Calculating the ball mill load is essential for optimizing the milling process, ensuring efficient grinding, and maintaining the longevity of the equipment. The ball mill load refers to the total volume of material (including grinding media, ore, and water) inside the mill. It is typically expressed as a percentage of the mill's total volume. The calculation involves understanding the mill's dimensions, the density of the materials, and the volume occupied by the grinding media and ore. Proper load calculation ensures that the mill operates within its optimal capacity, preventing overloading or underloading, which can affect grinding efficiency and equipment wear.
Key Points Explained:
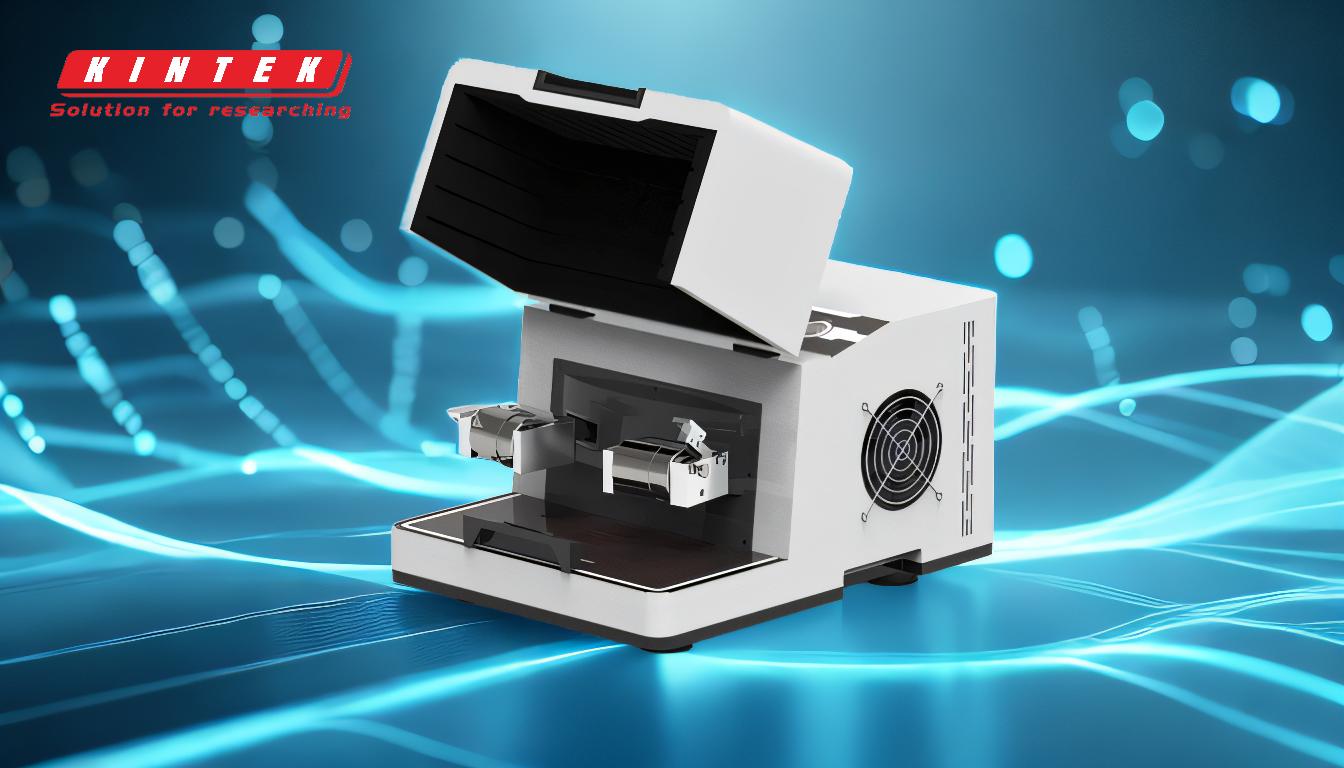
-
Understanding Ball Mill Load:
- The ball mill load is the total volume of material inside the mill, including grinding media (balls), ore, and water.
- It is expressed as a percentage of the mill's total volume.
- Proper load calculation ensures efficient grinding and prevents equipment damage.
-
Components of Ball Mill Load:
- Grinding Media (Balls): The steel or other material balls used for grinding. Their volume and density are critical for load calculation.
- Ore: The material to be ground. Its volume and density affect the total load.
- Water: Often added to the mill to form a slurry, which aids in grinding and material transport.
-
Steps to Calculate Ball Mill Load:
-
Determine Mill Dimensions: Measure the internal diameter and length of the mill to calculate its total volume.
- Formula: ( V_{\text{mill}} = \pi \times r^2 \times L ), where ( r ) is the radius and ( L ) is the length of the mill.
-
Calculate Volume of Grinding Media:
- Determine the total volume occupied by the grinding balls.
- Formula: ( V_{\text{balls}} = \text{Number of Balls} \times \frac{4}{3} \pi r_{\text{ball}}^3 ), where ( r_{\text{ball}} ) is the radius of a single ball.
-
Calculate Volume of Ore and Water:
- Estimate the volume occupied by the ore and water based on their mass and density.
- Formula: ( V_{\text{material}} = \frac{\text{Mass of Material}}{\text{Density of Material}} ).
-
Calculate Total Load:
- Sum the volumes of grinding media, ore, and water.
- Formula: ( \text{Load Percentage} = \frac{V_{\text{total}}}{V_{\text{mill}}} \times 100 ), where ( V_{\text{total}} ) is the sum of all volumes.
-
Determine Mill Dimensions: Measure the internal diameter and length of the mill to calculate its total volume.
-
Factors Affecting Ball Mill Load:
- Mill Speed: Higher speeds can increase the load due to centrifugal force.
- Material Properties: Density and particle size of the ore affect the load.
- Grinding Media Size and Density: Larger or denser balls increase the load.
- Water Content: More water increases the slurry volume, affecting the load.
-
Practical Considerations:
- Optimal Load: Typically, the ball mill load should be around 40-50% of the mill's total volume for efficient grinding.
- Overloading: Excessive load can lead to inefficient grinding, increased power consumption, and equipment wear.
- Underloading: Insufficient load can reduce grinding efficiency and increase energy consumption.
-
Monitoring and Adjustment:
- Regularly monitor the mill load using sensors or manual measurements.
- Adjust the feed rate, grinding media, and water content to maintain the optimal load.
-
Reference to Capacity Calculation:
- The reference mentions calculating mill capacity based on the newly generated powder ore of less than 0.074 mm (-200 mesh).
- This is related to the mill's productivity and can be used in conjunction with load calculations to optimize the grinding process.
By following these steps and considerations, you can accurately calculate the ball mill load and ensure efficient and effective grinding operations.
Summary Table:
Key Component | Description |
---|---|
Grinding Media (Balls) | Volume and density of steel or other material balls used for grinding. |
Ore | Volume and density of the material to be ground. |
Water | Added to form a slurry, aiding in grinding and material transport. |
Optimal Load | Typically 40-50% of the mill's total volume for efficient grinding. |
Overloading Risks | Inefficient grinding, increased power consumption, and equipment wear. |
Underloading Risks | Reduced grinding efficiency and higher energy consumption. |
Need help optimizing your ball mill operations? Contact our experts today!