A rotary pump, specifically a rotary vane pump, is a widely used vacuum pump capable of achieving medium to high vacuum levels. The vacuum level it can achieve depends on its design, whether it is single-stage or double-stage, and its operational conditions. Standard rotary vane pumps typically achieve vacuum levels of around 5x10^-2 mbar, which is suitable for many laboratory and industrial applications. These pumps work by trapping gas molecules in chambers created by rotating vanes and expelling them to create a vacuum. While they are not as effective as turbomolecular pumps (which can achieve vacuum levels of 1x10^-5 mbar), rotary vane pumps are reliable, cost-effective, and commonly used for rough to medium vacuum applications.
Key Points Explained:
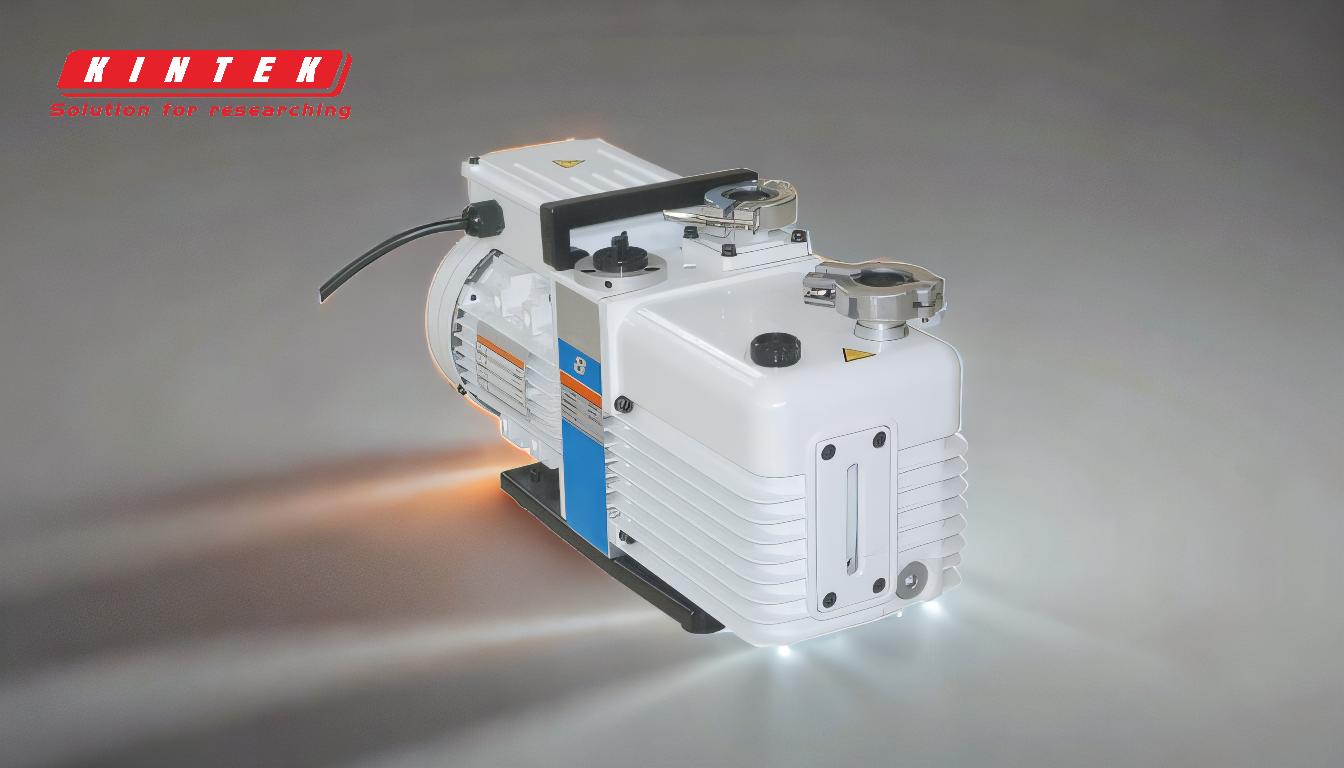
-
Vacuum Levels Achievable by Rotary Pumps
- Rotary vane pumps, the most common type of rotary pump, can achieve vacuum levels of approximately 5x10^-2 mbar.
