A ball mill machine operates by utilizing the principles of impact, attrition, and friction to grind materials into fine particles. It consists of a horizontally-mounted rotating cylinder filled with grinding media, such as steel balls or rods. As the cylinder rotates, the grinding media are lifted and then cascade down, impacting and grinding the material inside. The larger balls break down coarse materials, while smaller balls fill the voids to produce finer particles. The process is continuous, with the material being fed into one end and the ground product exiting through the other. This method is widely used in industries for grinding ores, chemicals, and other materials.
Key Points Explained:
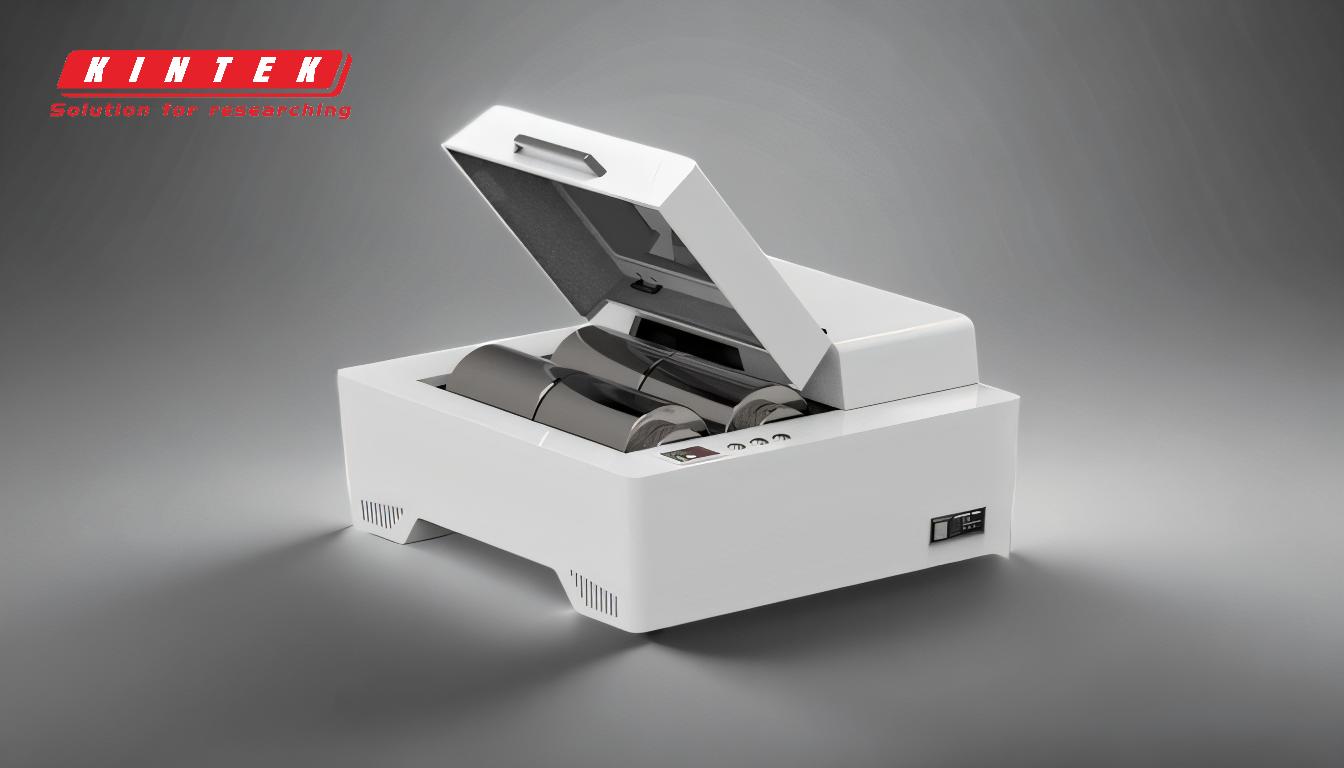
-
Principle of Operation:
- Impact: The grinding balls inside the cylinder collide with the material, exerting pressure and breaking it down into smaller particles.
- Attrition: The repeated collisions and rubbing actions between the grinding balls and the material further reduce the particle size.
- Friction: The movement of the grinding balls against each other and the cylinder walls generates heat and additional grinding action.
-
Components of a Ball Mill:
- Cylinder: A horizontally-mounted rotating cylinder that contains the grinding media and the material to be ground.
- Grinding Media: Typically steel balls or rods, which are responsible for the grinding action.
- Drive Mechanism: A motor and gear system that rotates the cylinder.
- Feed and Discharge: Openings at either end of the cylinder for introducing the material and removing the ground product.
-
Grinding Process:
- Loading: The material to be ground is loaded into the cylinder along with the grinding media.
- Rotation: The cylinder is rotated, causing the grinding media to be lifted and then cascade down.
- Grinding Action: The grinding media impact and grind the material as they fall, reducing it to the desired particle size.
- Discharge: The ground material exits the cylinder through the discharge opening.
-
Types of Ball Mills:
- Tumbling Ball Mill: The most common type, where the cylinder rotates along a horizontal axis.
- Pebble Mill: Uses pebbles as grinding media instead of steel balls.
- Vibratory Ball Mill: Uses vibrations to enhance the grinding action.
-
Applications:
- Mining: Used to grind ores for mineral extraction.
- Chemical Industry: For grinding chemicals and pigments.
- Pharmaceuticals: To reduce the size of active pharmaceutical ingredients.
- Ceramics: For grinding raw materials used in ceramic production.
-
Advantages:
- Versatility: Can grind a wide variety of materials.
- Efficiency: Capable of producing very fine particles.
- Scalability: Available in a range of sizes to suit different production needs.
-
Limitations:
- Energy Consumption: High energy requirements due to the need to rotate the heavy cylinder.
- Wear and Tear: The grinding media and cylinder lining are subject to wear and need regular replacement.
- Noise: The operation can be noisy due to the impact of the grinding media.
By understanding these key points, a purchaser can make an informed decision about the suitability of a ball mill for their specific grinding needs, considering factors such as material type, desired particle size, and production capacity.
Summary Table:
Aspect | Details |
---|---|
Principle | Impact, attrition, and friction for grinding. |
Components | Cylinder, grinding media (steel balls/rods), drive mechanism, feed/discharge. |
Process | Loading, rotation, grinding action, discharge. |
Types | Tumbling, pebble, vibratory ball mills. |
Applications | Mining, chemicals, pharmaceuticals, ceramics. |
Advantages | Versatility, efficiency, scalability. |
Limitations | High energy use, wear and tear, noise. |
Discover the right ball mill for your needs—contact our experts today!