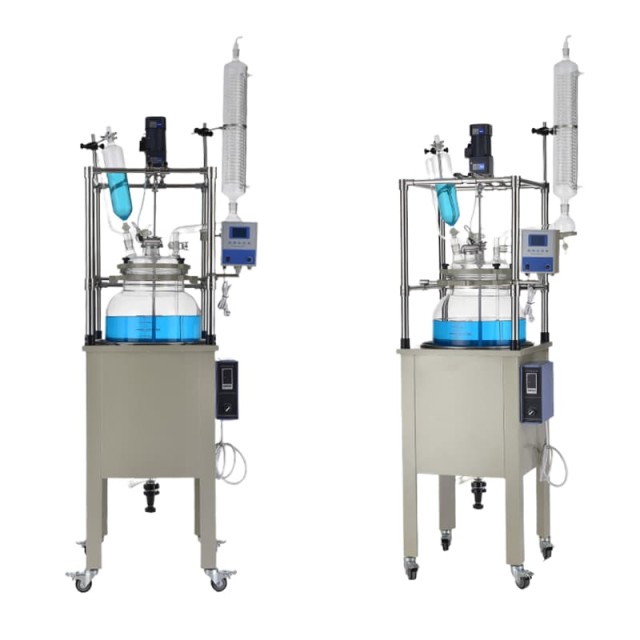
Glass Reactor
80-150L Single Jacketed Glass Reactor Vessel for Lab Use
Item Number : KR-80S
Price varies based on specs and customizations
- Reactor Volume
- 80-150 L
- Max. Torgue
- 378-425 N/cm
- Stirring Speed
- 0-650 rpm
- Working temperature
- -80~250 ℃
- Vacuum
- 0.098 Mpa
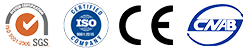
Shipping:
Contact us to get shipping details Enjoy On-time Dispatch Guarantee.
Applications
Glass reactor system combines the glassware vessel, speed controlled stirring, controlled temperature heating or chilling, as while as filtering, lifting, or tilting mechanical functions, which creates an idea environment for the different target materials synthetic reaction, distillation, separation and filtration in the pharmaceutical, chemical, biological products and other industries.
KinTek glass reactors vessel volumes are from 1 liters to 200 liters,glassware can be single, double and triple jacketed, stirring system can be fixed speed or various speed adjustable, agitating shaft and impeller can be different materials or assembling, reactor assemble can be lift-able and tilt-able for convenient materials handling, standard input and output ports for heating or chilling circulating, also supply various optional functions like filtering assembling, anti-explosive controls, warm keep jacket, heating jacket and so on. Kindle tech also offer reactor custom tailor service, client just text us the working purpose and requests, we will work out detail plan proposals to our clients.
Features
![]() |
|
Technical specifications
Model | KGR-80 | KGR-100 | KGR-150 |
Reactor Volume | 80L | 100L | 150L |
Stirring Power | 370W | 370W | 400W |
Max. Torgue | 378N/cm | 378N/cm | 425N/cm |
Port Sealing | PTFE | ||
Speed Control | Knop Stepless Speed Regulation | ||
Stirring Speed | 0-650rpm | ||
Working temperature | -80~250℃ | ||
Vacuum | 0.098Mpa | ||
Safty Protection | Over-current/ ground fault/over-temperature protection | ||
Working Environment | 5-35℃ | ||
Power Supply | 110-440V, 50/60Hz | ||
Overall Dimensions | 700*630*2500 mm | 720*630*2700 mm | 750*660*2750 mm |
Net weight | 140kg | 160kg | 200kg |
Warnings
Operator safety is the top important issue! Please operate the equipment with cautions. Working with inflammable& explosive or toxic gases is very dangerous, operators must take all necessary precautions before starting the equipment. Working with positive pressure inside the reactors or chambers is dangerous, operator must fellow the safety procedures strictly. Extra caution must also be taken when operating with air-reactive materials, especially under vacuum. A leak can draw air into the apparatus and cause a violent reaction to occur.
