Hot isostatic pressing (HIP) is a manufacturing process that uses high temperature and isostatic gas pressure to eliminate porosity and increase the density of materials such as metals, ceramics, polymers, and composites. The duration of the HIP process varies depending on factors like material type, desired density, and specific application requirements. For example, a dense coating with hydroxyapatite (HAP) structure was achieved in just 35 minutes at temperatures between 700–850°C and a pressure of 1000 bar. However, the total process time also includes phases like temperature ramp-up, pressure application, and cool-down, which can extend the overall duration. The process is highly controlled, with computers managing temperature, pressure, and timing to ensure consistent and reproducible results.
Key Points Explained:
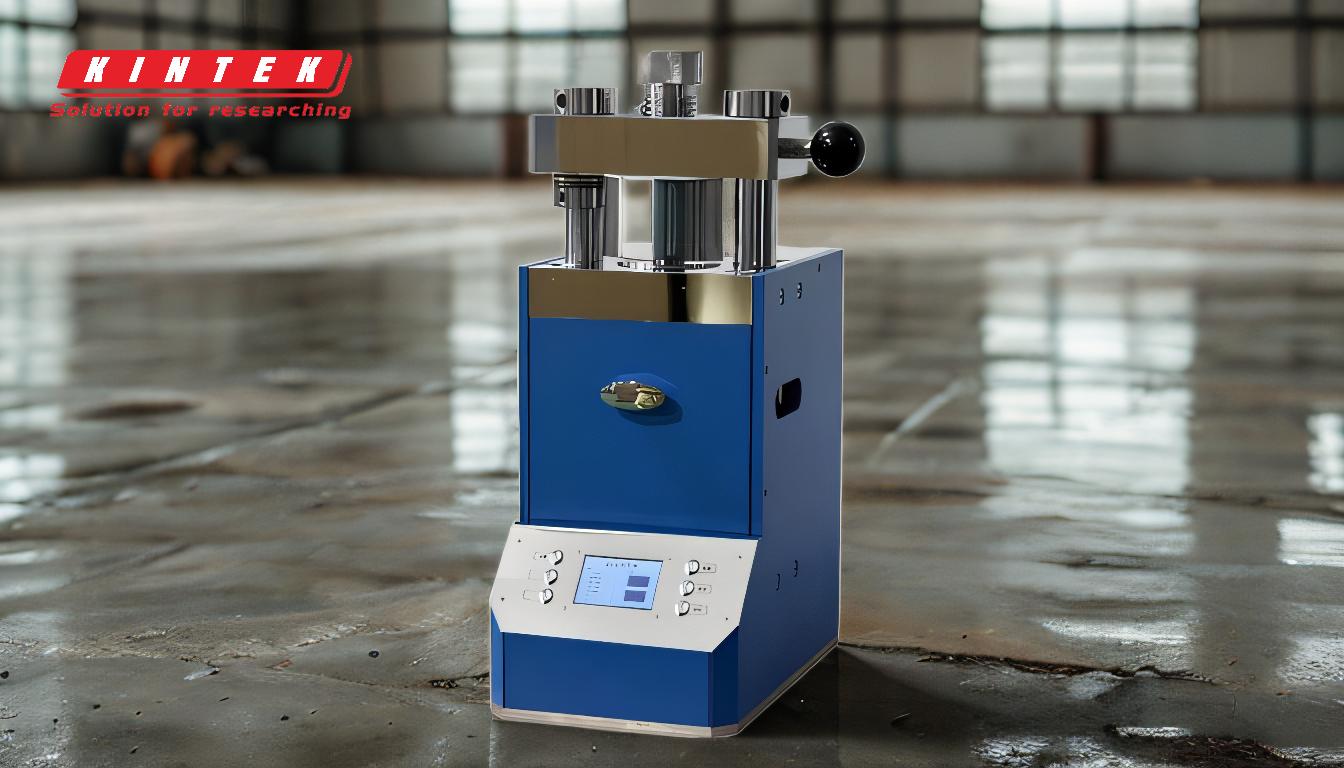
-
Process Overview:
- Hot isostatic pressing involves applying high temperature (1000–2200°C) and isostatic gas pressure (100–200 MPa) uniformly to materials in all directions.
- The process densifies materials by eliminating porosity through mechanisms like plastic deformation, creep, and diffusion.
- It is used for sintering, densifying, or joining materials and improving their mechanical properties.
-
Typical Duration:
- The core HIP process can take as little as 35 minutes for specific applications, such as creating dense coatings with hydroxyapatite (HAP) at 700–850°C and 1000 bar pressure.
- However, the total process time includes additional phases like:
- Temperature ramp-up: Heating the material to the desired temperature.
- Pressure application: Achieving and maintaining the required isostatic pressure.
- Cool-down: Gradually reducing temperature and pressure to safely remove the components.
-
Factors Influencing Process Time:
- Material Type: Different materials (e.g., metals, ceramics, polymers) require varying temperatures, pressures, and durations for densification.
- Desired Density: Higher density goals may necessitate longer processing times.
- Component Size and Complexity: Larger or more complex parts may require extended processing to ensure uniform densification.
- Process Control: Automated systems ensure precise control over temperature, pressure, and timing, which can optimize the process duration.
-
Process Phases:
- Loading: Components are placed into the HIP chamber, which can be loaded from the top or bottom.
- Heating and Pressurization: The chamber is heated to the target temperature, and inert gas (e.g., argon) is used to apply uniform pressure.
- Densification: The material undergoes densification through mechanisms like plastic deformation, creep, and diffusion.
- Depressurization and Cooling: The chamber is gradually depressurized and cooled to ensure the components are safe to handle.
-
Equipment and Automation:
- HIP equipment is computer-controlled, with programmable cycles to achieve consistent results.
- The equipment can handle various sizes and types of components, ensuring uniform pressure application without altering the shape of preformed parts.
-
Applications and Customization:
- HIP is used for refining parts, solving technical problems, and improving material quality and durability.
- The process can be customized to meet specific customer, military, or industry requirements, including traceability and stringent gas purity standards.
In summary, the duration of hot isostatic pressing depends on the material, desired outcome, and process parameters. While the core densification phase can be as short as 35 minutes, the total process time includes additional steps like heating, cooling, and pressure control, which may extend the overall duration. The process is highly controlled and customizable to meet specific application needs.
Summary Table:
Aspect | Details |
---|---|
Core Process Duration | As short as 35 minutes for specific applications (e.g., HAP coatings). |
Total Process Time | Includes ramp-up, pressure application, and cool-down phases. |
Key Influencing Factors | Material type, desired density, component size, and process control. |
Process Phases | Loading, heating, pressurization, densification, depressurization, cooling. |
Applications | Densifying metals, ceramics, polymers, and composites for improved quality. |
Need a customized HIP solution? Contact our experts today to optimize your material processing!