Wet milling offers several advantages over dry milling, particularly in terms of efficiency, product quality, and cost-effectiveness. Wet milling processes, especially when using horizontal mills, are designed to maximize output while minimizing waste and operational costs. They are highly efficient, reduce product loss, and enhance the quality of the final product in terms of color strength, gloss, and durability. Additionally, wet milling reduces process time significantly, lowers raw material costs, and ensures minimal contamination and solvent loss. These benefits make wet milling a preferable choice for industries requiring high-quality outputs with consistent performance.
Key Points Explained:
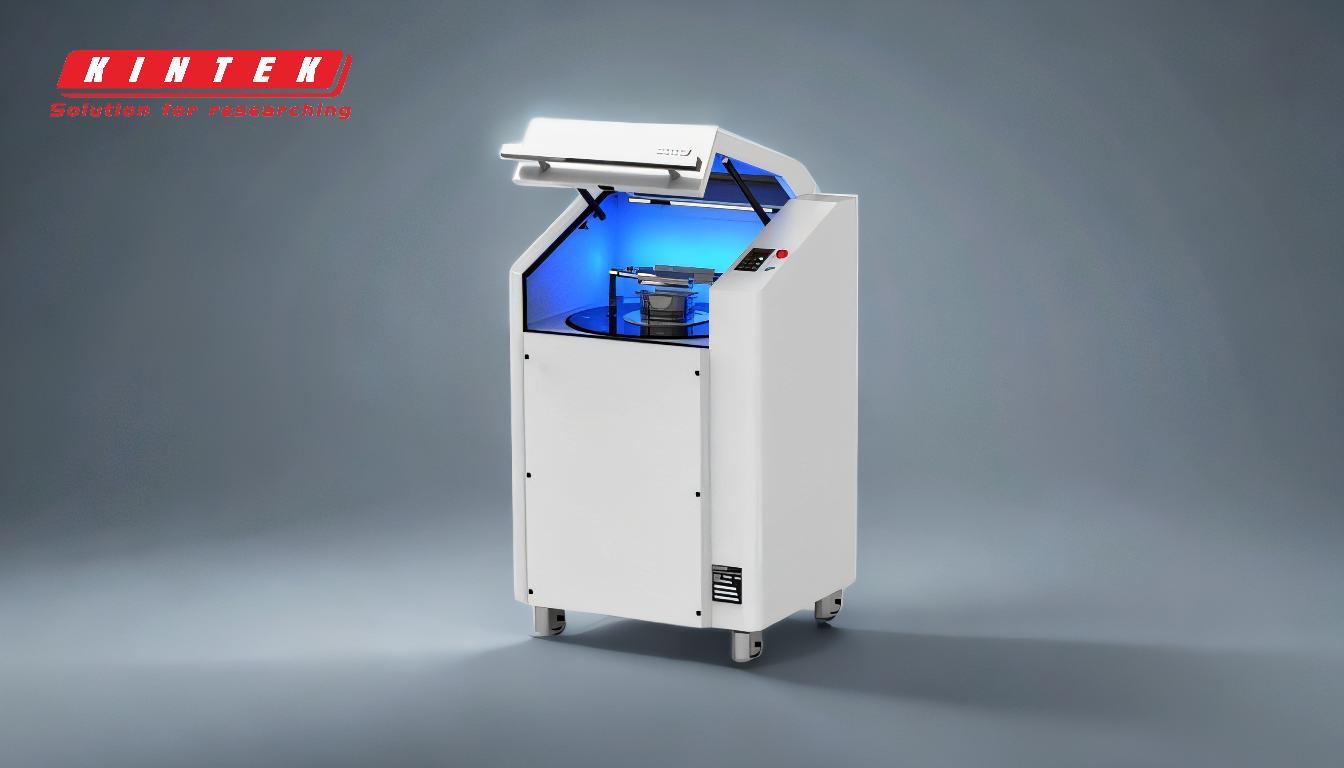
-
Efficient Use of Media:
- Wet milling utilizes small amounts of grinding media (0.25 mm to 2 mm), which is highly efficient. This precision allows for better control over the milling process, ensuring that the desired particle size is achieved with minimal waste.