Designed for You
KinTek provide deep custom made service and equipment to worldwide customers, our specialized teamwork and rich experienced engineers are capable to undertake the custom tailoring hardware and software equipment requirements, and help our customer to build up the exclusive and personalized equipment and solution!
Would you please drop your ideas to us, our engineers are ready for you now!
FAQ
What Is A Glass Reactor?
What Are The Advantages Of Glass Reactor?
What Material Is Glass Reactor?
What Are The Different Types Of Glass Reactors?
What Temperature Should A Glass Reactor Be?
4.7
out of
5
The glass reactor is a great piece of equipment. It's well-made and durable, and it provides accurate and reliable results.
4.9
out of
5
The glass reactor is easy to operate and maintain, and it's a great value for the price. I would definitely recommend it to anyone looking for a quality glass reactor.
4.8
out of
5
The glass reactor is a great tool for conducting chemical reactions. It's easy to use and clean, and it provides consistent results.
4.6
out of
5
The glass reactor is a great addition to our lab. It's helped us to improve the quality of our products and reduce our production costs.
4.9
out of
5
The glass reactor is a great investment for any lab. It's versatile, reliable, and easy to use.
4.7
out of
5
The glass reactor is a must-have for any lab. It's a great way to conduct chemical reactions and obtain accurate results.
4.8
out of
5
The glass reactor is a great tool for teaching chemistry. It's easy for students to use and understand, and it helps them to visualize chemical reactions.
4.9
out of
5
The glass reactor is a great tool for research. It's versatile and can be used for a variety of experiments.
4.7
out of
5
The glass reactor is a great tool for pilot plant studies. It's easy to scale up and can be used to produce large quantities of product.
4.8
out of
5
The glass reactor is a great tool for process development. It's easy to use and can be used to quickly evaluate different process conditions.
4.9
out of
5
The glass reactor is a great tool for quality control. It's accurate and reliable, and it can be used to test the quality of products.
4.7
out of
5
The glass reactor is a great tool for safety. It's designed to prevent accidents and protect users.
4.8
out of
5
The glass reactor is a great tool for environmental protection. It's energy-efficient and can be used to reduce waste.
4.9
out of
5
The glass reactor is a great tool for education. It's a great way to teach students about chemistry and chemical reactions.
4.7
out of
5
The glass reactor is a great tool for innovation. It's a great way to develop new products and processes.
Products
80-150L Single Jacketed Glass Reactor Vessel for Lab Use
REQUEST A QUOTE
Our professional team will reply to you within one business day. Please feel free to contact us!
Related Products
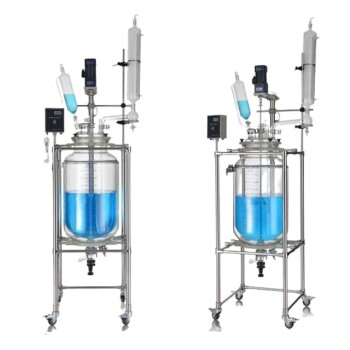
80-150L Jacketed Glass Reactor Vessel for Lab Applications
Looking for a versatile jacket glass reactor system for your lab? Our 80-150L reactor offers controlled temperature, speed, and mechanical functions for synthetic reactions, distillation, and more. With customizable options and tailored services, KinTek has you covered.
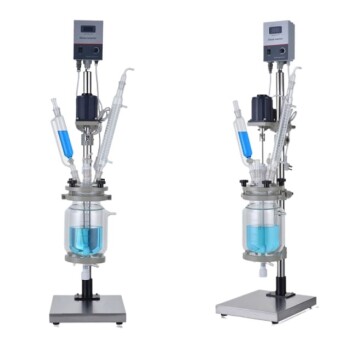
1-5L Jacketed Glass Reactor Vessel Lab Glass Reactor
Discover the perfect solution for your pharmaceutical, chemical, or biological products with our 1-5L jacket glass reactor system. Custom options available.

10-50L Single Jacketed Glass Reactor Vessel for Lab Applications
Looking for a reliable single glass reactor system for your lab? Our 10-50L reactor offers precise temperature and stirring control, durable support, and safety features for synthetic reactions, distillation, and more. KinTek's customizable options and tailored services are here to meet your needs.
