The cost of manufacturing a mold can vary significantly depending on several factors, including the complexity of the design, the materials used, the type of mold, and the manufacturing process. Generally, simple molds for basic shapes can cost a few hundred dollars, while highly complex molds for intricate designs can run into tens of thousands of dollars or more. Factors such as the type of material (e.g., aluminum, steel), the precision required, and the production volume also play a crucial role in determining the final cost. Additionally, labor costs, tooling expenses, and post-processing requirements like finishing and quality control can further influence the overall expense. Understanding these variables is essential for accurately estimating the cost of mold manufacturing.
Key Points Explained:
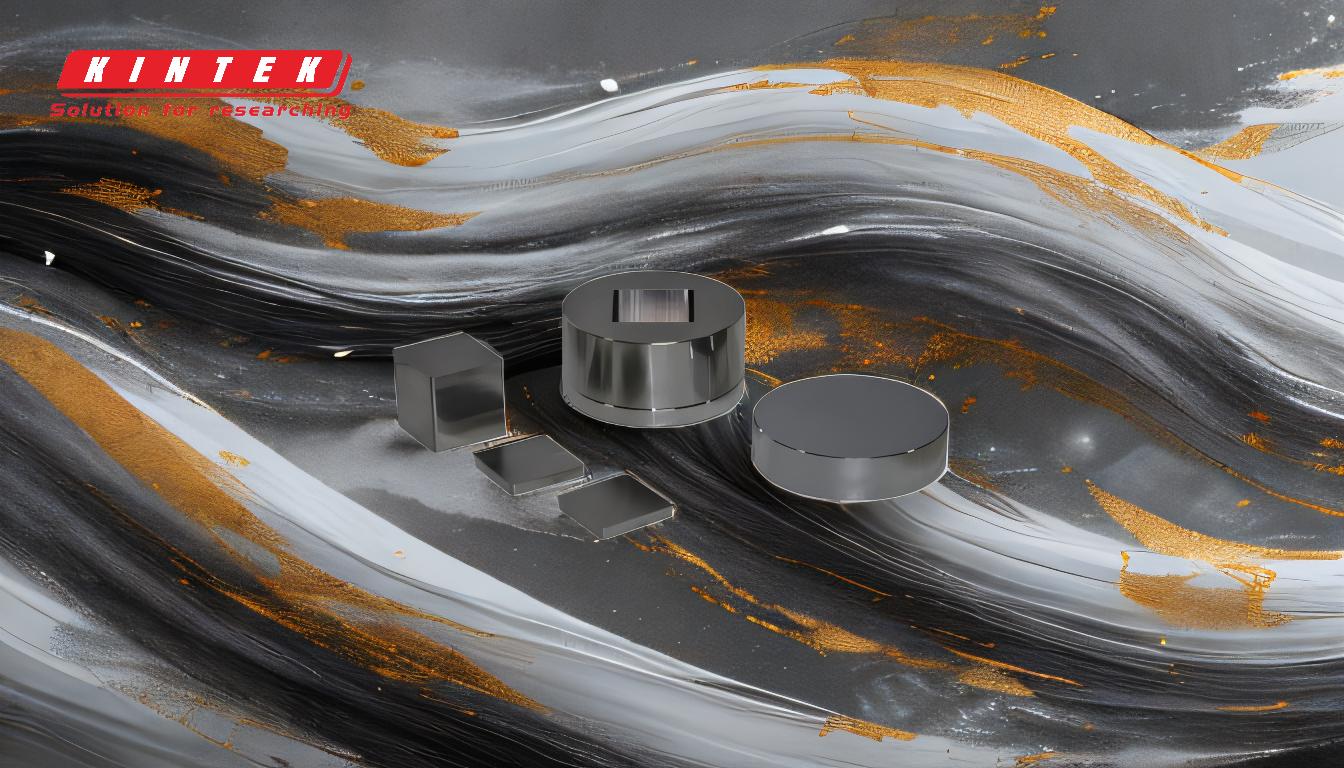
-
Complexity of the Mold Design:
- The more complex the mold design, the higher the cost. Complex designs require more time, precision, and expertise to manufacture. For example, molds with intricate geometries, undercuts, or fine details will necessitate advanced machining techniques and may require multiple stages of production, increasing the overall cost.
