A ball mill is indeed used for fine grinding, as it is designed to reduce materials to very small particle sizes through a combination of impact and abrasion. The process involves filling the mill with grinding media (balls) and the material to be ground, then rotating the mill to create a cascading effect that grinds the material into fine particles. The speed of rotation, the size and type of grinding media, and the duration of grinding all influence the fineness of the final product. Ball mills are widely used in industries such as mining, ceramics, and pharmaceuticals for achieving fine and uniform particle sizes.
Key Points Explained:
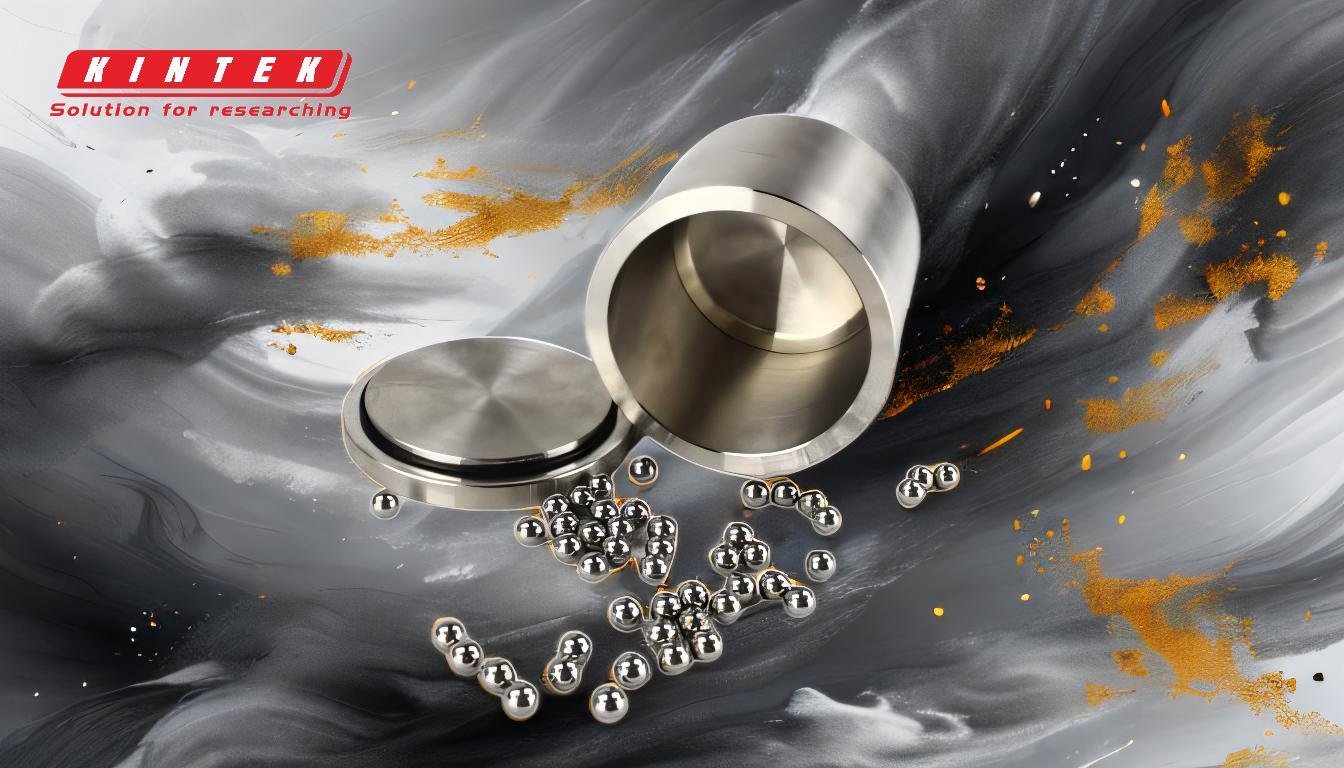
-
Purpose of a Ball Mill:
- A ball mill is primarily used for grinding materials into fine powders. It achieves this by using grinding media (balls) that impact and abrade the material as the mill rotates.
-
Mechanism of Fine Grinding:
- The grinding process in a ball mill involves the following steps:
- Loading: Materials and grinding balls are loaded into the cylinder.
- Rotation: The cylinder rotates, causing the balls to cascade and collide with the material.
- Impact and Abrasion: The collisions between the balls and the material break down the particles into smaller sizes.
- Adjustable Parameters: The speed of rotation, ball size, and grinding duration can be adjusted to achieve the desired fineness.
- The grinding process in a ball mill involves the following steps:
-
Factors Influencing Fine Grinding:
- Speed of Rotation: Higher speeds increase the impact force, leading to finer grinding, but excessive speed can reduce efficiency.
- Grinding Media Size: Smaller balls are more effective for fine grinding as they provide more contact points with the material.
- Duration of Grinding: Longer grinding times generally result in finer particles, but over-grinding can lead to inefficiencies or unwanted changes in material properties.
-
Applications of Fine Grinding:
- Ball mills are used in various industries for fine grinding, including:
- Mining: Grinding ores to extract valuable minerals.
- Ceramics: Producing fine powders for ceramic products.
- Pharmaceuticals: Creating uniform particle sizes for drug formulations.
- Ball mills are used in various industries for fine grinding, including:
-
Advantages of Using a Ball Mill for Fine Grinding:
- Versatility: Can grind a wide range of materials.
- Uniformity: Produces consistent particle sizes.
- Scalability: Suitable for both laboratory and industrial-scale operations.
-
Limitations:
- Energy Consumption: Ball mills can be energy-intensive, especially for very fine grinding.
- Heat Generation: Prolonged grinding can generate heat, which may affect heat-sensitive materials.
In summary, a ball mill is an effective tool for fine grinding, offering versatility and uniformity in particle size reduction. Its performance can be optimized by adjusting key parameters such as rotation speed, grinding media size, and grinding duration.
Summary Table:
Aspect | Details |
---|---|
Purpose | Grinding materials into fine powders using grinding media (balls). |
Mechanism | Rotation causes cascading balls to impact and abrade materials. |
Key Parameters | Rotation speed, grinding media size, and duration influence fineness. |
Applications | Mining, ceramics, pharmaceuticals for fine and uniform particle sizes. |
Advantages | Versatile, uniform particle sizes, scalable for lab and industrial use. |
Limitations | Energy-intensive, heat generation may affect heat-sensitive materials. |
Optimize your fine grinding process with a ball mill—contact us today for expert advice!