RF sputtering is a widely used technique in thin film deposition, particularly for non-conductive (dielectric) materials, due to its ability to overcome the limitations of DC sputtering. By using an alternating current (AC) power source at a frequency of 13.56 MHz, RF sputtering prevents charge buildup on insulating targets, sustains plasma at low pressures, and reduces arcing. This method ensures uniform film deposition, minimizes target erosion, and avoids issues like the disappearing anode effect. RF sputtering is highly versatile, enabling the deposition of a wide range of materials, including insulators, metals, alloys, and composites, with improved film quality and step coverage.
Key Points Explained:
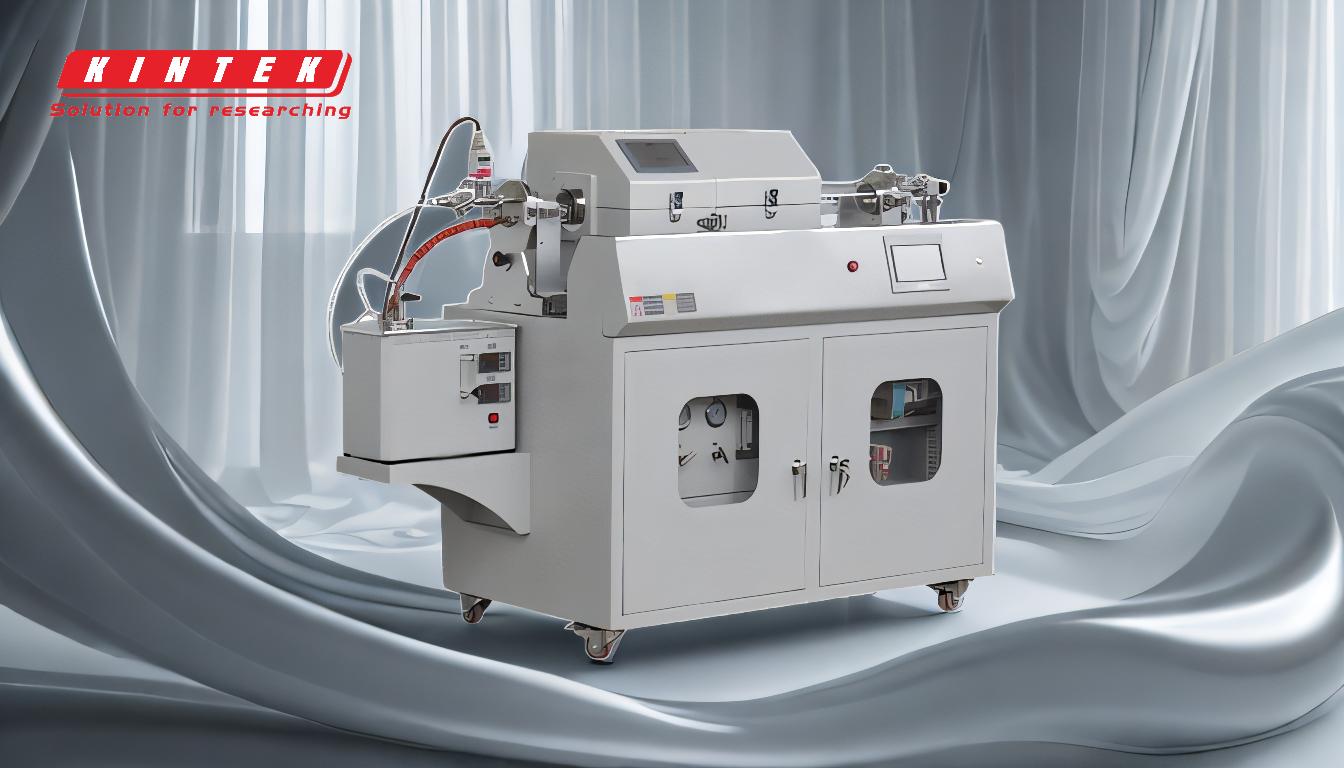
-
Overcoming Limitations of DC Sputtering:
- DC sputtering is effective for conductive materials but fails with non-conductive (dielectric) targets due to surface charging. Positive ions bombarding the target cause charge buildup, repelling further ions and halting the sputtering process.
- RF sputtering uses an AC power source at 13.56 MHz to alternate the polarity of the target, preventing charge buildup and enabling the deposition of insulating materials.
-
Mechanism of RF Sputtering:
- The target material and substrate holder act as two electrodes. Electrons oscillate between these electrodes at the applied RF frequency.
- In the positive half-cycle, the target acts as an anode, attracting electrons.
- In the negative half-cycle, the target becomes a cathode, ejecting gas ions and target atoms toward the substrate to form a thin film.
-
Advantages of RF Sputtering:
- Versatility: RF sputtering can deposit a wide variety of materials, including insulators, metals, alloys, and composites.
- Uniform Film Deposition: The alternating field reduces arcing and charge buildup, leading to more uniform films.
- Low-Pressure Operation: Plasma can be sustained at low pressures (1-15 mTorr), reducing ionized gas collisions and improving deposition efficiency.
- Minimized Target Erosion: RF sputtering reduces "racetrack erosion" and avoids the disappearing anode effect seen in DC sputtering.
-
Improved Performance with RF Diode Sputtering:
- Recent advancements in RF diode sputtering eliminate the need for magnetic confinement and provide better coating uniformity.
- This technology results in flat target erosion, no racetrack formation, no target poisoning, minimal arcing, and a stable process.
-
Applications in Industry:
- RF sputtering is commonly used in the computer and semiconductor industries to create thin films for electronic components.
- It is particularly effective for depositing dielectric materials, which are essential for insulating layers in microelectronics.
-
Process Stability and Efficiency:
- The alternating electrical field prevents ion buildup on insulating targets, ensuring continuous ion bombardment and a stable sputtering process.
- RF sputtering operates efficiently at low pressures, reducing energy loss due to gas collisions and enhancing deposition rates.
By addressing the limitations of DC sputtering and leveraging the unique advantages of AC power, RF sputtering has become a critical technology for depositing high-quality thin films, especially for non-conductive materials. Its ability to sustain plasma at low pressures, reduce arcing, and ensure uniform film deposition makes it indispensable in modern manufacturing and semiconductor industries.
Summary Table:
Aspect | Details |
---|---|
Mechanism | Uses AC power at 13.56 MHz to alternate polarity, preventing charge buildup. |
Advantages | Versatile, uniform deposition, low-pressure operation, minimized erosion. |
Applications | Widely used in semiconductor and computer industries for dielectric films. |
Key Benefit | Sustains plasma at low pressures, reduces arcing, and ensures film uniformity. |
Learn how RF sputtering can enhance your thin film processes—contact our experts today!