The duration for which a sieve shaker should be run depends on several factors, including the type of material being sieved, the desired level of separation, and the specific standards or protocols being followed. Generally, sieve shakers are run for a period that ensures thorough separation of particles according to their size. This duration can vary based on the material's properties, such as particle size distribution, density, and moisture content. For most standard applications, running the sieve shaker for 10 to 15 minutes is common, but specific protocols or material characteristics may require adjustments to this time frame.
Key Points Explained:
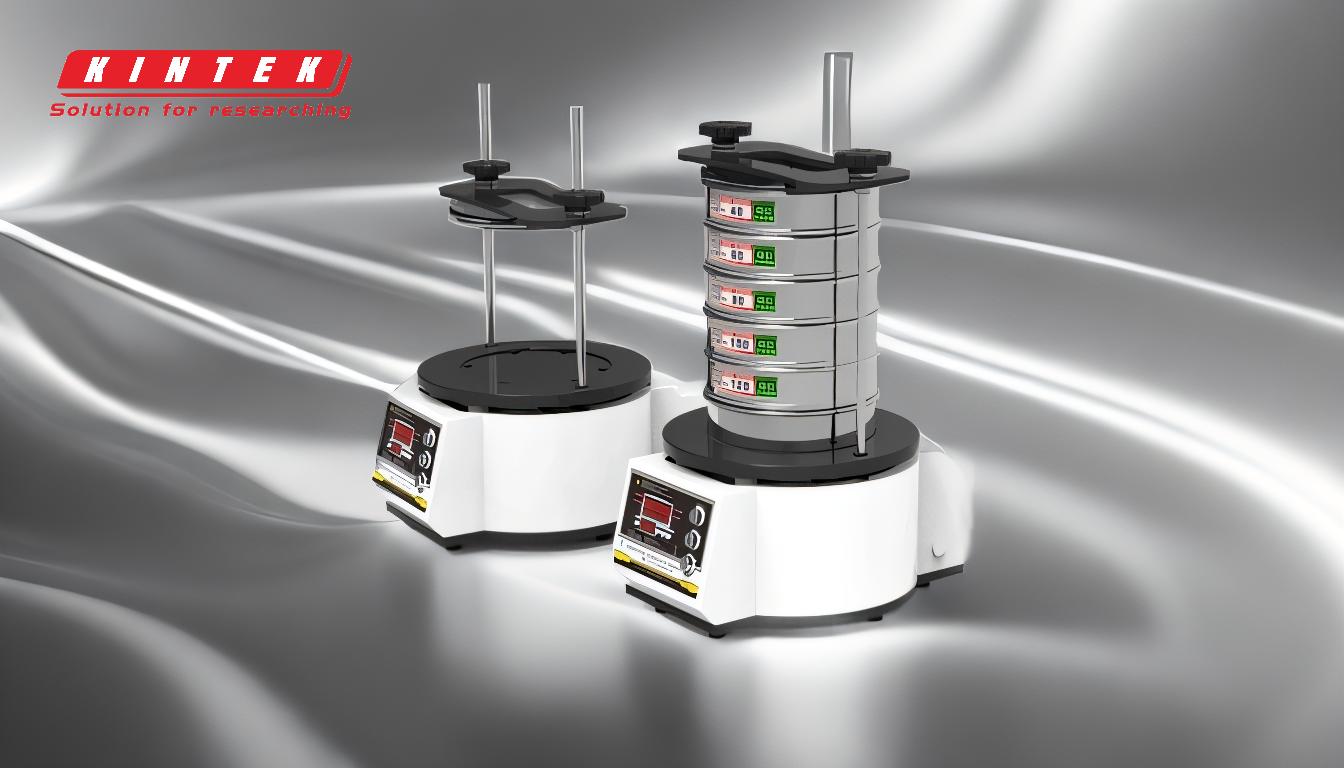
-
Material Characteristics:
- Particle Size Distribution: Materials with a wide range of particle sizes may require longer sieving times to ensure all particles are properly separated.
- Density: Denser materials might need more time to ensure that smaller particles pass through the sieve.
- Moisture Content: Wet or sticky materials can clog sieves, potentially requiring longer sieving times or pre-treatment to dry the material.
-
Sieve Specifications:
- Sieve Frame Diameter: The diameter of the sieve frame (e.g., 200mm, 300mm, 400mm) can influence the sieving time. Larger frames may require more time to ensure uniform sieving across the entire surface.
- Mesh Standards: Compliance with standards like GB6003.1-1997 for wire woven mesh or GB6003.2-1997 for perforated plate screen mesh may dictate specific sieving times to meet regulatory or quality control requirements.
-
Desired Separation Level:
- Precision Requirements: Higher precision in particle separation may necessitate longer sieving times to achieve the desired level of accuracy.
- End-Use Application: The intended use of the sieved material (e.g., pharmaceutical, construction) may influence the required sieving duration to meet application-specific standards.
-
Operational Considerations:
- Sieve Shaker Type: Different types of sieve shakers (e.g., mechanical, electromagnetic) may have varying optimal running times based on their design and efficiency.
- Sample Size: Larger sample sizes may require extended sieving times to ensure complete separation.
-
Standard Protocols:
- Industry Standards: Many industries have standardized protocols that specify sieving times. For example, ASTM or ISO standards may provide guidelines on the duration for specific materials.
- Laboratory Practices: Internal laboratory protocols or quality control procedures may also dictate the sieving time to ensure consistency and reproducibility.
-
Monitoring and Adjustment:
- Visual Inspection: Periodic checks during sieving can help determine if the process is complete or if additional time is needed.
- Weight Measurement: Weighing the material before and after sieving can help assess the effectiveness of the sieving process and determine if the duration is sufficient.
In conclusion, while a general guideline of 10 to 15 minutes is commonly used for sieve shaker operation, the actual duration should be tailored to the specific material, sieve specifications, and desired outcomes. Adhering to industry standards and considering material properties will help determine the optimal sieving time for accurate and efficient particle separation.
Summary Table:
Factor | Influence on Sieving Time |
---|---|
Material Characteristics | Particle size distribution, density, and moisture content affect sieving duration. |
Sieve Specifications | Frame diameter and mesh standards (e.g., GB6003.1-1997) may dictate specific sieving times. |
Desired Separation Level | Higher precision or application-specific standards may require longer sieving times. |
Operational Considerations | Sieve shaker type and sample size impact optimal running times. |
Standard Protocols | ASTM, ISO, or internal lab protocols provide guidelines for sieving duration. |
Monitoring and Adjustment | Visual inspection and weight measurement help determine sufficient sieving time. |
Need help determining the ideal sieving time for your materials? Contact our experts today for tailored solutions!