Hot isostatic pressing (HIP) is a sophisticated manufacturing process used to eliminate porosity and increase the density of materials such as metals, ceramics, polymers, and composites. The process involves applying high temperature and uniform isostatic gas pressure simultaneously to achieve densification. The material, often in powder form, is placed in a sealed container, out-gassed, and subjected to temperatures up to 2000°C and pressures up to 300 MPa using inert gases like argon or nitrogen. The process is controlled by computers to ensure precise temperature, pressure, and time parameters. Mechanisms like plastic deformation, creep, and diffusion contribute to densification, resulting in a defect-free, fully dense material. The process concludes with a controlled cool-down and depressurization phase to safely remove the components.
Key Points Explained:
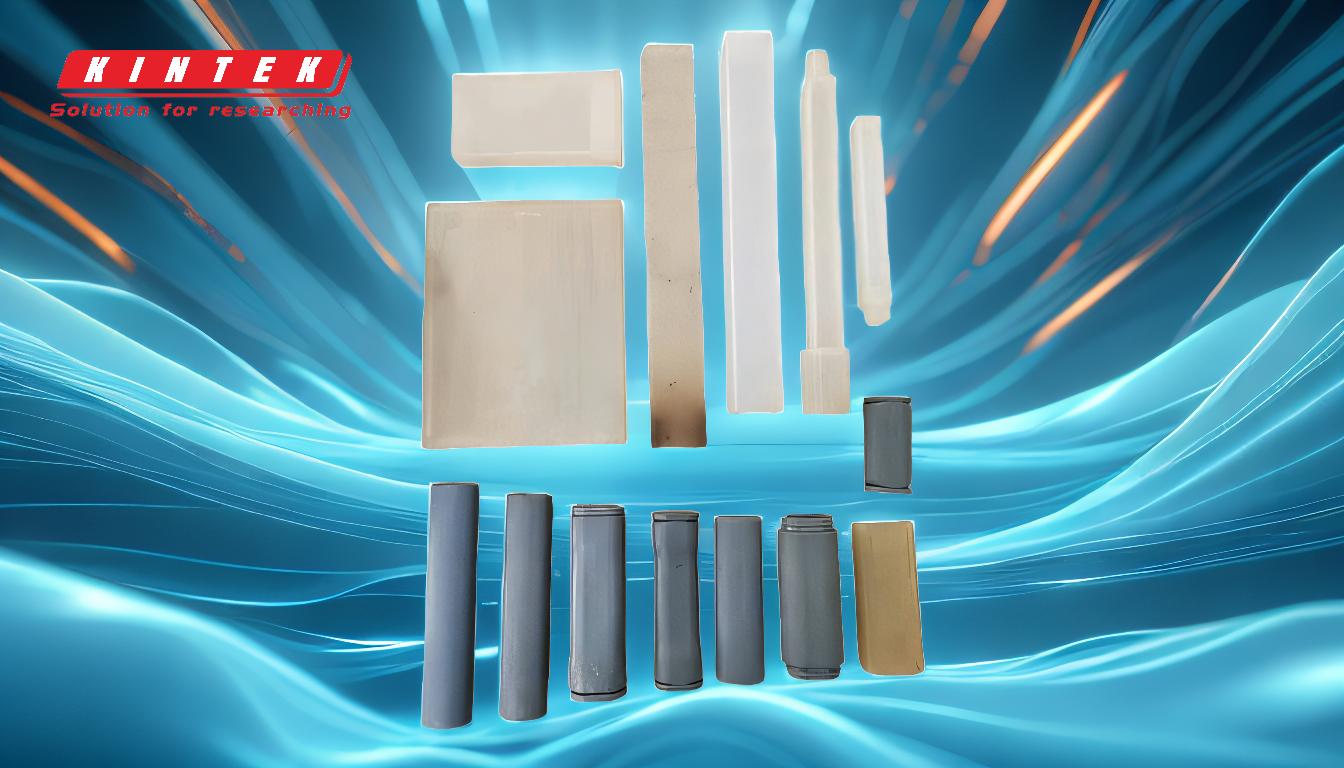
-
Preparation of Material:
- The material, typically in powder form, is placed into a metallic or glass container (called a "can").
- The container is out-gassed to remove any air or impurities and then sealed to create an airtight environment.
-
Loading into the HIP Chamber:
- The sealed container is loaded into a heating chamber within the HIP equipment.
- The chamber can be loaded from the top or bottom, depending on the design of the equipment.
-
Application of Temperature and Pressure:
- The process involves heating the material to temperatures as high as 2000°C.
- Simultaneously, an inert gas (usually argon or nitrogen) is introduced into the chamber to apply isostatic pressure, which can reach up to 300 MPa.
- The pressure is applied uniformly in all directions, ensuring that the material is compressed evenly without altering its shape.
-
Densification Mechanisms:
- Plastic Deformation: At the initial stage, plastic deformation is the dominant mechanism. The high pressure causes voids and pores within the material to collapse.
- Creep and Diffusion: As the process continues, creep and diffusion become more significant. These mechanisms allow the material to flow in the solid state, further eliminating pores and bonding the material at an atomic level.
-
Computer Control and Monitoring:
- The entire process is controlled by computers, which program the equipment to achieve the desired results.
- Parameters such as temperature ramp-up, pressure, and total process time are closely monitored and adjusted as needed to ensure optimal densification.
-
Depressurization and Cool-Down:
- After the desired temperature and pressure have been maintained for the required duration, the process enters the depressurization phase.
- The chamber is gradually cooled down to ensure that the components can be safely removed without any thermal shock or deformation.
-
Final Product:
- The result of the HIP process is a fully dense, defect-free material with improved mechanical properties.
- The material can be used in various applications, including aerospace, medical, and industrial sectors, where high strength and reliability are critical.
-
Applications of HIP:
- HIP is used to densify materials, eliminate porosity, and improve the mechanical properties of metals, ceramics, polymers, and composites.
- It is also used for joining different materials or parts, creating strong, defect-free bonds.
-
Advantages of HIP:
- Uniform Pressure: The isostatic nature of the pressure ensures that the material is compressed evenly, leading to uniform densification.
- Defect Elimination: The process effectively eliminates internal voids, pores, and defects, resulting in materials with superior mechanical properties.
- Versatility: HIP can be applied to a wide range of materials, making it a versatile manufacturing process.
-
Equipment and Process Control:
- HIP equipment comes in various sizes and configurations, allowing for the processing of both small and large components.
- Advanced computer control systems ensure precise control over the process parameters, leading to consistent and high-quality results.
By following these steps and mechanisms, hot isostatic pressing transforms porous materials into dense, high-performance components suitable for demanding applications.
Summary Table:
Key Aspect | Details |
---|---|
Process Overview | Combines high temperature (up to 2000°C) and uniform isostatic pressure (up to 300 MPa) to densify materials. |
Material Preparation | Powdered material is placed in a sealed container, out-gassed, and sealed. |
Densification Mechanisms | Plastic deformation, creep, and diffusion eliminate pores and bond materials at an atomic level. |
Applications | Aerospace, medical, and industrial sectors requiring high strength and reliability. |
Advantages | Uniform pressure, defect elimination, and versatility across materials. |
Ready to enhance your material performance with HIP? Contact our experts today to learn more!