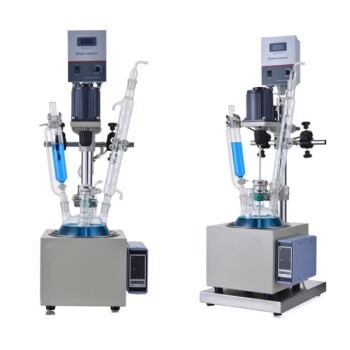
1-5L Single Jacketed Glass Reactor Vessel for Lab Use
Find your ideal glass reactor system for synthetic reactions, distillation, and filtration. Choose from 1-200L volumes, adjustable stirring and temperature control, and custom options. KinTek has you covered!
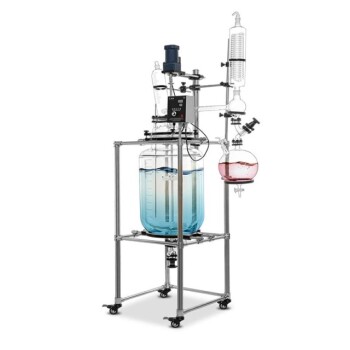
10-50L Jacketed Glass Reactor Vessel for Lab Applications
Discover the Versatile 10-50L Jacket Glass Reactor for Pharmaceutical, Chemical, and Biological Industries. Accurate Stirring Speed Control, Multiple Safety Protections, and Customizable Options Available. KinTek, Your Glass Reactor Partner.
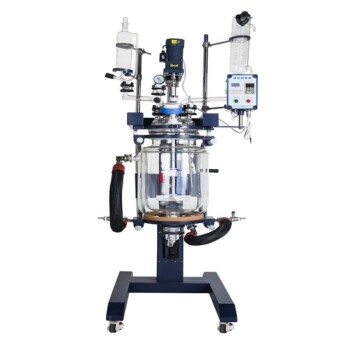
Lifting Tilting Jacketed Glass Reactor Vessel for Lab Use
Enhance your synthetic reactions, distillation, and filtration processes with our lifting/tilting glass reactor system. With a wide range of temperature adaptability, accurate stirring control, and solvent-resistant valves, our system guarantees stable and pure results. Explore the features and optional functions today!
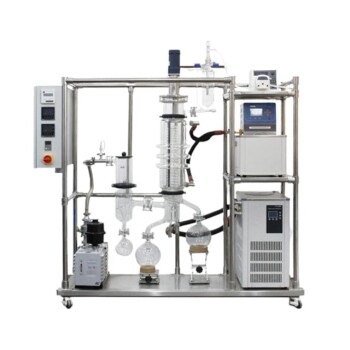
Molecular Distillation Equipment Short Path Molecular Distillation
Purify and concentrate natural products with ease using our molecular distillation process. With high vacuum pressure, low operating temperatures, and short heating times, preserve the natural quality of your materials while achieving excellent separation. Discover the advantages today!
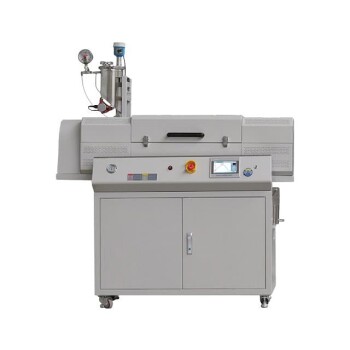
Laboratory Vacuum Tilt Rotary Tube Furnace Rotating Tube Furnace
Discover the versatility of Laboratory Rotary Furnace: Ideal for calcination, drying, sintering, and high-temperature reactions. Adjustable rotating and tilting functions for optimal heating. Suitable for vacuum and controlled atmosphere environments. Learn more now!
