Ball mills are versatile grinding machines used in various industries, such as mining, ceramics, and cement production, to grind materials into fine powders. Whether a ball mill requires water depends on the type of grinding process being used: dry grinding or wet grinding. In dry grinding, no water is added, and the material is ground using only the mechanical action of the balls. In wet grinding, water or another liquid is added to the mill to form a slurry, which helps in grinding finer particles and reduces dust. The choice between dry and wet grinding depends on the material properties, desired particle size, and specific application requirements.
Key Points Explained:
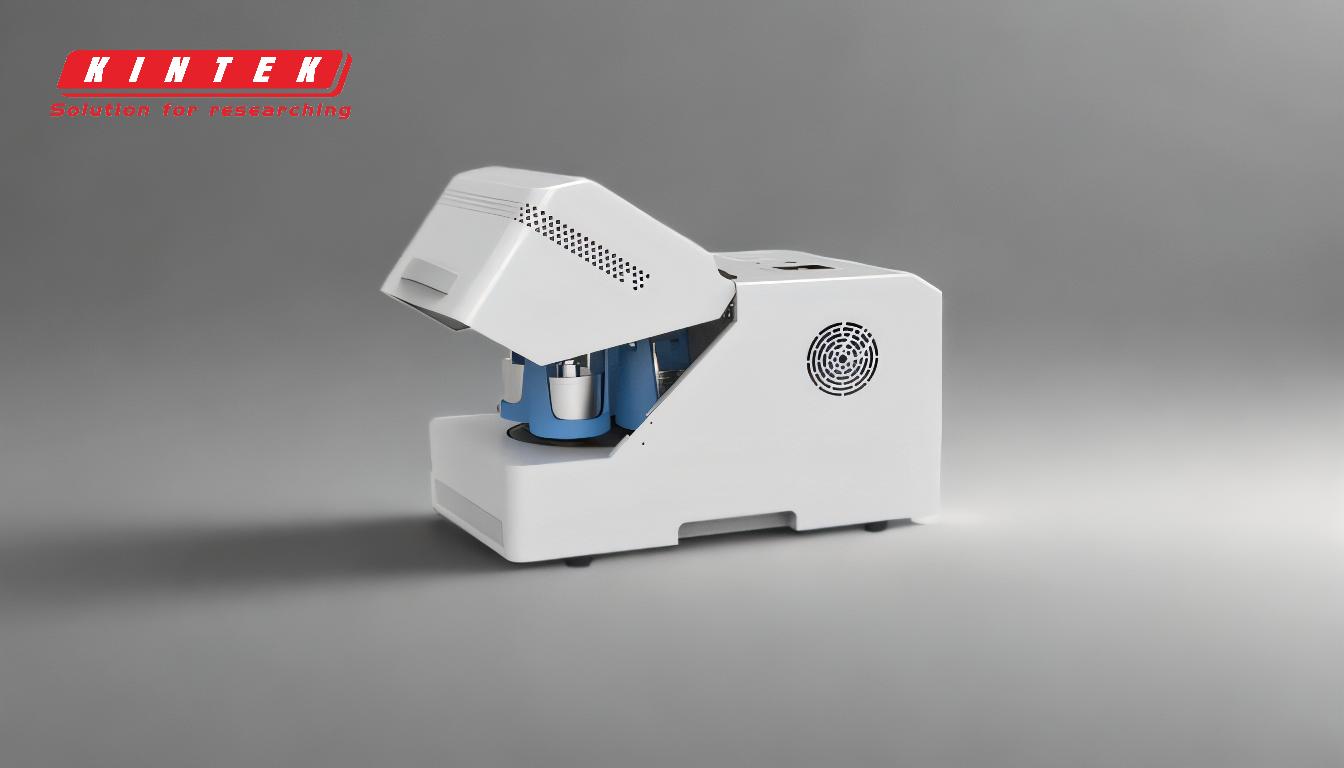
-
Types of Grinding Processes in Ball Mills:
- Dry Grinding: In this process, no water or liquid is added to the ball mill. The material is ground solely by the impact and friction of the grinding media (balls). Dry grinding is suitable for materials that do not require additional lubrication or cooling and is often used when the final product must be dry.
- Wet Grinding: Water or another liquid is added to the ball mill to form a slurry. The liquid helps in reducing dust, improving material flow, and achieving finer particle sizes. Wet grinding is commonly used for materials that are difficult to grind dry or when the final product needs to be in a slurry form.
-
Advantages of Wet Grinding:
- Finer Particle Size: The presence of water helps in breaking down particles more effectively, resulting in a finer grind.
- Dust Control: Wet grinding significantly reduces dust generation, making it safer and more environmentally friendly.
- Cooling Effect: Water acts as a coolant, preventing overheating of the material and the mill itself.
- Improved Material Flow: The slurry formed during wet grinding flows more easily through the mill, enhancing efficiency.
-
Advantages of Dry Grinding:
- No Liquid Handling: Dry grinding eliminates the need for handling and disposing of liquids, simplifying the process.
- Energy Efficiency: Dry grinding can be more energy-efficient for certain materials, as it does not require the additional energy needed to evaporate or separate liquids.
- Dry Final Product: If the end product must be dry, dry grinding avoids the need for additional drying steps.
-
Factors Influencing the Choice Between Dry and Wet Grinding:
- Material Properties: Some materials, like certain ores or ceramics, are more effectively ground in the presence of water, while others, like cement clinker, are typically ground dry.
- Desired Particle Size: Wet grinding is often preferred when very fine particles are required.
- Environmental and Safety Considerations: Wet grinding is chosen when dust control is critical, while dry grinding may be preferred in environments where liquid handling is impractical.
- End-Use Requirements: The final application of the ground material (e.g., dry powder vs. slurry) dictates whether water is needed.
-
Applications of Wet and Dry Grinding:
- Wet Grinding Applications: Commonly used in the mining industry for ore processing, in the ceramics industry for preparing clay slurries, and in the chemical industry for producing fine chemical powders.
- Dry Grinding Applications: Often used in the cement industry for grinding clinker, in the production of dry powders for pharmaceuticals, and in the manufacture of dry pigments.
-
Operational Considerations:
- Mill Design: Ball mills designed for wet grinding may have different liners and discharge mechanisms compared to those used for dry grinding.
- Maintenance: Wet grinding mills may require more maintenance due to the corrosive nature of water and the potential for slurry buildup.
- Cost: The cost of water, its treatment, and disposal can add to the operational expenses of wet grinding, while dry grinding may have lower associated costs in terms of liquid handling.
In conclusion, whether a ball mill needs water depends on the specific requirements of the grinding process and the material being processed. Wet grinding offers advantages in terms of finer particle size and dust control, while dry grinding is preferred for energy efficiency and when a dry final product is needed. The choice between the two methods should be based on material properties, desired outcomes, and operational considerations.
Summary Table:
Aspect | Dry Grinding | Wet Grinding |
---|---|---|
Water Usage | No water added | Water or liquid added to form slurry |
Particle Size | Coarser particles | Finer particles |
Dust Control | Dust generation | Minimal dust |
Energy Efficiency | More energy-efficient for certain materials | Requires energy for liquid handling |
Applications | Cement, dry powders, pigments | Mining, ceramics, fine chemical powders |
Maintenance | Lower maintenance | Higher maintenance due to water corrosion |
Final Product | Dry powder | Slurry or wet product |
Need help deciding between dry and wet grinding for your ball mill? Contact our experts today for personalized advice!