A pyrolysis reactor is heated using various methods depending on its design and application. The primary heat sources are external, such as furnaces or burners, which supply heat to the reactor. The reactor itself is often a closed system that operates based on thermodynamic principles, ensuring efficient heat transfer to the material being processed. Different reactor types, such as auger, drum, fluidized bed, and Heinz retort reactors, utilize unique mechanisms to distribute heat evenly and achieve the desired pyrolysis conditions. These reactors are constructed from durable materials like Q245R, Q345R boiler plates, or stainless steel to withstand high temperatures and corrosive environments. The heating process is critical for converting feedstock into valuable byproducts like syngas, biochar, and oils.
Key Points Explained:
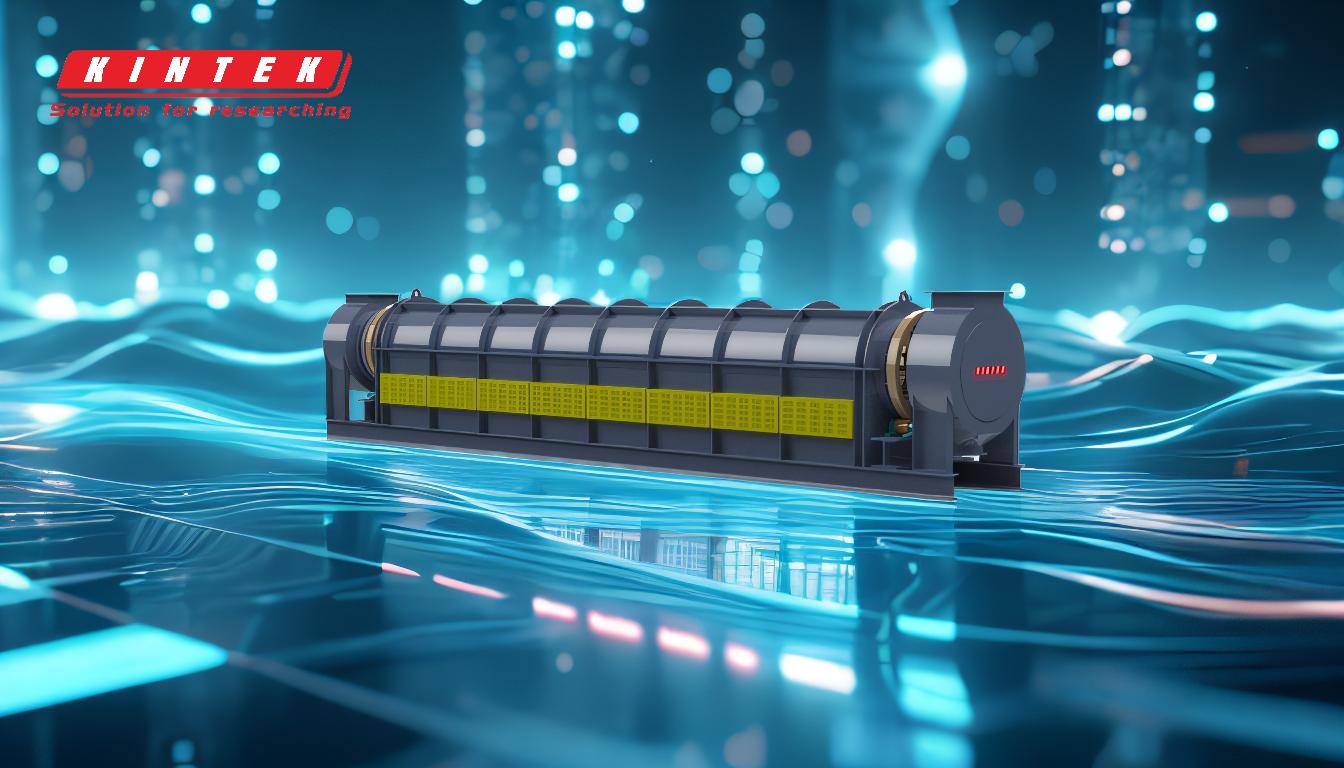
-
External Heat Supply:
- A pyrolysis reactor typically relies on an external heat source, such as a furnace or burner, to provide the necessary thermal energy for pyrolysis. This heat is transferred to the reactor through conduction, convection, or radiation, depending on the reactor design.
- For example, a drum pyrolysis reactor is housed in a furnace that supplies heat to the rotating drum, ensuring uniform heating of the biomass inside.
-
Closed System Operation:
- Pyrolysis reactors operate as closed systems to maintain controlled conditions and prevent the entry of oxygen, which could interfere with the pyrolysis process. This is achieved using inert gases like nitrogen during feeding and processing.
- The closed system ensures that the feedstock undergoes thermal decomposition without combustion, yielding valuable byproducts like syngas and biochar.
-
Reactor Types and Heating Mechanisms:
- Auger Reactor: Uses a screw mechanism driven by a variable-speed motor to move the feedstock through the hot zone. Heat is transferred through mechanical force and pressure, making it suitable for continuous processing.
- Drum Reactor: Features a rotating drum that circulates heat internally. The drum is housed in a furnace, which provides the necessary heat for slow pyrolysis, ideal for biomass processing.
- Fluidized Bed Reactor: Suspends the feedstock in a gas or liquid medium, ensuring even heating and faster pyrolysis. This design is highly efficient for large-scale operations.
- Heinz Retort Reactor: An airtight vessel that receives heat from an external source. Heat is transferred through the vessel walls, causing thermal decomposition of the feedstock. This design is simple and effective for small-scale applications.
-
Construction Materials:
- Pyrolysis reactors are constructed from durable materials like Q245R and Q345R boiler plates or 304 and 306 stainless steel. These materials are chosen for their ability to withstand high temperatures and corrosive environments, ensuring the reactor's longevity and safety.
-
Heat Transfer and Process Efficiency:
- Efficient heat transfer is crucial for the pyrolysis process. Reactors are designed to maximize heat distribution, ensuring that the feedstock reaches the required temperature for thermal decomposition.
- For instance, in a fluidized bed reactor, the suspended feedstock is evenly heated, accelerating the pyrolysis process and improving yield.
-
Byproducts and Applications:
- The heating process in a pyrolysis reactor converts feedstock into valuable byproducts such as syngas, biochar, and oils. These byproducts can be used for energy production, soil amendment, and other industrial applications.
- For example, syngas produced during pyrolysis can be used to generate heat and electricity, while biochar can be utilized as a soil enhancer.
In summary, the heating of a pyrolysis reactor involves a combination of external heat sources, efficient heat transfer mechanisms, and durable construction materials. The design and operation of the reactor play a critical role in determining the efficiency and yield of the pyrolysis process, making it a versatile technology for converting waste into valuable resources.
Summary Table:
Aspect | Details |
---|---|
Heat Sources | External furnaces or burners supply heat via conduction, convection, or radiation. |
Reactor Types | Auger, drum, fluidized bed, and Heinz retort reactors with unique heating mechanisms. |
Construction Materials | Durable materials like Q245R, Q345R boiler plates, or stainless steel. |
Heat Transfer | Ensures uniform heating for efficient thermal decomposition of feedstock. |
Byproducts | Syngas, biochar, and oils for energy, soil amendment, and industrial uses. |
Learn more about pyrolysis reactor heating methods and their applications—contact our experts today!