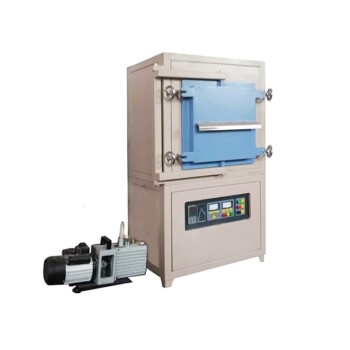
1700℃ Controlled Atmosphere Furnace Nitrogen Inert Atmosphere Furnace
KT-17A Controlled atmosphere furnace: 1700℃ heating, vacuum sealing technology, PID temperature control, and versatile TFT smart touch screen controller for laboratory and industrial use.
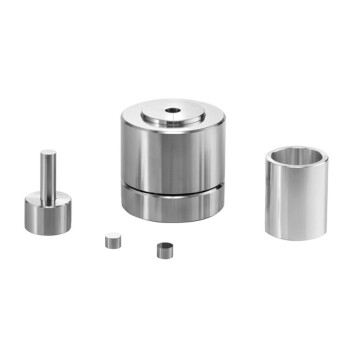
Assemble Lab Cylindrical Press Mold
Get reliable and precise molding with Assemble Lab Cylindrical Press Mold. Perfect for ultra-fine powder or delicate samples, widely used in material research and development.
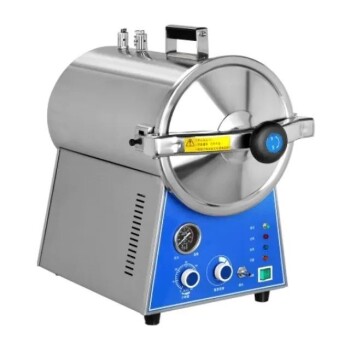
Desktop Fast High Pressure Laboratory Autoclave Sterilizer 16L 24L for Lab Use
The desktop fast steam sterilizer is a compact and reliable device used for rapid sterilization of medical, pharmaceutical, and research items.
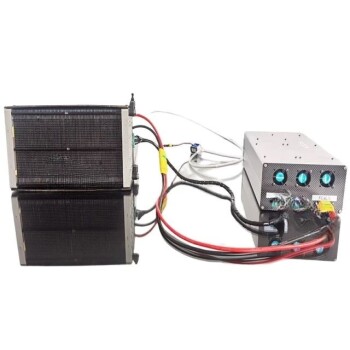
Hydrogen Fuel Cell Stack Battery Lab Equipment
A fuel cell stack is a modular, highly efficient way to generate electricity using hydrogen and oxygen through an electrochemical process. It can be used in various stationary and mobile applications as a clean and renewable energy source.
Related Articles
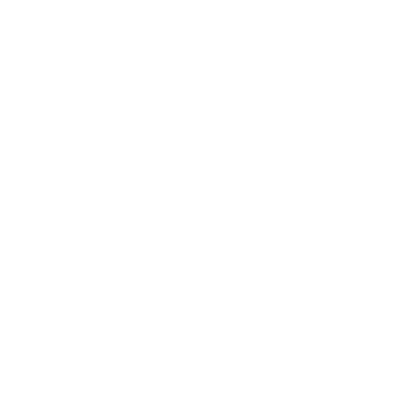
Enhancing Safety in Your Laboratory: A Comprehensive Guide to Pressure Reactor Safety
Laboratory safety isn't just about you. Improper preparation and mishandling can cause potential hazards that could be disastrous if left unchecked. It is crucial to take the time to carefully prepare your pressure reactor and lab safety equipment, as even minor problems can escalate quickly when working under pressure.
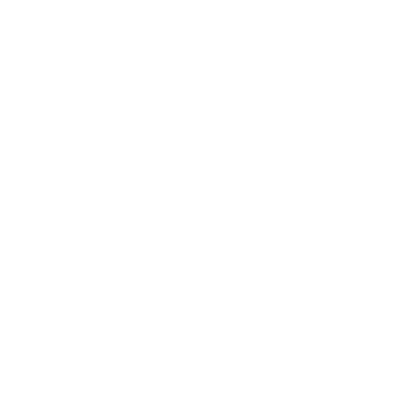
10 Essential Safety Steps for Pressure Reactor Use in Laboratories
Safety is paramount when conducting chemical reactions under pressurized conditions. It is important to carefully prepare pressure reactors and laboratory safety equipment to prevent potential hazards that, if not controlled, can have catastrophic consequences. In order to ensure the safety of using a pressure reactor, it is important to understand the specifications of the reactor. Become familiar with the chemistry of the reactor material and make sure it is chemically resistant enough to withstand the substances used in the reaction.
