The size of balls to use in a ball mill depends on several factors, including the desired particle size of the final product, the hardness and nature of the material being ground, the size and design of the mill, and the rotation speed. Smaller balls are typically used for finer grinding, as they provide more contact points and can produce smaller particles. However, larger balls may be more effective for coarser grinding or harder materials. The optimal ball size is a balance between grinding efficiency, energy consumption, and the specific requirements of the material being processed.
Key Points Explained:
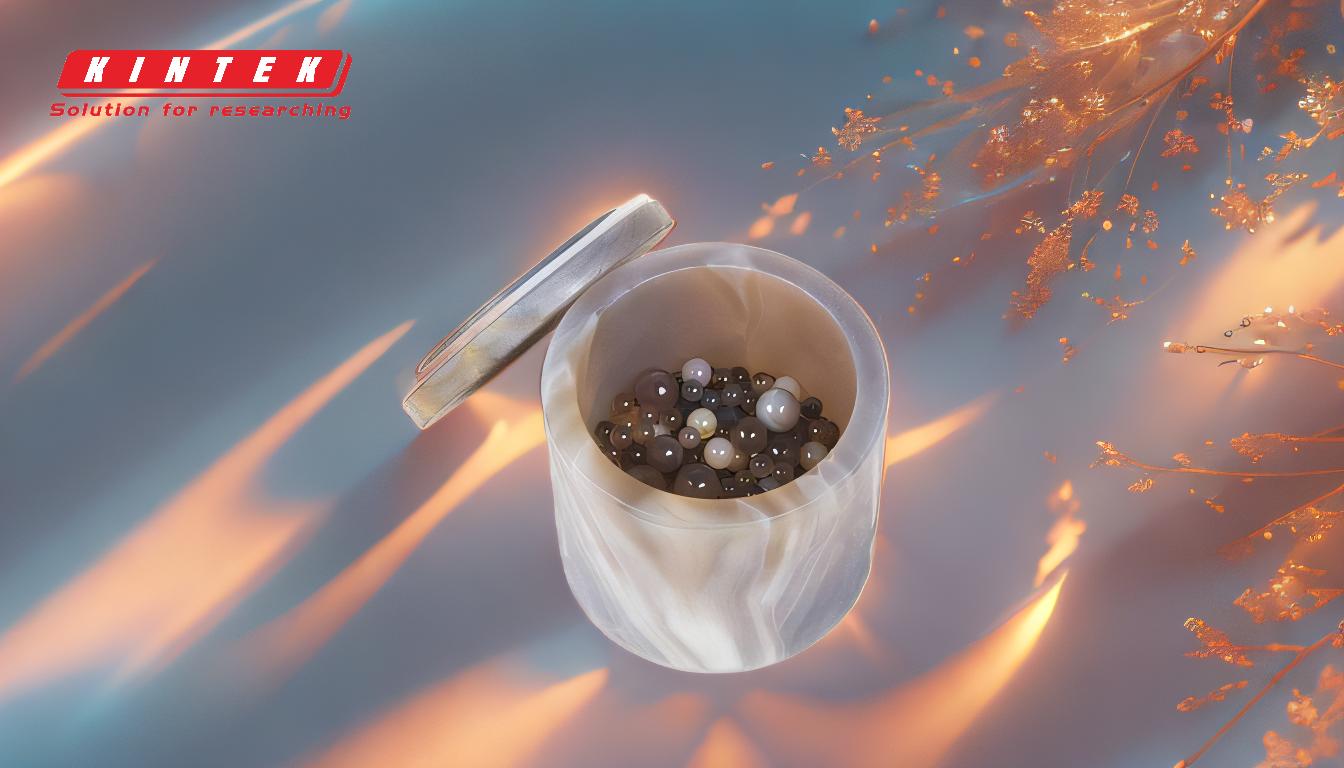
-
Desired Particle Size:
- Smaller balls are generally used when the goal is to produce finer particles. This is because smaller balls have a larger surface area relative to their volume, which increases the number of contact points with the material being ground. This leads to more efficient grinding and the production of smaller particles.
- Larger balls are more suitable for coarser grinding, as they can impart more energy to the material, breaking it down into larger particles.
-
Hardness and Nature of the Material:
- Harder materials may require larger balls to effectively break them down. Larger balls can deliver more impact force, which is necessary for grinding harder substances.
- Softer materials can be ground more effectively with smaller balls, as the goal is often to achieve a fine, uniform particle size rather than to break down tough materials.
-
Mill Design and Rotation Speed:
- The size of the mill and its rotation speed also play a role in determining the optimal ball size. Larger mills or those operating at higher speeds may require larger balls to ensure that the balls are lifted and dropped effectively, providing the necessary impact for grinding.
- The ratio of the drum diameter to its length (L:D ratio) is another important factor. An optimal L:D ratio (typically 1.56–1.64) ensures that the balls are distributed evenly and that the material is ground uniformly.
-
Ball Filling and Sizes:
- The filling level of the mill with balls (ball filling) and the distribution of ball sizes can affect grinding efficiency. A mix of different ball sizes may be used to optimize grinding, as larger balls can break down coarse material while smaller balls can refine the particle size.
- The armor surface shape inside the mill can also influence the grinding process, as it affects how the balls are lifted and dropped.
-
Energy Consumption and Efficiency:
- Smaller balls may require longer grinding times to achieve the desired particle size, which can increase energy consumption. However, they may also provide more efficient grinding in terms of particle size reduction.
- Larger balls may reduce grinding time but could lead to higher energy consumption due to the increased impact force required.
-
Timely Removal of Ground Product:
- The efficiency of the grinding process can also be influenced by how quickly the ground product is removed from the mill. If the product is not removed promptly, it can lead to over-grinding or re-agglomeration of particles, which can affect the final particle size distribution.
In summary, the size of balls to use in a ball mill should be chosen based on a combination of factors, including the desired particle size, the hardness of the material, the design and speed of the mill, and the need to balance grinding efficiency with energy consumption. A mix of ball sizes may be optimal in some cases, and the grinding process should be monitored to ensure that the final product meets the required specifications.
Summary Table:
Factor | Impact on Ball Size |
---|---|
Desired Particle Size | Smaller balls for finer particles; larger balls for coarser grinding. |
Material Hardness | Larger balls for harder materials; smaller balls for softer materials. |
Mill Design & Rotation Speed | Larger mills or higher speeds may require larger balls for effective grinding. |
Ball Filling & Sizes | A mix of ball sizes can optimize grinding efficiency. |
Energy Consumption | Smaller balls may increase energy use; larger balls may reduce grinding time. |
Timely Product Removal | Ensures consistent particle size and prevents over-grinding. |
Need help selecting the right ball size for your ball mill? Contact our experts today for personalized guidance!