Chemical Vapor Deposition (CVD) is a sophisticated process used to deposit thin films of materials onto a substrate through chemical reactions in a controlled environment. The process involves introducing gaseous precursors into a reaction chamber, activating them through heat, plasma, or other energy sources, and allowing them to react on the substrate surface to form the desired coating. The process is broken down into several key steps, including reactant introduction, activation, surface reaction, and byproduct removal. CVD systems are composed of various components such as reaction chambers, gas delivery systems, heating systems, and vacuum systems, all working together to ensure precise and high-quality deposition. The process is influenced by factors like temperature, pressure, and the type of energy source used, making it highly versatile for various industrial applications.
Key Points Explained:
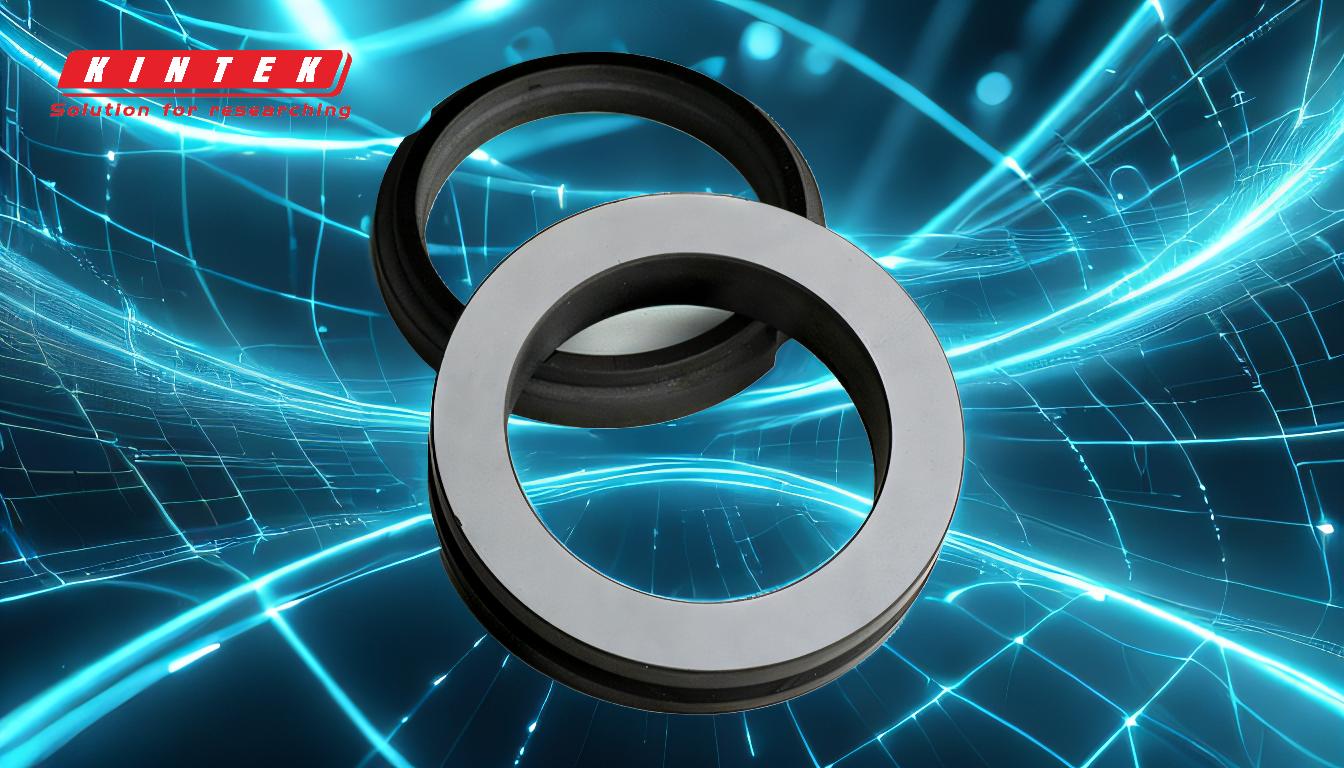
-
Introduction of Reactants:
- Process: Gaseous or liquid precursors containing the elements of the desired film are introduced into the reaction chamber.
