Sputtering is a highly advantageous technique for alloy deposition due to its ability to handle materials with very high melting points, maintain the composition of the source material, and provide excellent adhesion to substrates. It is also cost-effective, maintenance-free, and suitable for ultrahigh vacuum applications. The process involves bombarding a target material with high-energy ions, typically argon, to eject atoms that then deposit onto a substrate. This method allows for precise atomic-level film deposition, better surface adhesion, and more uniform films. Additionally, sputtering can be performed in various configurations, including top-down and bottom-up, making it versatile for different applications.
Key Points Explained:
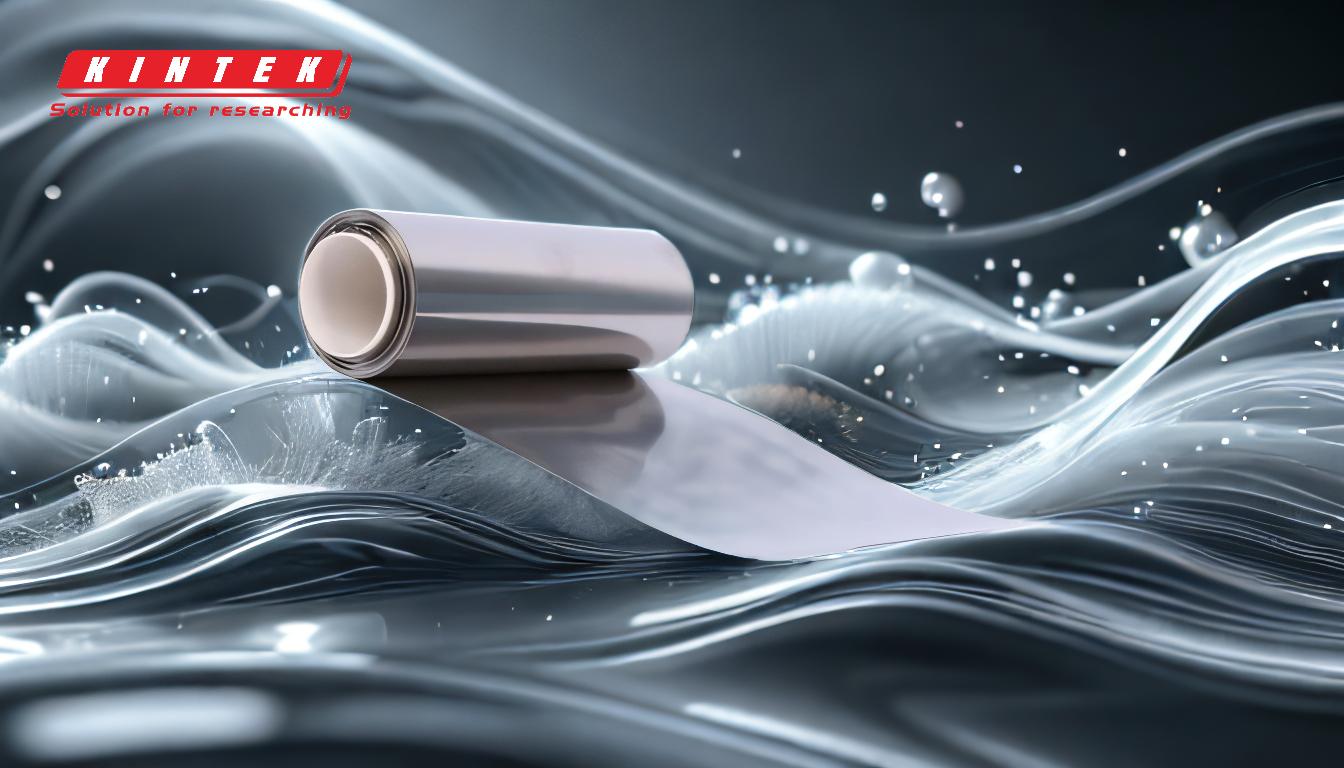
-
Handling High Melting Point Materials:
- Sputtering is particularly useful for depositing materials with very high melting points, such as tantalum (2998°C), which are difficult or impossible to evaporate using other methods. This capability makes sputtering ideal for depositing alloys that include refractory metals.
-
Maintaining Composition:
- The composition of sputter-deposited films closely matches that of the source material. This is crucial for alloy deposition, where maintaining the exact ratio of different elements is essential for achieving the desired material properties.
-
Better Adhesion:
- Sputtered films exhibit better adhesion to substrates compared to evaporated films. The high kinetic energy of sputter-ejected atoms results in stronger bonding with the substrate, which is particularly important for applications requiring durable and long-lasting coatings.
-
Versatility in Deposition Configurations:
- Unlike evaporation deposition, which is typically limited to bottom-up configurations, sputtering can be performed both top-down and bottom-up. This flexibility allows for more complex and varied deposition setups, accommodating different substrate geometries and application requirements.
-
Uniform and Dense Films:
- Sputtering produces more uniform films with higher packing densities, even at low temperatures. This uniformity is beneficial for creating consistent and reliable alloy coatings, which are essential for applications in electronics, optics, and protective coatings.
-
Wide Range of Materials:
- Sputtering can be used with a broad range of materials, including diverse mixtures and alloys. This versatility makes it suitable for depositing complex alloys that may include multiple elements with different properties.
-
Cost-Effectiveness and Maintenance:
- Sputter deposition is relatively inexpensive compared to other deposition processes and is maintenance-free. This makes it a practical choice for industrial applications where cost and reliability are critical factors.
-
Suitable for Ultrahigh Vacuum Applications:
- The sputtering process is compatible with ultrahigh vacuum environments, which are necessary for certain high-precision applications, such as semiconductor manufacturing and advanced material research.
-
Reactive Deposition:
- Sputtering allows for reactive deposition using reactive gaseous species, enabling the creation of compound films with specific chemical properties. This is particularly useful for depositing alloys that require precise chemical compositions.
-
Minimal Radiant Heat:
- The sputtering process generates very little radiant heat, which is beneficial for temperature-sensitive substrates. This feature allows for the deposition of alloys on materials that might be damaged by the high temperatures associated with other deposition methods.
In summary, sputtering is a highly effective and versatile method for alloy deposition, offering numerous advantages such as handling high melting point materials, maintaining precise compositions, providing excellent adhesion, and producing uniform, dense films. Its cost-effectiveness, maintenance-free operation, and compatibility with ultrahigh vacuum applications further enhance its utility in various industrial and research settings.
Summary Table:
Advantage | Description |
---|---|
Handles High Melting Points | Ideal for refractory metals like tantalum (2998°C). |
Maintains Composition | Films match source material, crucial for precise alloy ratios. |
Better Adhesion | Stronger bonding due to high kinetic energy of sputtered atoms. |
Versatile Configurations | Top-down and bottom-up setups for diverse applications. |
Uniform and Dense Films | Produces consistent, high-density coatings, even at low temperatures. |
Wide Range of Materials | Suitable for complex alloys with multiple elements. |
Cost-Effective & Maintenance-Free | Affordable and reliable for industrial use. |
Ultrahigh Vacuum Compatibility | Perfect for semiconductor manufacturing and advanced research. |
Reactive Deposition | Enables precise chemical compositions using reactive gases. |
Minimal Radiant Heat | Safe for temperature-sensitive substrates. |
Ready to enhance your alloy deposition process? Contact our experts today to learn more about sputtering solutions!