A ball mill reduces particle size through a combination of mechanical forces, including impact, extrusion, and friction, exerted by grinding balls within a rotating cylinder. The process begins by loading materials and grinding balls into the cylinder, which is then rotated at a controlled speed. As the cylinder rotates, the balls collide with the material, breaking it into smaller particles. The repeated collisions and grinding actions lead to the flattening, welding, and deformation of particles, ultimately achieving the desired particle size. The process is highly efficient for producing fine and ultrafine particles, making ball mills essential in industries like mining, ceramics, and pharmaceuticals.
Key Points Explained:
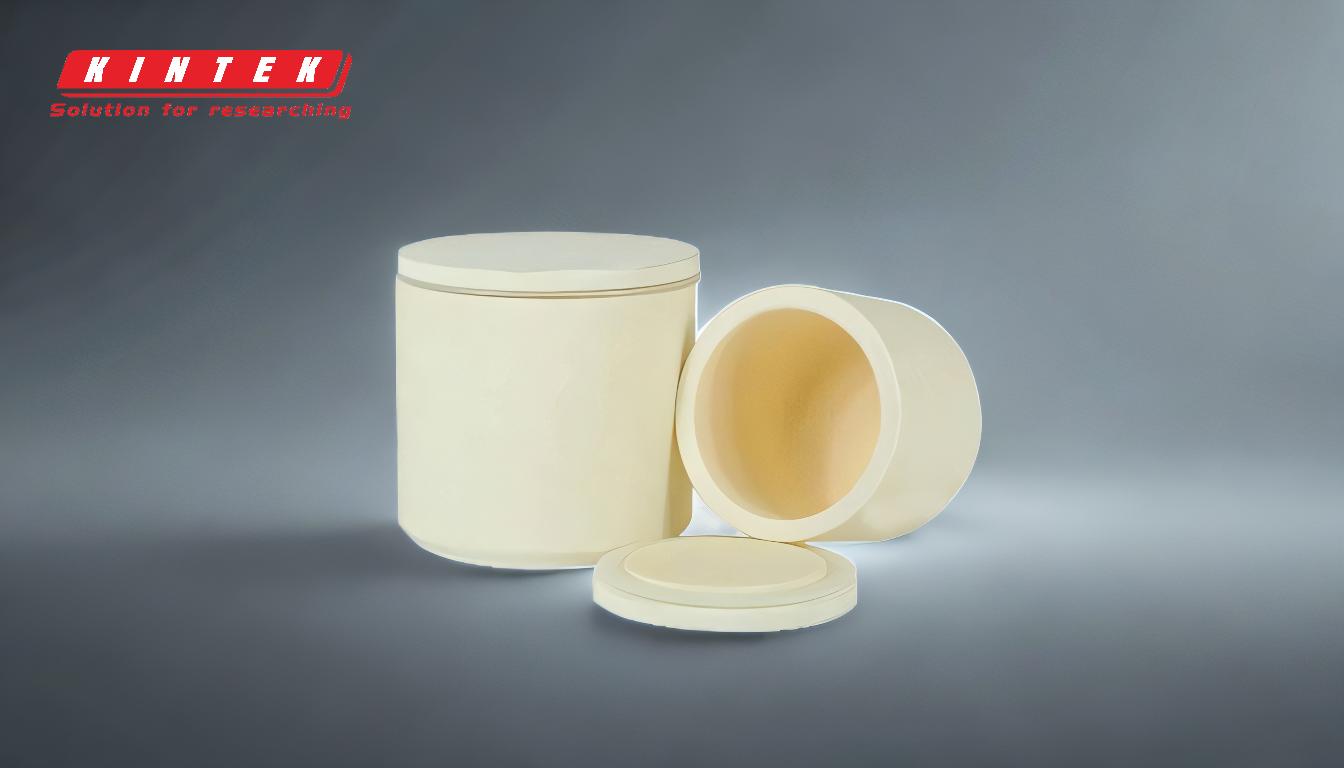
-
Mechanism of Particle Size Reduction:
- Impact: The grinding balls collide with the material, delivering kinetic energy that breaks larger particles into smaller ones.
- Extrusion: Particles are crushed between the grinding balls and the walls of the cylinder, further reducing their size.
- Friction: The rolling and sliding motion of the balls against the material and each other generates frictional forces that grind the particles into finer sizes.
-
Components and Operation:
- Cylinder: The rotating cylinder houses the grinding balls and the material to be processed.
- Grinding Balls: These are typically made of steel, ceramic, or other hard materials and come in various sizes to optimize grinding efficiency.
- Rotation Speed: The speed of the cylinder is critical. Too slow, and the balls won't generate enough force; too fast, and centrifugal force may prevent grinding.
- Loading and Unloading: Materials and balls are loaded into the cylinder, and the machine is operated until the desired particle size is achieved. The processed material is then removed.
-
Stages of Particle Size Reduction:
- Flattening: Initial collisions flatten larger particles, increasing their surface area.
- Welding: Under high pressure, particles may weld together temporarily before breaking apart.
- Layered Structures: Repeated impacts create layered structures within the particles.
- Deformation: These layers deform and fracture, leading to further size reduction.
- Nanoparticle Formation: Prolonged grinding can produce nanoparticles, which are extremely fine particles.
-
Role of Ball Size:
- Large Balls: Effective for breaking down coarse materials due to their higher kinetic energy.
- Small Balls: Fill void spaces and are better suited for fine grinding, producing uniform particle sizes.
-
Applications and Efficiency:
- Ball mills are widely used in industries requiring fine and ultrafine particle sizes, such as mining (for ore grinding), ceramics (for powder preparation), and pharmaceuticals (for drug formulation).
- The process is highly efficient due to the continuous mechanical action, which ensures consistent particle size reduction.
-
Factors Affecting Grinding Efficiency:
- Ball-to-Material Ratio: The proportion of grinding balls to material affects the grinding efficiency.
- Cylinder Speed: Optimal speed ensures effective grinding without excessive wear or energy consumption.
- Material Properties: Hardness, brittleness, and moisture content of the material influence the grinding process.
By understanding these key points, equipment and consumable purchasers can make informed decisions about selecting the right ball mill and grinding parameters for their specific needs.
Summary Table:
Aspect | Details |
---|---|
Mechanism | Impact, extrusion, and friction reduce particle size. |
Key Components | Rotating cylinder, grinding balls, controlled speed. |
Stages of Reduction | Flattening, welding, deformation, nanoparticle formation. |
Ball Size Role | Large balls for coarse grinding, small balls for fine grinding. |
Applications | Mining, ceramics, pharmaceuticals. |
Efficiency Factors | Ball-to-material ratio, cylinder speed, material properties. |
Need a ball mill for your industry? Contact us today to find the perfect solution!