- Details: These precursors are typically volatile compounds that can easily vaporize and mix with other gases in the chamber. The introduction is controlled by mass flow controllers to ensure precise metering of the gases.
- Importance: Accurate control of reactant introduction is crucial for achieving uniform film deposition and desired material properties.
-
Activation of Reactants:
- Process: The precursors are activated using thermal energy, plasma, or catalysts to initiate the chemical reactions.
- Details: Activation can occur through various methods, such as heating the chamber to a specific temperature, using plasma to ionize the gases, or introducing catalysts to lower the activation energy required for the reaction.
- Importance: Proper activation ensures that the precursors are in the correct reactive state to form the desired material on the substrate surface.
-
Surface Reaction and Deposition:
- Process: The activated precursors react at the substrate surface to form the desired material, which then deposits as a thin film.
- Details: The reaction involves the breakdown of precursor molecules and the formation of new chemical bonds on the substrate surface. The deposition process is influenced by factors such as surface kinetics, diffusion, and desorption.
- Importance: The quality and uniformity of the deposited film depend on the efficiency of the surface reaction and the control of deposition parameters.
-
Removal of Byproducts:
- Process: Volatile or non-volatile byproducts generated during the reaction are removed from the reaction chamber.
- Details: Byproducts can be gases or solid residues that need to be evacuated to maintain the purity of the deposition environment. This is typically achieved using a vacuum-pumping system and a scrubbing system to clean the exhaust gases.
- Importance: Effective removal of byproducts prevents contamination and ensures the integrity of the deposited film.
-
System Components:
- Reaction Chamber: The core component where the deposition process occurs. It is designed to withstand high temperatures and pressures.
- Gas Delivery System: Includes sources of precursor gases, feed lines, and mass flow controllers to deliver precise amounts of gases into the chamber.
- Heating System: Provides the necessary thermal energy to activate the precursors and maintain the reaction temperature.
- Vacuum System: Maintains the low-pressure environment required for the CVD process, ensuring efficient gas flow and byproduct removal.
- Control System: Monitors and regulates various parameters such as temperature, pressure, and gas flow to ensure consistent and high-quality deposition.
- Exhaust System: Removes byproducts and excess gases from the reaction chamber, often including a scrubbing system to clean the exhaust before release.
-
Influencing Factors:
- Temperature: High temperatures are typically required to activate the precursors and drive the chemical reactions. The exact temperature depends on the specific materials and precursors used.
- Pressure: Low pressures are often used to enhance gas diffusion and reduce unwanted side reactions. The pressure is controlled by the vacuum system.
- Energy Source: The type of energy source (thermal, plasma, etc.) affects the activation and reaction kinetics, influencing the quality and properties of the deposited film.
- Substrate Preparation: The condition of the substrate surface, including cleanliness and temperature, plays a critical role in the adhesion and uniformity of the deposited film.
-
Applications and Versatility:
- Versatility: CVD is used in various industries, including semiconductor manufacturing, optics, and protective coatings, due to its ability to deposit a wide range of materials with high precision.
- Customization: The process can be tailored to specific requirements by adjusting parameters such as temperature, pressure, and precursor composition, making it suitable for diverse applications.
In summary, the CVD process is a highly controlled and versatile method for depositing thin films with precise properties. It involves a series of well-defined steps and relies on a complex system of components to achieve high-quality results. Understanding the key steps and factors influencing the process is essential for optimizing CVD for specific applications.
Summary Table:
Key Aspect | Details |
---|---|
Reactant Introduction | Precursors are introduced into the reaction chamber with precise control. |
Activation | Precursors are activated via heat, plasma, or catalysts for reactions. |
Surface Reaction | Activated precursors form a thin film on the substrate surface. |
Byproduct Removal | Byproducts are removed to maintain deposition purity. |
System Components | Includes reaction chamber, gas delivery, heating, vacuum, and control systems. |
Influencing Factors | Temperature, pressure, energy source, and substrate preparation. |
Applications | Used in semiconductors, optics, and protective coatings. |
Ready to optimize your thin film deposition process? Contact our experts today for tailored CVD solutions!