Sifting, or sieving, is a critical process in various industries, particularly in food processing, pharmaceuticals, and materials science. It ensures the separation of particles based on size, which is essential for achieving uniformity, quality, and consistency in the final product. Sieving removes impurities, prevents clumping, and ensures that materials meet specific size requirements, which is vital for functionality, safety, and regulatory compliance. Additionally, sieving can improve the efficiency of downstream processes, such as mixing, packaging, or chemical reactions, by ensuring that materials are of the correct size and free from contaminants.
Key Points Explained:
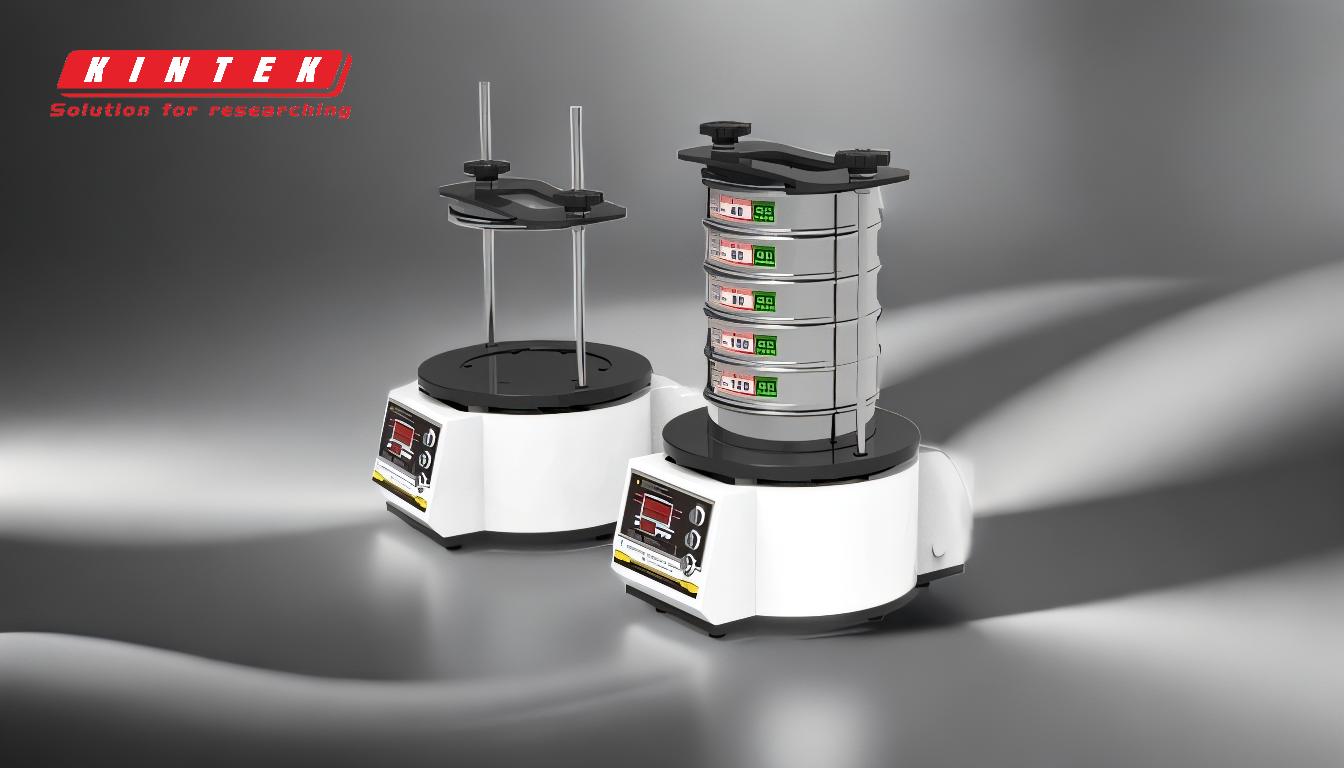
-
Ensures Uniform Particle Size:
- Sieving separates particles by size, ensuring that the final product has a consistent and uniform particle size distribution.