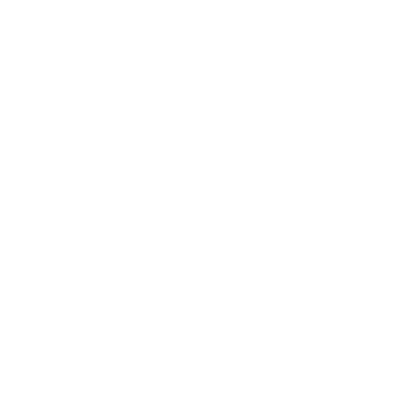
A Step-by-Step Guide to Cleaning Laboratory Glassware
Maintaining clean and sterile glassware is crucial in any laboratory setting. Not only is it important for the accuracy and reliability of experiments, it is also essential for the safety of those working in the lab.
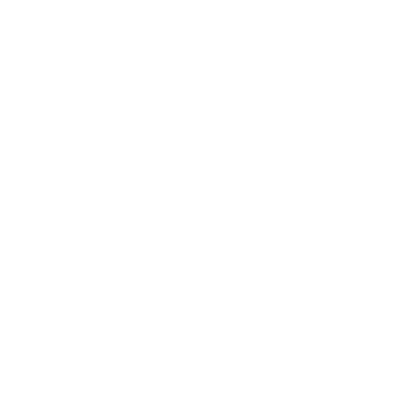
How To Clean Laboratory Glassware - Part 1
Cleaning laboratory glassware isn't as simple as washing the dishes. Here's how to wash your glassware so that you won't ruin your chemical solution or laboratory experiment.
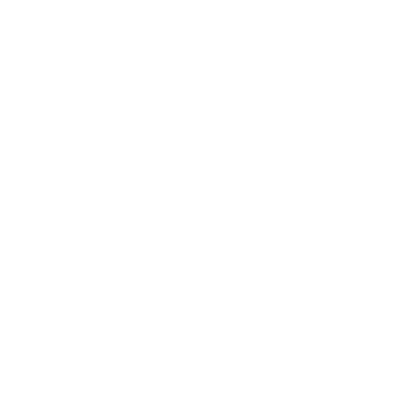
Glassware vs. Plasticware - Which is the Better Choice for Your Needs?
Both glassware and plasticware have their own advantages and disadvantages, and the choice between the two will depend on the specific needs of your laboratory.
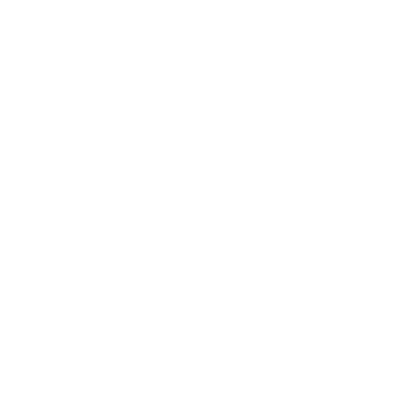
Safety Equipment In A Lab - Eye Protection
Safety glasses or chemical goggles must be donned before entering any wet bench lab, including cell culture labs. This applies to lab visitors, GT maintenance and custodial workers as well as staff and students.
