Sputter coating is a critical step in preparing specimens for scanning electron microscopy (SEM), particularly for non-conductive or beam-sensitive materials. It involves depositing a thin, conductive layer of metal (such as gold, platinum, or iridium) onto the specimen to enhance imaging quality. This process prevents charging effects, reduces thermal damage, and improves the signal-to-noise ratio, resulting in clearer and more detailed SEM images. Additionally, sputter coating ensures a uniform and durable conductive layer, making it an essential technique for accurate and high-quality SEM analysis.
Key Points Explained:
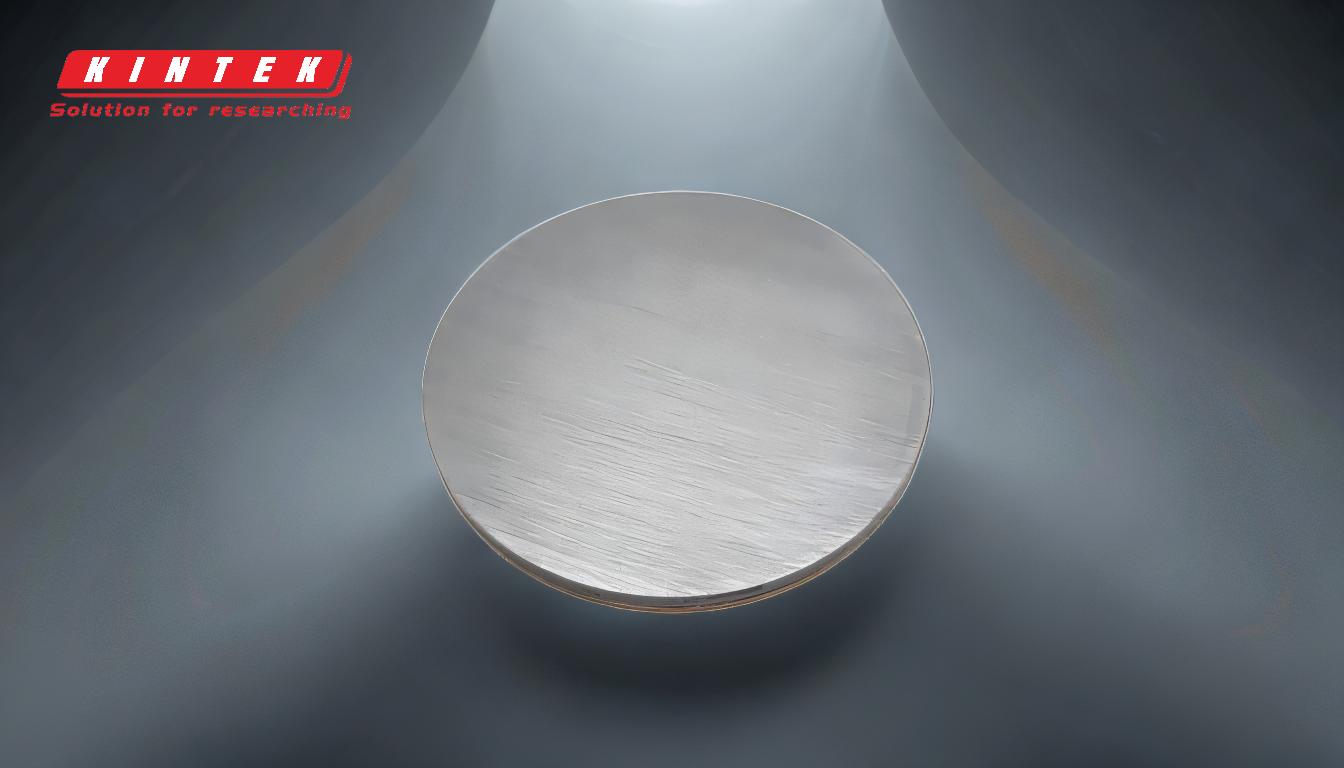
-
Prevention of Charging Effects:
- Non-conductive or poorly conductive materials can accumulate electrons from the SEM's electron beam, leading to charging effects. These effects distort the image and make accurate analysis difficult.
- Sputter coating applies a conductive layer to the specimen, which grounds the surface and prevents electron buildup. This ensures stable imaging without artifacts caused by charging.
-
Enhancement of Signal-to-Noise Ratio:
- The conductive layer improves the emission of secondary electrons from the specimen's surface, which are crucial for creating high-resolution SEM images.
- By enhancing the secondary electron signal, sputter coating increases the signal-to-noise ratio, resulting in sharper and more detailed images.
-
Protection of Beam-Sensitive Materials:
- Some materials are sensitive to the electron beam and can be damaged during SEM imaging. The conductive coating acts as a protective layer, dissipating heat and reducing the risk of thermal damage.
- This is particularly important for biological samples, polymers, and other delicate materials that might degrade under the electron beam.
-
Improved Topographic Examination:
- The thin, uniform conductive layer highlights the surface features of the specimen, making it easier to examine its topography.
- Metals like gold, platinum, and iridium are commonly used because they provide excellent conductivity and produce high-quality secondary electron signals.
-
Uniform and Durable Coating:
- Sputter coating creates a stable plasma environment, ensuring a consistent and even deposition of the conductive material.
- The coating bonds at an atomic level with the substrate, making it durable and long-lasting, unlike surface-applied layers that might peel or degrade.
-
Essential for Non-Conductive Samples:
- Non-conductive materials, such as ceramics, plastics, and biological tissues, require sputter coating to make them suitable for SEM analysis.
- Without this step, these materials would not produce usable images due to charging and poor electron emission.
-
Wide Range of Applications:
- Sputter coating is used across various fields, including materials science, biology, and nanotechnology, to prepare samples for SEM imaging.
- It is a versatile technique that can be tailored to different materials and research needs by selecting appropriate coating materials and thicknesses.
By addressing these key points, sputter coating ensures that specimens are prepared optimally for SEM analysis, enabling researchers to obtain accurate, high-quality images and reliable data.
Summary Table:
Key Benefits of Sputter Coating | Description |
---|---|
Prevents Charging Effects | Grounds the surface to avoid electron buildup, ensuring stable imaging. |
Enhances Signal-to-Noise Ratio | Improves secondary electron emission for sharper, detailed SEM images. |
Protects Beam-Sensitive Materials | Dissipates heat, reducing thermal damage to delicate samples. |
Improves Topographic Examination | Highlights surface features for better topographical analysis. |
Ensures Uniform & Durable Coating | Creates a consistent, long-lasting conductive layer. |
Essential for Non-Conductive Samples | Makes materials like ceramics and plastics suitable for SEM. |
Wide Range of Applications | Used in materials science, biology, and nanotechnology. |
Ready to optimize your SEM imaging? Contact us today to learn more about sputter coating solutions!