-
Material Selection:
- The choice of material significantly impacts the cost. Common materials include aluminum and steel. Aluminum molds are generally less expensive and are suitable for low to medium production runs. Steel molds, on the other hand, are more durable and can withstand higher production volumes but are more costly due to the material's hardness and the additional machining time required.
-
Type of Mold:
- Different types of molds, such as injection molds, blow molds, or compression molds, have varying costs. Injection molds, for instance, are typically more expensive due to the precision required in their design and the high-pressure environment they operate in. Blow molds, used for creating hollow objects like bottles, may be less expensive but still require specialized equipment.
-
Manufacturing Process:
- The manufacturing process itself can influence the cost. Processes like CNC machining, EDM (Electrical Discharge Machining), and 3D printing each have different cost structures. CNC machining is precise but can be expensive due to the time and expertise required. EDM is used for highly detailed work and can add to the cost. 3D printing is becoming more common for prototyping and can reduce costs for certain types of molds.
-
Production Volume:
- The expected production volume plays a role in determining the cost. High-volume production runs may justify the higher initial cost of a more durable material like steel, as the cost per unit decreases with higher volumes. Conversely, low-volume production may benefit from less expensive materials and simpler designs.
-
Labor Costs:
- Skilled labor is required for mold design, machining, and finishing. The cost of labor can vary depending on the region and the expertise of the workforce. Highly skilled machinists and engineers command higher wages, which can increase the overall cost of mold manufacturing.
-
Tooling and Equipment:
- The cost of tooling and equipment needed to produce the mold can be substantial. Specialized machinery, such as CNC machines or EDM equipment, represents a significant investment. Additionally, the maintenance and operation of these machines contribute to the overall cost.
-
Post-Processing and Finishing:
- After the mold is manufactured, it often requires post-processing steps such as polishing, heat treatment, or coating to ensure it meets the required specifications. These additional steps add to the cost but are necessary for achieving the desired quality and durability.
-
Quality Control and Testing:
- Ensuring the mold meets quality standards involves rigorous testing and inspection. This may include dimensional checks, material testing, and trial runs to verify the mold's performance. The cost of quality control measures must be factored into the overall expense.
-
Economies of Scale:
- Larger production runs can benefit from economies of scale, where the cost per unit decreases as the volume increases. This is particularly relevant for high-volume manufacturing, where the initial investment in a high-quality mold can be amortized over a larger number of units.
In summary, the cost of manufacturing a mold is influenced by a multitude of factors, each contributing to the final price. Understanding these variables and how they interact is crucial for anyone involved in the procurement or design of molds, ensuring that the final product meets both quality and budgetary requirements.
Summary Table:
Factor | Impact on Cost |
---|---|
Design Complexity | Higher complexity increases costs due to advanced machining and production stages. |
Material Selection | Aluminum is cheaper; steel is durable but more expensive. |
Type of Mold | Injection molds are costlier; blow molds are less expensive. |
Manufacturing Process | CNC and EDM are precise but costly; 3D printing reduces costs for prototyping. |
Production Volume | High volumes justify higher upfront costs; low volumes benefit from simpler designs. |
Labor Costs | Skilled labor increases costs, especially in high-wage regions. |
Tooling and Equipment | Specialized machinery like CNC and EDM adds to expenses. |
Post-Processing | Polishing, heat treatment, and coating increase costs. |
Quality Control | Rigorous testing and inspection add to overall expenses. |
Economies of Scale | Larger production runs reduce cost per unit. |
Need help estimating your mold manufacturing costs? Contact us today for a personalized quote!