- This level of vacuum is considered a rough to medium vacuum, suitable for applications like degassing, vacuum drying, and general laboratory use.
- For comparison, turbomolecular pumps, which are more advanced, can achieve much higher vacuum levels of 1x10^-5 mbar, but they are typically used in high-vacuum applications like semiconductor manufacturing or particle physics research.
-
How Rotary Vane Pumps Work
- Rotary vane pumps operate by using a rotor with vanes that rotate inside a chamber. The rotor is eccentrically installed, meaning it is offset from the center of the chamber.
- As the rotor spins, the vanes trap gas molecules in chambers that progressively decrease in size, compressing the gas.
- The compressed gas is then expelled through an exhaust port, creating a low-pressure region (vacuum) in the chamber.
- The vanes are held against the housing by centrifugal force and springs, ensuring a tight seal to prevent gas leakage.
-
Single-Stage vs. Double-Stage Rotary Pumps
- Rotary vane pumps can be single-stage or double-stage.
- Single-stage pumps are simpler and less expensive but achieve lower vacuum levels, typically around 1x10^-1 mbar.
- Double-stage pumps have two compression stages in series, allowing them to achieve deeper vacuum levels of 5x10^-2 mbar.
- Double-stage pumps are more commonly used in applications requiring a higher vacuum.
-
Applications of Rotary Vane Pumps
- Rotary vane pumps are versatile and widely used in various industries.
- Common applications include:
- Laboratory use: For vacuum filtration, degassing, and freeze-drying.
- Industrial use: In vacuum packaging, HVAC systems, and material handling.
- Chemical and pharmaceutical industries: For distillation, evaporation, and solvent recovery.
- Their ability to operate directly from atmospheric pressure makes them highly practical for many tasks.
-
Limitations of Rotary Vane Pumps
- While rotary vane pumps are effective for rough to medium vacuum applications, they have limitations:
- They cannot achieve the ultra-high vacuum levels required for advanced scientific research or semiconductor manufacturing.
- They require regular maintenance, including oil changes, to ensure optimal performance.
- They are less efficient in handling corrosive or particulate-laden gases, which can damage the vanes and housing.
- While rotary vane pumps are effective for rough to medium vacuum applications, they have limitations:
-
Comparison with Other Vacuum Pumps
- Rotary vane pumps are often compared to other types of vacuum pumps, such as turbomolecular pumps and diaphragm pumps.
- Turbomolecular pumps: Achieve much higher vacuum levels (1x10^-5 mbar) but are more expensive and complex.
- Diaphragm pumps: Oil-free and suitable for clean applications but typically achieve lower vacuum levels (1x10^-1 mbar).
- Rotary vane pumps strike a balance between cost, performance, and versatility, making them a popular choice for many applications.
-
Maintenance and Lubrication
- Rotary vane pumps require lubrication to reduce friction and wear between the vanes and housing.
- The vacuum chamber is typically greased with oil, which also helps seal the chambers and improve vacuum performance.
- Regular maintenance, including oil changes and vane inspections, is essential to maintain the pump's efficiency and longevity.
-
Operational Speed and Efficiency
- Rotary vane pumps operate at a rotating speed of approximately 1500 revolutions per minute (RPM).
- This high-speed rotation ensures efficient gas compression and expulsion, contributing to the pump's ability to achieve consistent vacuum levels.
- The small clearances between the rotor and housing, combined with low-friction materials, minimize gas leakage and enhance performance.
By understanding these key points, a purchaser can make an informed decision about whether a rotary vane pump is suitable for their specific vacuum requirements. Its ability to achieve vacuum levels of 5x10^-2 mbar, combined with its reliability and versatility, makes it a valuable tool for a wide range of applications.
Summary Table:
Aspect | Details |
---|---|
Vacuum Level | ~5x10^-2 mbar (double-stage), ~1x10^-1 mbar (single-stage) |
Applications | Degassing, vacuum drying, filtration, HVAC, distillation, solvent recovery |
Maintenance | Regular oil changes and vane inspections required |
Comparison | Less effective than turbomolecular pumps but more cost-effective |
Operational Speed | ~1500 RPM for efficient gas compression and expulsion |
Need a reliable rotary vane pump for your lab or industry? Contact us today for expert advice and solutions!