Improving the efficiency of a ball mill involves optimizing several factors, including feed size, feeding uniformity, liner material, cylinder volume, fill rate, mill speed, and steel ball ratio. These factors directly influence the grinding process, energy consumption, and overall output quality. By controlling feed size and ensuring uniform feeding, the mill can operate more consistently, reducing wear and energy waste. Upgrading liner materials and optimizing cylinder volume enhance durability and grinding capacity. Adjusting fill rate and mill speed ensures optimal grinding conditions, while selecting the right steel ball ratio maximizes grinding efficiency. These strategies collectively improve the ball mill's performance and productivity.
Key Points Explained:
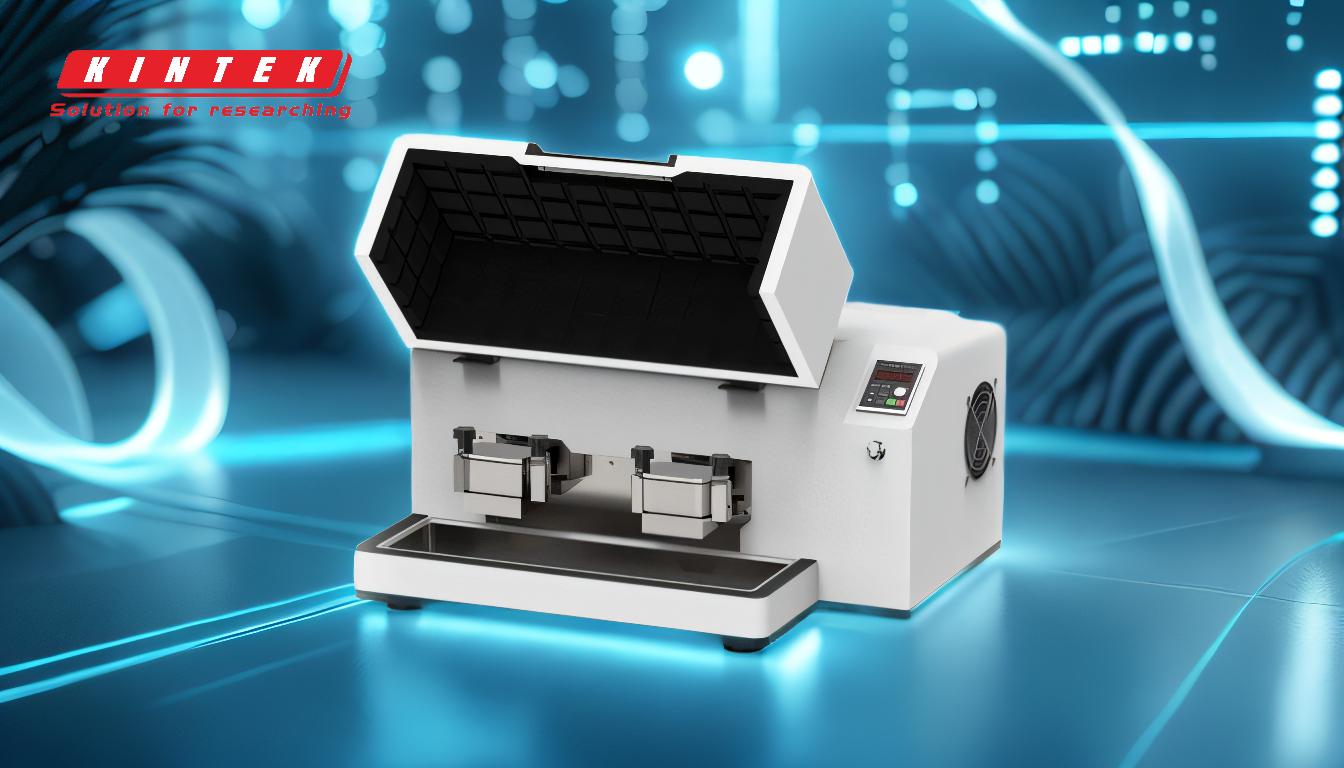
-
Control Feed Size:
- Why it matters: The size of the feed material significantly impacts the grinding efficiency. Larger particles require more energy to break down, leading to inefficiency.
- How to implement: Use crushers or pre-grinding equipment to reduce the feed size before it enters the ball mill. This ensures that the mill processes smaller, more manageable particles, reducing energy consumption and improving throughput.
-
Uniform Feeding:
- Why it matters: Uneven feeding can cause fluctuations in the mill's load, leading to inconsistent grinding and potential damage to the mill.
- How to implement: Use automated feeding systems or vibratory feeders to ensure a steady and consistent flow of material into the mill. This maintains a stable grinding environment and improves overall efficiency.
-
Improve Material of Liner and Effective Volume of Cylinder:
- Why it matters: The liner material and cylinder volume affect the mill's durability, grinding capacity, and energy efficiency.
- How to implement: Use high-quality, wear-resistant materials for the liners to reduce maintenance and downtime. Optimize the cylinder's effective volume by ensuring it is neither overfilled nor underfilled, which can impact grinding efficiency.
-
Control Fill Rate and Mill Speed:
- Why it matters: The fill rate (percentage of the mill volume occupied by grinding media) and mill speed (rotation speed) directly influence the grinding action and energy consumption.
- How to implement: Adjust the fill rate to ensure an optimal balance between grinding media and material. Similarly, control the mill speed to achieve the desired grinding action without excessive energy use. Typically, a fill rate of 30-40% and an optimal speed (70-80% of critical speed) are recommended.
-
Choose Right Steel Ball Ratio:
- Why it matters: The ratio of different-sized steel balls affects the grinding efficiency and the quality of the final product.
- How to implement: Use a mix of different-sized steel balls to ensure efficient grinding of various particle sizes. Larger balls are effective for breaking down coarse particles, while smaller balls are better for fine grinding. Regularly monitor and adjust the ball ratio based on the feed material and desired output.
By systematically addressing these factors, the efficiency of a ball mill can be significantly improved, leading to better performance, reduced energy consumption, and higher-quality output.
Summary Table:
Factor | Why It Matters | How to Implement |
---|---|---|
Control Feed Size | Larger particles require more energy, reducing efficiency. | Use crushers or pre-grinding equipment to reduce feed size. |
Uniform Feeding | Uneven feeding causes inconsistent grinding and potential mill damage. | Use automated feeding systems or vibratory feeders for steady material flow. |
Liner Material & Volume | Affects durability, grinding capacity, and energy efficiency. | Use high-quality, wear-resistant liners and optimize cylinder volume. |
Fill Rate & Mill Speed | Directly influences grinding action and energy consumption. | Maintain a 30-40% fill rate and 70-80% of critical speed for optimal grinding. |
Steel Ball Ratio | Affects grinding efficiency and final product quality. | Use a mix of ball sizes for coarse and fine grinding; adjust based on feed material and output needs. |
Ready to optimize your ball mill efficiency? Contact our experts today for tailored solutions!