Sputtering is a versatile and widely used thin-film deposition technique that involves bombarding a target material with high-energy ions, typically from an inert gas like argon, in a vacuum chamber. This process dislodges atoms or molecules from the target, which then deposit onto a substrate, forming a thin, uniform film. Sputtering is valued for its ability to produce dense, high-quality coatings with precise control over thickness and composition. It is used in various industries, including semiconductors, optics, and automotive, for applications ranging from creating conductive layers on microchips to enhancing the durability and appearance of cookware. The process is particularly advantageous for its ability to deposit films at low temperatures and over large areas, making it suitable for temperature-sensitive substrates and mass production.
Key Points Explained:
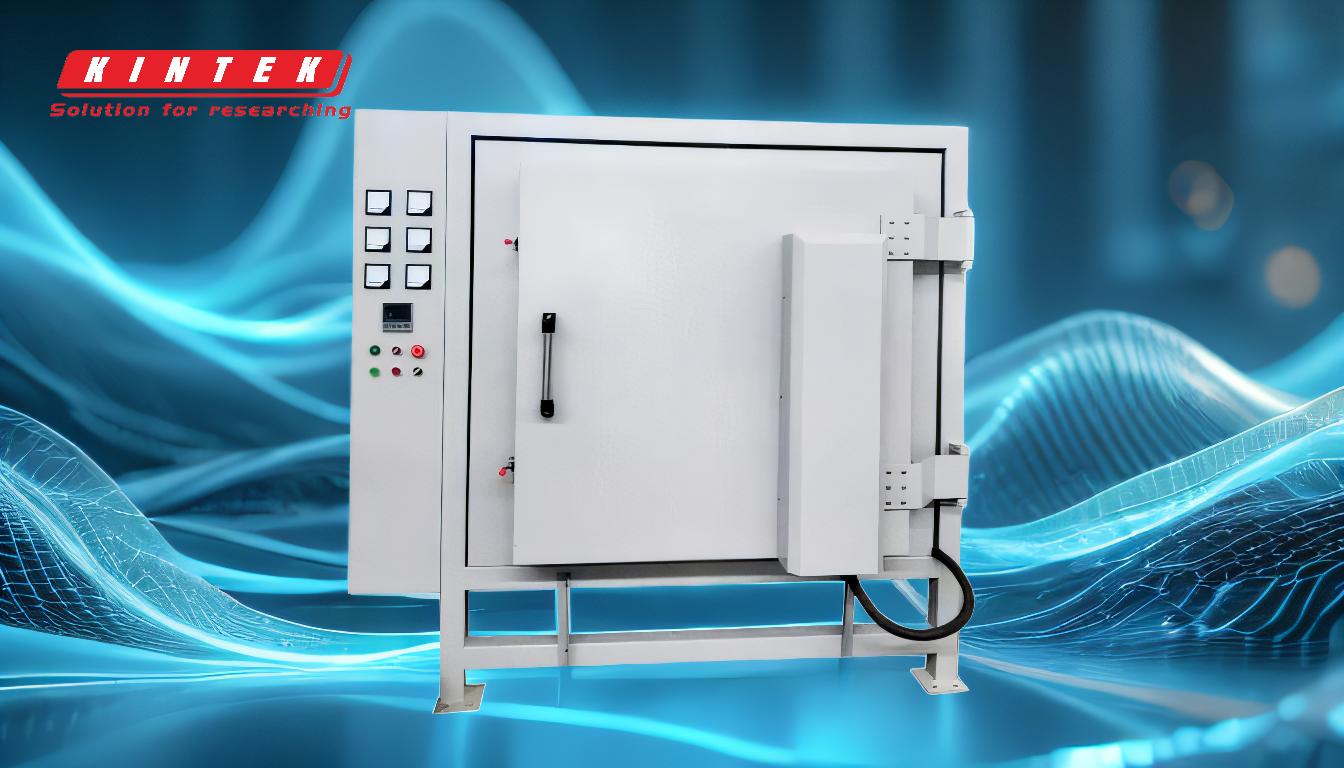
-
Mechanism of Sputtering:
- Sputtering involves bombarding a target material with high-energy ions, typically from an inert gas like argon, in a vacuum chamber.
- The ions collide with the target, dislodging atoms or molecules, which then travel through the vacuum and deposit onto a substrate.
- This process creates a thin, uniform film on the substrate, with the thickness controlled by adjusting the deposition time.
-
Advantages of Sputtering:
- Uniformity: Sputtering allows for uniform coating over large areas, making it ideal for applications requiring consistent film thickness.
- Density and Stress Reduction: The process densifies the deposited film and reduces residual stress, especially at lower deposition temperatures (below 150 °C).
- Precision: Film thickness can be precisely controlled by adjusting the deposition time, which is crucial for applications like semiconductor manufacturing.
- Versatility: Sputtering can be used with a wide range of materials, including metals, alloys, and ceramics, making it suitable for various industries.
-
Applications of Sputtering:
- Semiconductors: Sputtering is used to deposit thin metal films on silicon wafers, which are then etched into conductive lines for microchips.
- Optics: The process is used to create anti-reflective coatings on lenses and mirrors, enhancing their optical properties.
- Automotive and Cookware: Sputtering is employed to apply durable, corrosion-resistant coatings on aluminum wheels and cookware, improving their appearance and performance.
- Solar Panels: Sputtering is used to deposit thin films on solar panels, enhancing their efficiency and durability.
-
Historical Context:
- Sputtering has been used commercially since the early 20th century, with Thomas Edison being one of the first to apply it to wax phonograph recordings in 1904.
- Over time, the technique has evolved, with variations like anodizing being developed to create uniform, shiny surfaces on aluminum products.
-
Process Details:
- Vacuum Chamber: The process takes place in a vacuum chamber to minimize contamination and ensure a clean deposition environment.
- Plasma Generation: A cathode is electrically energized to generate a plasma, ionizing the inert gas (usually argon) and creating a glow discharge.
- Energy Transfer: The ions are accelerated towards the target, transferring their energy and ejecting neutral particles from the target material.
- Deposition: The ejected particles traverse the vacuum and deposit onto the substrate, forming a thin film.
-
Material Considerations:
- Target Material: The choice of target material depends on the desired properties of the thin film, such as conductivity, reflectivity, or durability.
- Substrate Compatibility: Sputtering is suitable for a wide range of substrates, including silicon wafers, glass, and metals, making it a versatile deposition method.
-
Environmental and Operational Benefits:
- Low Temperature: Sputtering can be performed at relatively low temperatures, making it suitable for temperature-sensitive substrates.
- Scalability: The process can be scaled for mass production, allowing for the efficient coating of large numbers of substrates.
In summary, sputtering is a highly effective and versatile thin-film deposition technique with numerous advantages, including uniformity, precision, and the ability to deposit films at low temperatures. Its applications span a wide range of industries, from semiconductors to consumer goods, making it an essential process in modern manufacturing and technology.
Summary Table:
Key Aspect | Details |
---|---|
Mechanism | Bombarding a target with high-energy ions in a vacuum chamber. |
Advantages | Uniformity, precision, low-temperature deposition, and material versatility. |
Applications | Semiconductors, optics, automotive, cookware, and solar panels. |
Environmental Benefits | Low-temperature operation and scalability for mass production. |
Interested in sputtering for your manufacturing needs? Contact us today to learn more!