screens may be used to separate materials such as plastics, metals, and paper. These screens are often designed for ease of use and low maintenance.
-
Customization and Modular Designs:
- Vibrating screens can be customized to meet specific requirements. This includes the ability to adjust the size, number of decks, and screen media (the material used for the screening surface).
- Modular designs allow for the addition or removal of decks, making it possible to adapt the screen to different applications or changes in processing requirements.
-
Impact of Screen Size on Performance:
- Efficiency: Larger screens generally offer higher efficiency due to their increased screening area, which allows for more material to be processed at once.
- Capacity: The capacity of a vibrating screen is directly related to its size. Larger screens can handle higher volumes of material, making them suitable for large-scale operations.
- Maintenance: Larger screens may require more maintenance due to their increased complexity and the higher loads they handle. However, modern designs often incorporate features that reduce maintenance requirements.
-
Noise and Material Contamination:
- The size of the screen can also impact noise levels and the potential for material contamination. Larger screens may generate more noise, but they are often designed with noise-reduction features. Additionally, the design of the screen can minimize material contamination by ensuring that the screening process is as efficient as possible.
In conclusion, the size of a vibrating screen is a critical factor that influences its performance, capacity, and suitability for specific applications. The choice of screen size should be based on the volume of material to be processed, the desired throughput, and the specific screening requirements of the application. By carefully considering these factors, users can select the appropriate vibrating screen size to meet their needs and ensure efficient and effective material processing.
Summary Table:
Screen Size | Dimensions | Applications |
---|---|---|
Small Screens | ~600mm x 1200mm | Laboratories, low-capacity operations |
Medium Screens | ~1200mm x 2400mm | Industrial, medium-capacity operations |
Large Screens | ~2400mm x 4800mm+ | Mining, heavy-duty, high-volume operations |
Need help selecting the perfect vibrating screen size? Contact our experts today for tailored solutions!