A two-stage vacuum pump is generally better than a single-stage pump for applications requiring higher vacuum levels and improved performance. The two-stage design incorporates two sets of rotors and vanes, enabling it to operate in a low vacuum stage and a high vacuum stage. This configuration allows the pump to achieve deeper vacuum levels, making it suitable for applications like ultra-high vacuum (UHV) systems. While single-stage pumps are simpler and cost-effective for basic vacuum needs, two-stage pumps excel in efficiency, pressure range, and overall performance, particularly in demanding industrial or scientific environments.
Key Points Explained:
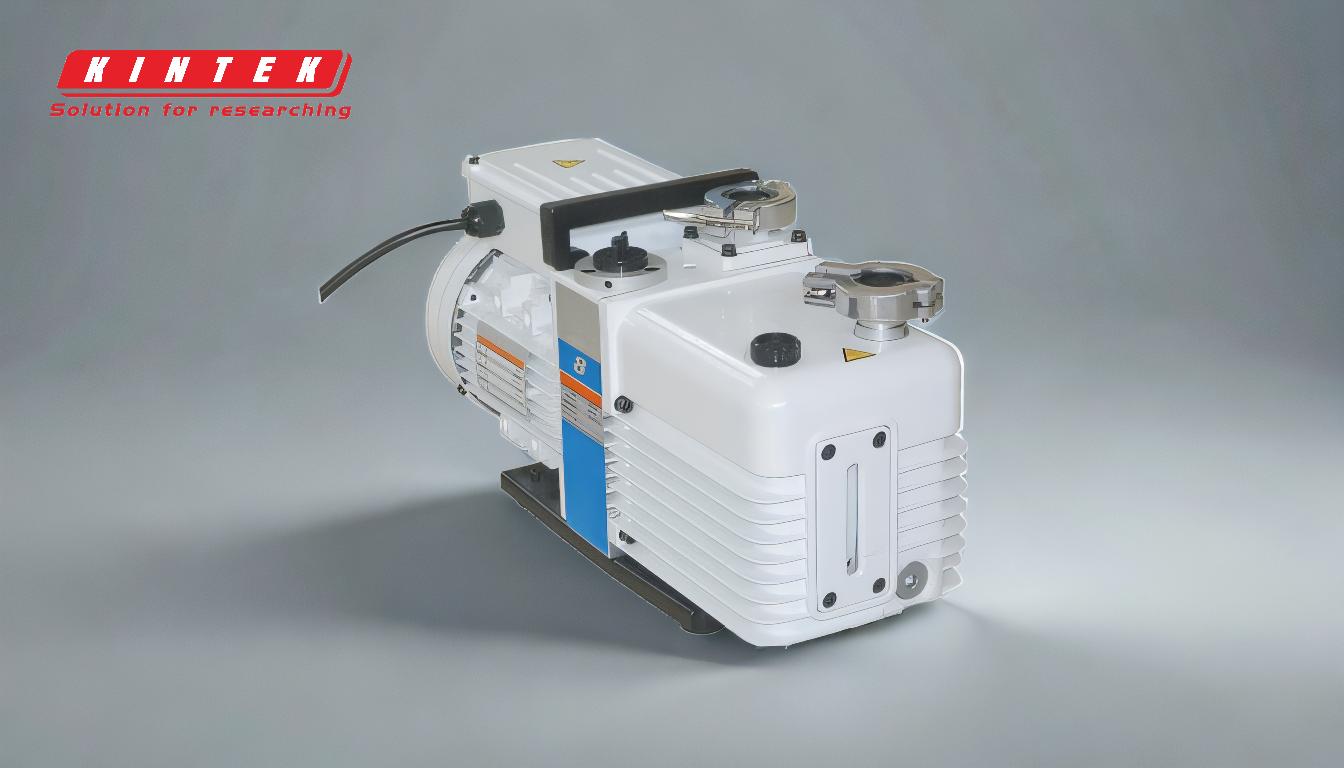
-
Design and Mechanism:
- A two-stage vacuum pump consists of two sets of rotors and vanes, which operate in tandem to create a more efficient vacuum.
- The first stage (high vacuum stage) draws in the process gas, while the second stage (low vacuum stage) compresses the gas to atmospheric pressure. This dual-stage mechanism enhances the pump's ability to achieve deeper vacuum levels compared to a single-stage pump.
-
Vacuum Performance:
- Two-stage pumps can achieve ultra-high vacuum (UHV) levels, making them ideal for applications requiring extremely low pressure environments.
- For example, a two-stage system can increase the pressure level from atmospheric pressure to 4.5 x 10^-2 Torr, which is significantly better than what a single-stage pump can typically achieve.
-
Applications:
- Two-stage vacuum pumps are preferred in industries and scientific research where precise and deep vacuum levels are critical, such as in vacuum furnaces, semiconductor manufacturing, and analytical instrumentation.
- Single-stage pumps, on the other hand, are more suited for simpler applications like vacuum packaging or basic laboratory tasks.
-
Efficiency and Cost:
- While two-stage pumps are more complex and expensive than single-stage pumps, their superior performance and ability to handle demanding applications justify the higher cost.
- Single-stage pumps are more cost-effective for less demanding tasks but may fall short in performance for advanced vacuum requirements.
-
Comparison with Multi-Stage Systems:
- Two-stage pumps are often compared to three-stage systems, which include a diffusion pump. While a three-stage system can achieve even lower pressure levels (e.g., 8.0 x 10^-6 Torr), a two-stage pump offers a balance between performance and complexity, making it a versatile choice for many applications.
In summary, a two-stage vacuum pump is better than a single-stage pump for applications requiring higher vacuum levels and improved efficiency. Its dual-stage design enables it to achieve deeper vacuum levels, making it suitable for demanding industrial and scientific environments. While single-stage pumps are simpler and more cost-effective for basic tasks, two-stage pumps provide superior performance and versatility.
Summary Table:
Feature | Two-Stage Pump | Single-Stage Pump |
---|---|---|
Design | Dual-stage mechanism (two rotors and vanes) | Single-stage mechanism |
Vacuum Level | Ultra-high vacuum (UHV) capable | Limited to basic vacuum levels |
Applications | Industrial, scientific, UHV systems | Vacuum packaging, basic lab tasks |
Efficiency | Higher efficiency and performance | Suitable for less demanding tasks |
Cost | More expensive but justifies superior performance | Cost-effective for basic needs |
Upgrade your vacuum system with a two-stage pump—contact us today for expert advice!