Sputtering targets are essential components in thin film deposition processes, widely used in industries such as semiconductors, optics, and electronics. The manufacturing of sputtering targets involves specialized techniques tailored to the material properties and intended applications. Common methods include classical and vacuum hot-pressing, cold-pressing and sintering, and vacuum melting and casting. Advanced manufacturing methods are also employed to achieve fine grain structures and precise shapes. The process begins with raw material preparation, followed by forming, sintering, and finishing steps to ensure high-quality targets. These targets are then used in sputtering processes, where argon plasma bombards the target to release atoms that form thin films on substrates.
Key Points Explained:
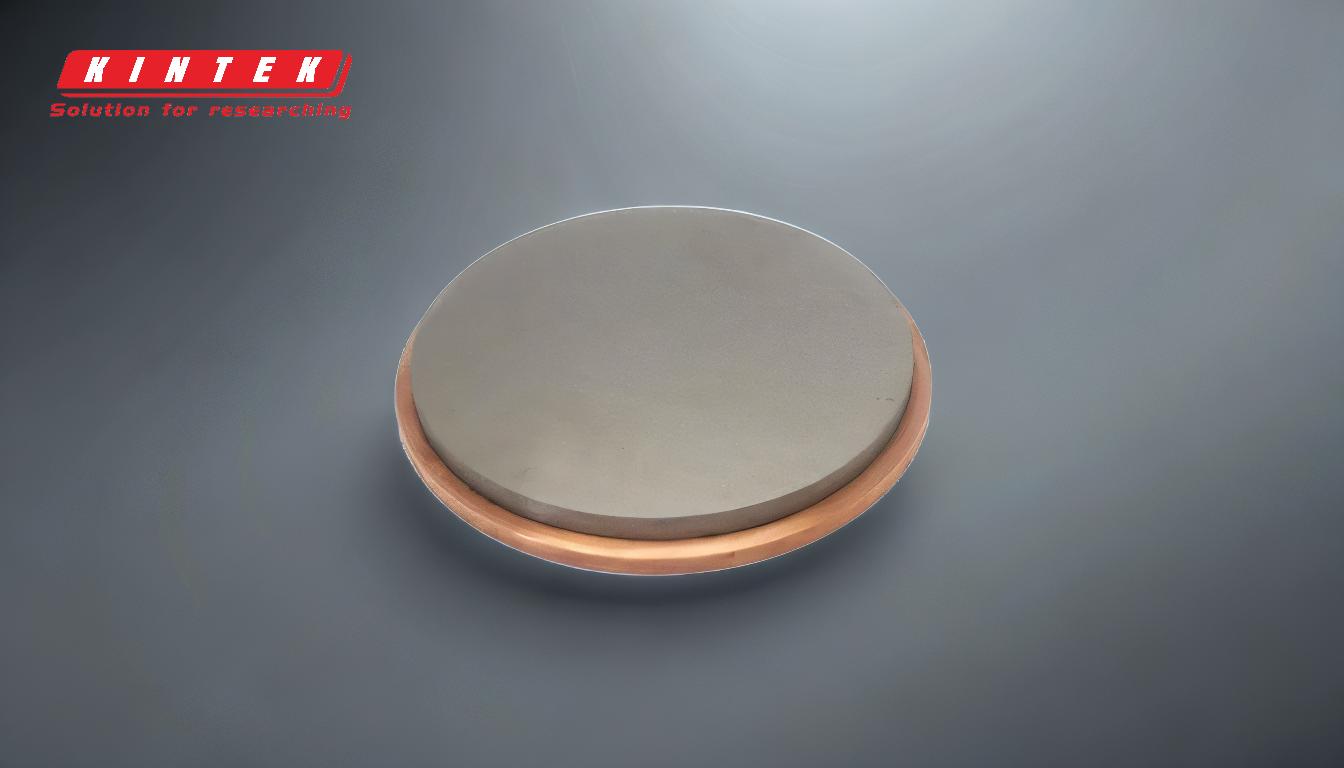
-
Overview of Sputtering Target Manufacturing:
- Sputtering targets are solid slabs made from materials like pure metals, alloys, or compounds (e.g., oxides, nitrides).
- The manufacturing process depends on the material properties and the intended application of the target.
- Common techniques include classical and vacuum hot-pressing, cold-pressing and sintering, and vacuum melting and casting.
-
Raw Material Preparation:
- The process begins with the selection and preparation of raw materials, which can be metals, alloys, or compounds.
- Materials are often purified to ensure high quality and consistency.
- For example, silicon sputtering targets may involve processes like electroplating, sputtering, or vapor deposition to achieve the desired material properties.
-
Forming Techniques:
- Classical and Vacuum Hot-Pressing: This method involves heating the material under pressure to form a dense, uniform target. It is suitable for materials that require high density and fine grain structures.
- Cold-Pressing and Sintering: In this method, the material is pressed into a desired shape at room temperature and then sintered at high temperatures to achieve bonding and densification.
- Vacuum Melting and Casting: This technique involves melting the material in a vacuum to prevent contamination and then casting it into the desired shape. It is ideal for materials that require high purity.
-
Advanced Manufacturing Methods:
- Advanced techniques are used to produce sputtering targets with very fine grain structures, which are critical for achieving high-quality thin films.
- These methods leverage a broad portfolio of materials to create targets in nearly any shape or size, meeting the specific requirements of modern applications.
-
Finishing and Quality Control:
- After forming, the targets undergo finishing processes such as machining, polishing, and cleaning to achieve the desired surface finish and dimensions.
- Quality control measures, including inspection and testing, ensure that the targets meet the required specifications for density, purity, and microstructure.
-
Application in Sputtering Process:
- Once manufactured, sputtering targets are used in sputtering processes, where argon plasma is ignited in a vacuum chamber.
- Argon ions are accelerated towards the negatively charged target, causing atoms to be ejected from the target surface.
- These atoms diffuse through the chamber and condense as a thin film on a substrate, forming the desired coating.
-
Historical Context and Modern Use:
- Sputtering targets were first discovered in 1852 and developed as a thin film deposition technique in 1920.
- Today, they are a critical component in physical vapor deposition (PVD) processes, widely used in modern technology and manufacturing.
By understanding these key points, a purchaser can make informed decisions about the type of sputtering target needed for specific applications, ensuring optimal performance and efficiency in thin film deposition processes.
Summary Table:
Aspect | Details |
---|---|
Raw Material Preparation | Selection and purification of metals, alloys, or compounds. |
Forming Techniques | Hot-pressing, cold-pressing, sintering, vacuum melting, and casting. |
Advanced Methods | Fine grain structures, precise shapes for modern applications. |
Finishing & Quality Control | Machining, polishing, cleaning, and rigorous testing for high-quality targets. |
Applications | Used in semiconductors, optics, and electronics for thin film deposition. |
Need high-quality sputtering targets for your applications? Contact our experts today to learn more!