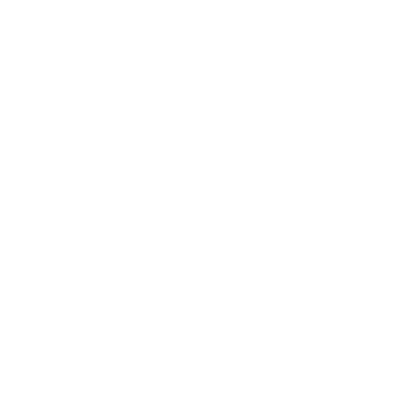
Exploring the Fundamentals of Good Laboratory Practice: Ensuring Quality, Integrity, and Safety in Scientific Research
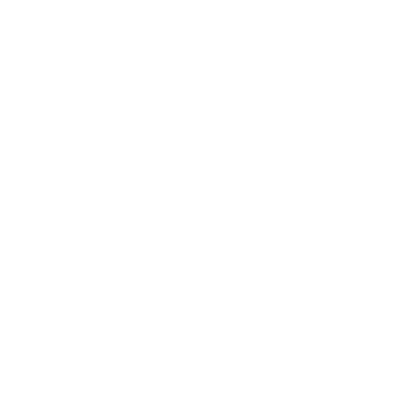
How to Save Money When Buying a Rotary Evaporator (Rotavapor)
A rotary evaporator, also known as a rotavapor, is a laboratory equipment commonly used to remove solvents from a sample. It works by rotating the sample flask to create a thin film of the solvent, which is then evaporated.
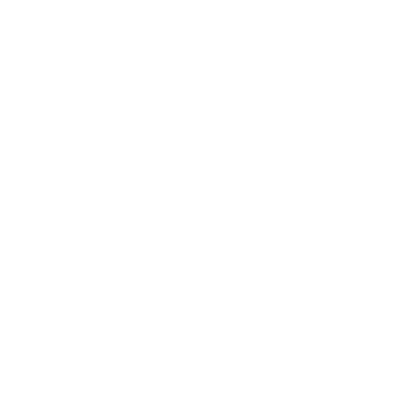
Mastering the Art of Rotary Evaporation
Rotary evaporation is a technique used in laboratories to remove solvents from samples through the process of evaporation.
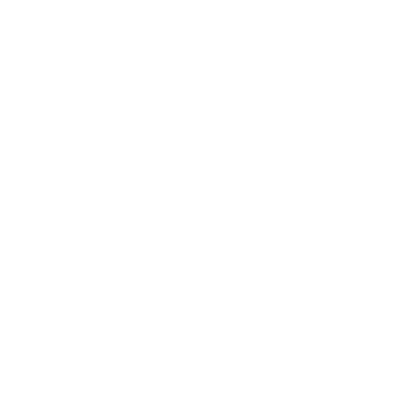
How to Choose the Best Rotary Evaporator (Rotavapor) for Your Budget
A rotary evaporator, also known as a rotavapor, is a laboratory equipment used for distillation, evaporation, and separation of solvents.
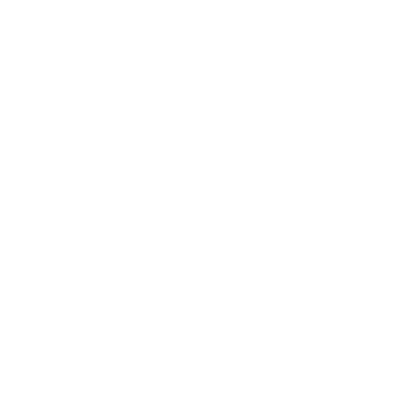
Welcome Our Canada Customers Visit Kindle Tech Group
Welcome our Canada customers visit Kindle Tech Group, customer satisfied with the workshop which strictly control the quality, technical team introduced all the procedure of the production.
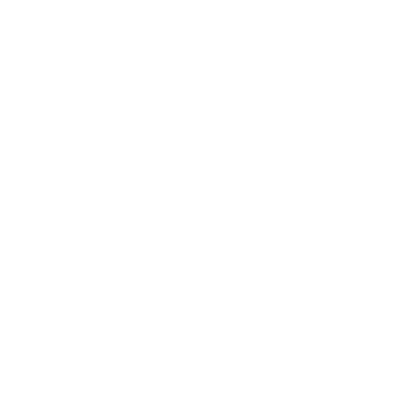
Unraveling The Mysteries of Rotary Evaporators Why They're Better
A rotary evaporator, or rotovap, is a laboratory equipment used for distillation of solvents and other compounds. It works by rotating the sample flask, while simultaneously heating it, to evaporate the solvent and separate it from the sample.