To remove powder from a ball mill, the process involves stopping the mill, ensuring safety measures are in place, and using appropriate tools and techniques to extract the powder. The powder can be removed manually by scooping or using vacuum systems, or through automated discharge systems if the mill is equipped with them. Proper cleaning and maintenance of the mill after powder removal are essential to prevent contamination and ensure efficient operation. The choice of method depends on the type of ball mill, the nature of the powder, and safety considerations.
Key Points Explained:
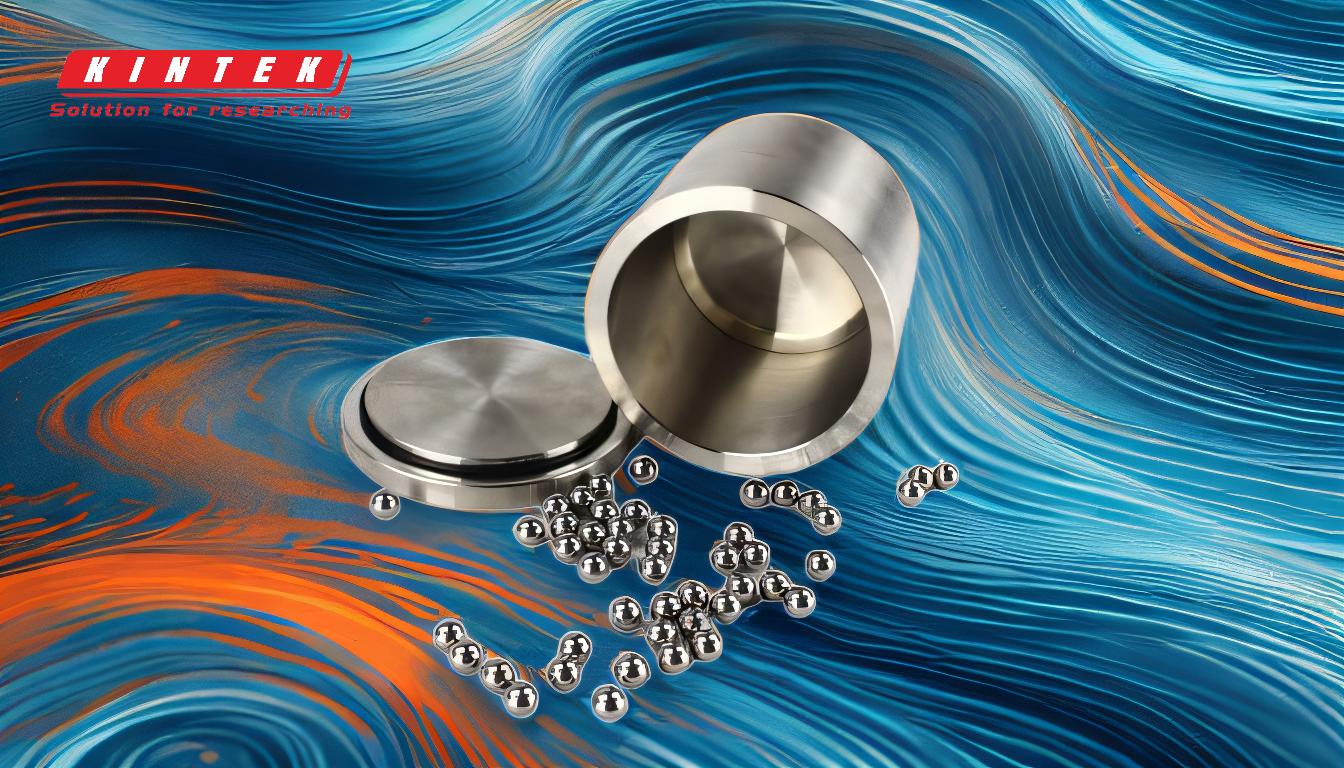
-
Stopping the Ball Mill:
- Before attempting to remove powder, ensure the ball mill is completely stopped and disconnected from any power source. This prevents accidental activation, which could lead to injuries or equipment damage.
- Allow the mill to cool down if it has been running for an extended period, as hot surfaces or materials can pose safety risks.
-
Safety Precautions:
- Wear appropriate personal protective equipment (PPE), such as gloves, safety goggles, and a dust mask, to protect against inhalation of fine particles and contact with potentially hazardous materials.
- Ensure proper ventilation in the workspace to minimize dust accumulation, which can be a fire or health hazard.
-
Manual Powder Removal:
- Scooping: For smaller ball mills or when dealing with non-hazardous powders, manually scoop out the powder using a clean, non-reactive tool like a plastic or stainless steel scoop. This method is simple but may not be efficient for large quantities.
- Vacuum Systems: Use an industrial vacuum cleaner equipped with a HEPA filter to safely collect the powder. This method is more efficient and reduces the risk of dust dispersion in the workspace.
-
Automated Discharge Systems:
- Some ball mills are equipped with built-in discharge mechanisms, such as screw conveyors or pneumatic systems, which allow for the automated removal of powder. These systems are ideal for large-scale operations and minimize manual handling.
- Ensure the discharge system is compatible with the type of powder being processed to avoid blockages or contamination.
-
Cleaning and Maintenance:
- After removing the powder, clean the interior of the ball mill thoroughly to prevent cross-contamination in subsequent batches. Use appropriate cleaning agents and tools, depending on the material of the mill and the nature of the powder.
- Inspect the mill for any signs of wear or damage, such as cracks or worn-out grinding media, and address these issues promptly to maintain optimal performance.
-
Considerations for Specific Powders:
- Hazardous Powders: If the powder is toxic, flammable, or reactive, follow specialized handling procedures, such as using explosion-proof equipment or working in a fume hood.
- Moisture-Sensitive Powders: For powders that are sensitive to moisture, ensure the removal process is conducted in a dry environment or under inert gas to prevent degradation.
-
Environmental and Regulatory Compliance:
- Dispose of the removed powder in accordance with local regulations and environmental guidelines. This may involve recycling, neutralization, or safe disposal at a licensed facility.
- Maintain records of powder removal and disposal processes to ensure compliance with safety and environmental standards.
By following these steps, you can safely and efficiently remove powder from a ball mill while minimizing risks and ensuring the longevity of the equipment.
Summary Table:
Step | Key Actions |
---|---|
Stopping the Ball Mill | Stop and disconnect the mill; allow it to cool. |
Safety Precautions | Wear PPE, ensure proper ventilation. |
Manual Removal | Scoop with non-reactive tools or use a HEPA vacuum. |
Automated Discharge | Use built-in systems like screw conveyors or pneumatic systems. |
Cleaning & Maintenance | Clean thoroughly; inspect for wear or damage. |
Special Powders | Follow specific handling procedures for hazardous or moisture-sensitive powders. |
Compliance | Dispose of powder according to regulations; maintain records. |
Need help with your ball mill powder removal process? Contact our experts today for tailored solutions!