Sputter coating is a widely used technique in materials science and microscopy, primarily for creating thin, uniform films on surfaces. It is particularly valuable in scanning electron microscopy (SEM) for improving image quality by reducing charging effects and enhancing conductivity. The process involves using inert gases like argon to create a glow discharge, which sputters target material onto a substrate. This method is versatile, allowing the deposition of conductive and insulating materials, and is essential for analyzing beam-sensitive or non-conductive samples. Sputter coating has evolved from simple DC diode systems to more advanced techniques like reactive sputtering, which enables the deposition of oxides and nitrides at higher rates.
Key Points Explained:
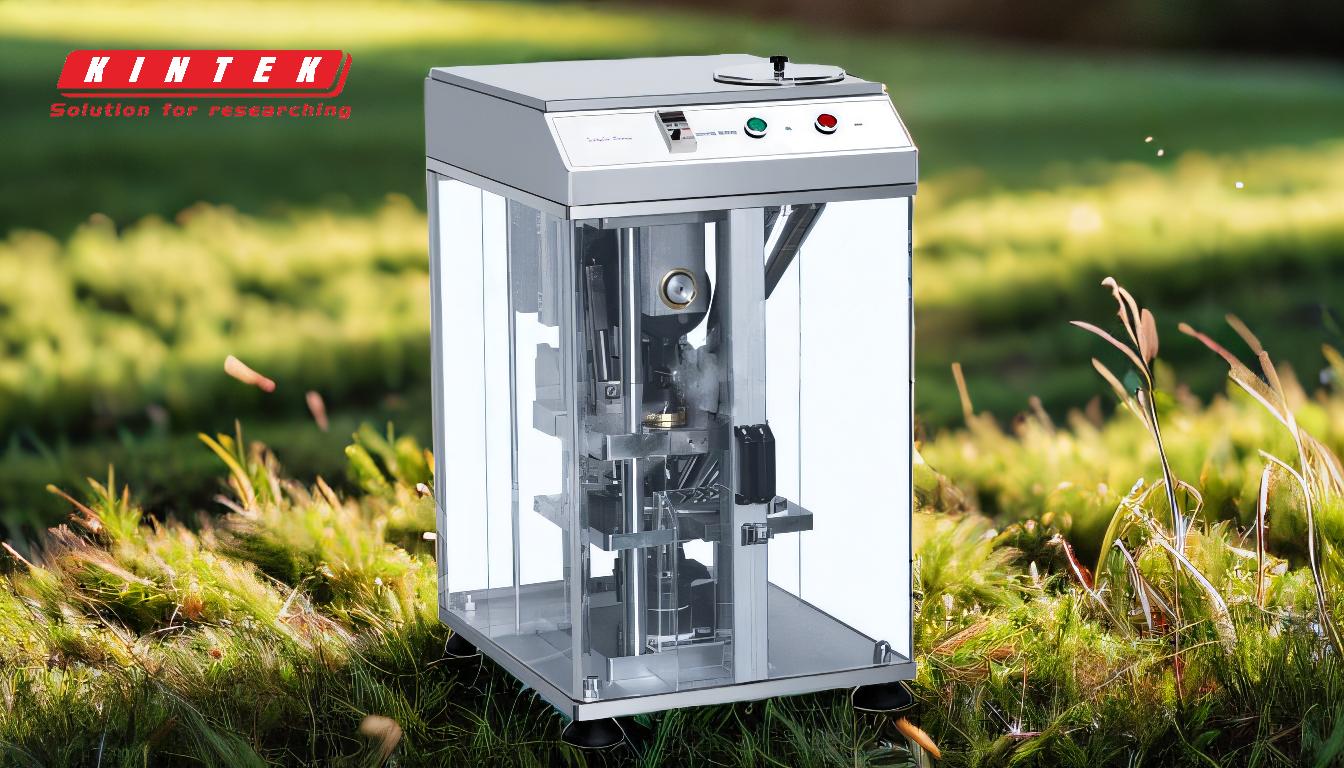
-
Improvement of SEM Imaging Quality:
- Sputter coating is crucial in SEM for enhancing the signal-to-noise ratio, leading to clearer and more detailed images. This is especially important for beam-sensitive samples, which can be damaged by the electron beam, and non-conductive materials, which tend to accumulate electrons, causing charging effects that distort the image. By applying a thin conductive layer, sputter coating mitigates these issues, ensuring accurate and high-quality imaging.
-
Versatility in Material Deposition:
- Sputter coating can deposit a wide range of materials, including metals, oxides, and nitrides. Reactive sputtering, for instance, allows the deposition of oxides or nitrides by sputtering a metal target in the presence of a reactive gas. This versatility makes sputter coating suitable for various applications, from creating conductive layers to forming protective or functional coatings.
-
Process of Sputtering:
- The sputtering process involves accelerating ions of an inert gas, such as argon, into a target material. The target is eroded by these ions through energy transfer, and the ejected neutral particles from the target traverse and are deposited as a thin film onto the surface of the substrates. This process is essential for creating uniform and adherent thin films.
-
Use of Inert Gases:
- Inert gases like argon are used to create a glow discharge between the cathode and anode in the sputter coating process. The free ions and electrons in the gas are attracted to opposite electrodes, producing a small current. This process is critical for the sputtering of the cathode material and the subsequent deposition of the sputtered atoms onto the specimen.
-
Evolution of Sputter Coating Techniques:
- Sputter coating has evolved from simple DC diode sputtering, which has the advantage of a simple device but suffers from low deposition rates and the inability to sputter insulating materials. Improvements like DC triple sputtering and quadrupole sputtering were developed to enhance ionization and stabilize discharge, though these methods still face challenges like low plasma concentration and deposition rates. Reactive sputtering, on the other hand, offers higher deposition rates for oxides and nitrides compared to RF magnetron deposition.
-
Application in Nanotechnology:
- The sputter coating process involves taking a solid material and using nanotechnology to turn it into microscopic particles. These particles are then applied to create a thin film on a given surface. This application is crucial in various fields, including electronics, optics, and materials science, where precise and uniform thin films are required.
In summary, sputter coating is an essential technique in modern materials science and microscopy, offering significant advantages in improving image quality, depositing a wide range of materials, and creating uniform thin films. Its evolution and versatility make it a valuable tool in both research and industrial applications.
Summary Table:
Key Aspect | Description |
---|---|
SEM Imaging Quality | Reduces charging effects, enhances conductivity, and improves signal-to-noise ratio. |
Material Deposition | Deposits conductive and insulating materials, including metals, oxides, and nitrides. |
Sputtering Process | Uses inert gases like argon to create thin, uniform films on substrates. |
Inert Gases | Argon creates a glow discharge, enabling efficient sputtering and deposition. |
Technique Evolution | Advanced methods like reactive sputtering offer higher deposition rates. |
Nanotechnology Applications | Creates precise, uniform thin films for electronics, optics, and materials science. |
Learn how sputter coating can elevate your research or industrial processes—contact our experts today!