- Uniformity is critical in industries like food processing, where consistent texture and appearance are essential for consumer satisfaction.
- In pharmaceuticals, uniform particle size ensures accurate dosing and proper dissolution rates for medications.
-
Removes Impurities and Contaminants:
- Sieving helps remove unwanted materials, such as foreign particles, oversized clumps, or undersized fines, which could compromise product quality.
- In food processing, sieving eliminates contaminants like dirt, stones, or metal fragments, ensuring food safety.
- In industries like construction or ceramics, sieving removes debris that could weaken the final product.
-
Prevents Clumping and Agglomeration:
- Many powdered or granular materials tend to clump due to moisture, static, or other factors.
- Sieving breaks up these clumps, ensuring a free-flowing material that is easier to handle, mix, or package.
- This is particularly important in industries like cosmetics or pharmaceuticals, where clumping can affect product performance.
-
Improves Downstream Process Efficiency:
- Sieving ensures that materials are of the correct size and consistency before they enter subsequent processes like mixing, blending, or packaging.
- For example, in chemical manufacturing, sieving ensures that reactants are of the correct size, which can improve reaction rates and yields.
- In food processing, sieving ensures that ingredients mix evenly, leading to consistent product quality.
-
Meets Regulatory and Quality Standards:
- Many industries have strict regulations regarding particle size and purity. Sieving helps ensure compliance with these standards.
- For example, pharmaceutical products must meet specific size requirements to ensure safety and efficacy.
- In food processing, sieving is often required to meet hygiene and safety standards.
-
Enhances Product Performance:
- In industries like ceramics or construction, the size of particles directly affects the strength and durability of the final product.
- Sieving ensures that materials meet the required specifications, leading to better performance and longer-lasting products.
- In cosmetics, sieving ensures that powders are fine and smooth, improving application and customer satisfaction.
-
Reduces Waste and Saves Costs:
- By removing oversized or undersized particles, sieving minimizes waste and ensures that only usable material is processed further.
- This can lead to significant cost savings, especially in industries where raw materials are expensive.
- Additionally, sieving can reduce the risk of product recalls or rework due to quality issues.
-
Customizable for Specific Applications:
- Sieving can be tailored to meet the specific needs of different industries and applications.
- For example, fine sieves are used for powders in cosmetics, while coarser sieves are used for aggregates in construction.
- The ability to customize sieve sizes and configurations makes sieving a versatile and adaptable process.
-
Ensures Safety in Certain Applications:
- In industries like mining or construction, sieving removes oversized or hazardous materials that could pose safety risks.
- For example, sieving aggregates in construction ensures that no large rocks or debris are present, reducing the risk of accidents.
-
Facilitates Quality Control:
- Sieving is often used as a quality control measure to ensure that products meet specified standards before they are released to the market.
- By regularly sieving materials, manufacturers can identify and address any issues early in the production process, reducing the risk of defects.
By understanding the importance of sieving, equipment and consumable purchasers can make informed decisions about the types of sieves and screening equipment needed for their specific applications. This ensures that they achieve the desired product quality, efficiency, and compliance with industry standards.
Summary Table:
Key Benefit | Description |
---|---|
Ensures Uniform Particle Size | Achieves consistent particle size for better product quality and performance. |
Removes Impurities | Eliminates contaminants like dirt, stones, and metal fragments for safety. |
Prevents Clumping | Breaks up clumps for free-flowing materials, ideal for handling and packaging. |
Improves Downstream Efficiency | Ensures correct particle size for mixing, blending, and chemical reactions. |
Meets Regulatory Standards | Complies with industry regulations for particle size and purity. |
Enhances Product Performance | Ensures materials meet specifications for strength, durability, and application. |
Reduces Waste and Saves Costs | Minimizes waste by removing unusable particles, leading to cost savings. |
Customizable for Applications | Adapts to specific needs, from fine powders to coarse aggregates. |
Ensures Safety | Removes hazardous materials, reducing risks in industries like mining. |
Facilitates Quality Control | Acts as a quality control measure to identify and address defects early. |
Upgrade your sieving process for better quality and efficiency—contact our experts today!