- The efficient use of media also translates to cost savings, as less material is required to achieve the same or better results compared to dry milling.
-
Reduction in Product Loss:
- Wet milling significantly reduces product loss. The liquid medium helps in capturing fine particles that might otherwise be lost in dry milling processes. This is particularly beneficial in industries where the cost of raw materials is high.
- The reduction in product loss also contributes to higher yields, making the process more economical.
-
Enhanced Product Quality:
- Wet milling enhances the quality of the final product by maximizing color strength, gloss, and durability. These attributes are crucial in industries such as paints, coatings, and pharmaceuticals, where product appearance and performance are critical.
- The consistent and predictable performance of wet milling ensures that each batch meets the required quality standards, reducing the need for rework or quality control adjustments.
-
Reduced Process Time:
- Wet milling can reduce process time by up to 300%. This dramatic reduction is due to the efficient grinding action of the wet media, which breaks down materials more quickly than dry milling.
- Faster processing times lead to increased throughput and productivity, allowing manufacturers to meet higher demand without compromising on quality.
-
Lower Raw Material Costs:
- Wet milling reduces raw material costs by about 5%. This is achieved through the efficient use of media and the reduction in product loss, which means less raw material is needed to produce the same amount of product.
- Lower raw material costs contribute to overall cost savings, making wet milling a more cost-effective option in the long run.
-
Minimal Contamination and Solvent Loss:
- Wet milling processes are designed to minimize contamination and solvent loss. The liquid medium helps to keep the milling environment clean, reducing the risk of contamination from external sources.
- Minimal solvent loss also means that less solvent is needed to maintain the milling process, further reducing costs and environmental impact.
-
Resistance to Abrasion:
- Wet milling equipment is resistant to abrasion, which extends the lifespan of the machinery. This resistance is particularly important when processing hard or abrasive materials, which can wear down equipment quickly in dry milling processes.
- Longer equipment lifespan reduces maintenance costs and downtime, contributing to overall operational efficiency.
-
Low Operation, Control, and Maintenance Requirements:
- Wet milling systems have relatively low operation, control, and maintenance requirements. This simplicity makes them easier to operate and maintain, reducing the need for specialized skills or extensive training.
- Lower maintenance requirements also mean less downtime and higher overall productivity.
-
Consistent and Predictable Performance:
- Wet milling offers consistent and predictable performance, ensuring that each batch of product meets the required specifications. This consistency is crucial for maintaining quality standards and customer satisfaction.
- Predictable performance also reduces the risk of production delays or quality issues, which can be costly and time-consuming to resolve.
-
Versatility and Limitations of Combination Dry/Wet Milling:
- While combination dry/wet milling machines offer versatility by being able to process both soft and hard materials, they have limitations such as non-productive time during switching between methods and higher initial investment costs.
- In some cases, dedicated wet milling machines may offer better production efficiency and cost-effectiveness, especially when the primary need is for wet milling processes.
In summary, wet milling, particularly with horizontal mills, provides a range of benefits that make it a superior choice for many industrial applications. These benefits include efficient media use, reduced product loss, enhanced product quality, faster processing times, lower raw material costs, minimal contamination, abrasion resistance, low maintenance requirements, and consistent performance. While combination dry/wet milling machines offer some versatility, dedicated wet milling machines often provide better efficiency and cost-effectiveness for specific applications.
Summary Table:
Advantage | Key Benefit |
---|---|
Efficient Use of Media | Reduces waste and costs with precise control over particle size. |
Reduction in Product Loss | Captures fine particles, increasing yield and reducing material costs. |
Enhanced Product Quality | Improves color strength, gloss, and durability for superior outputs. |
Reduced Process Time | Speeds up processing by up to 300%, boosting productivity. |
Lower Raw Material Costs | Cuts raw material expenses by 5% through efficient milling. |
Minimal Contamination and Solvent Loss | Ensures cleaner processes and reduces environmental impact. |
Resistance to Abrasion | Extends equipment lifespan, reducing maintenance costs. |
Low Operation and Maintenance | Simplifies operation and reduces downtime. |
Consistent Performance | Delivers predictable results, ensuring quality and customer satisfaction. |
Ready to enhance your milling process? Contact us today to learn more about wet milling solutions!