Magnets play a crucial role in enhancing the sputtering rate and improving thin film quality in magnetron sputtering. By creating a magnetic field parallel to the target surface, secondary electrons are trapped near the target, increasing the ionization of argon atoms and forming a dense plasma at lower pressures. This results in higher sputtering and deposition rates, reduced contamination, and improved film quality. The magnetic field also increases the energy of incident particles on the substrate, leading to better adhesion and denser films. Overall, the use of magnets makes the process more efficient and effective for thin film deposition.
Key Points Explained:
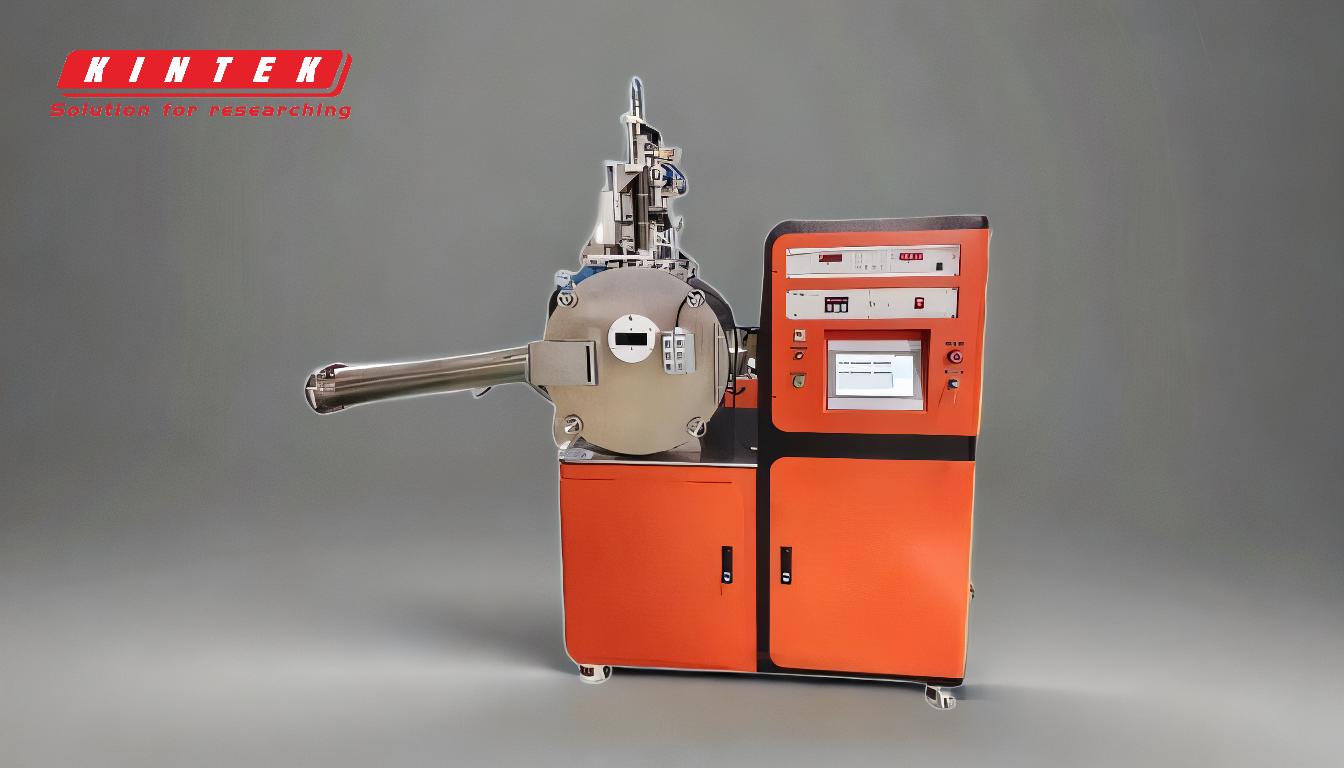
-
Trapping Secondary Electrons:
- Magnets create a magnetic field parallel to the target surface, which traps secondary electrons near the target.
- These trapped electrons follow helical paths around the magnetic field lines, increasing the probability of collisions with neutral gas atoms.
- This enhances the ionization of the gas, leading to a denser plasma near the target.
-
Increased Ionization Efficiency:
- The increased number of collisions between electrons and gas atoms results in higher ionization efficiency.
- More ionized argon atoms are available to bombard the target, increasing the sputtering rate.
- Ionized target material is more likely to interact with other particles and settle on the substrate, improving deposition efficiency.
-
Lower Pressure Operation:
- The magnetic field allows the sputtering process to occur at significantly lower pressures (from 1 Pa to 10^-1 Pa).
- Lower pressure reduces the presence of contaminants in the chamber, leading to cleaner films.
- It also increases the mean free path of sputtered atoms, allowing them to reach the substrate with higher energy.
-
Enhanced Plasma Density:
- The closed magnetic field over the target surface enhances plasma generation.
- Secondary electrons generated by collisions further boost plasma density.
- A denser plasma results in a more rapid sputtering process and higher coating rates.
-
Improved Thin Film Quality:
- The increased energy of incident particles on the substrate leads to better adhesion and denser films.
- Lower contamination levels result in higher purity films.
- The overall efficiency of the process allows for faster growth of high-quality thin films.
-
Higher Sputter Rate:
- The combination of trapped electrons, increased ionization, and denser plasma leads to a higher sputter rate.
- More target material is ejected and deposited on the substrate in a shorter time.
- This makes the process more efficient and cost-effective for industrial applications.
By understanding these key points, it becomes clear how magnets significantly enhance the magnetron sputtering process, leading to improved thin film quality and higher deposition rates.
Summary Table:
Key Benefit | Explanation |
---|---|
Trapping Secondary Electrons | Magnets trap electrons near the target, increasing collisions and ionization. |
Increased Ionization Efficiency | Higher ionization boosts sputtering rates and deposition efficiency. |
Lower Pressure Operation | Enables cleaner films and higher energy sputtered atoms at reduced pressures. |
Enhanced Plasma Density | Denser plasma accelerates sputtering and improves coating rates. |
Improved Thin Film Quality | Better adhesion, denser films, and higher purity due to reduced contamination. |
Higher Sputter Rate | Faster deposition of target material, making the process more cost-effective. |
Learn how magnets can optimize your magnetron sputtering process—contact our experts today!