Isostatic pressing can be considered expensive depending on the context, but it also offers cost-effective advantages in certain scenarios. The process involves higher tooling costs and complexity compared to uniaxial pressing, and it may require expensive materials like spray-dried powder. Additionally, the lower accuracy of pressed surfaces often necessitates subsequent machining, increasing overall costs. However, isostatic pressing is cost-effective for bonding dissimilar metals, producing complex parts, and achieving high-density compacts with low distortion. The lower mold costs and ability to handle intricate designs make it a viable option for specific applications, offsetting some of the initial expenses.
Key Points Explained:
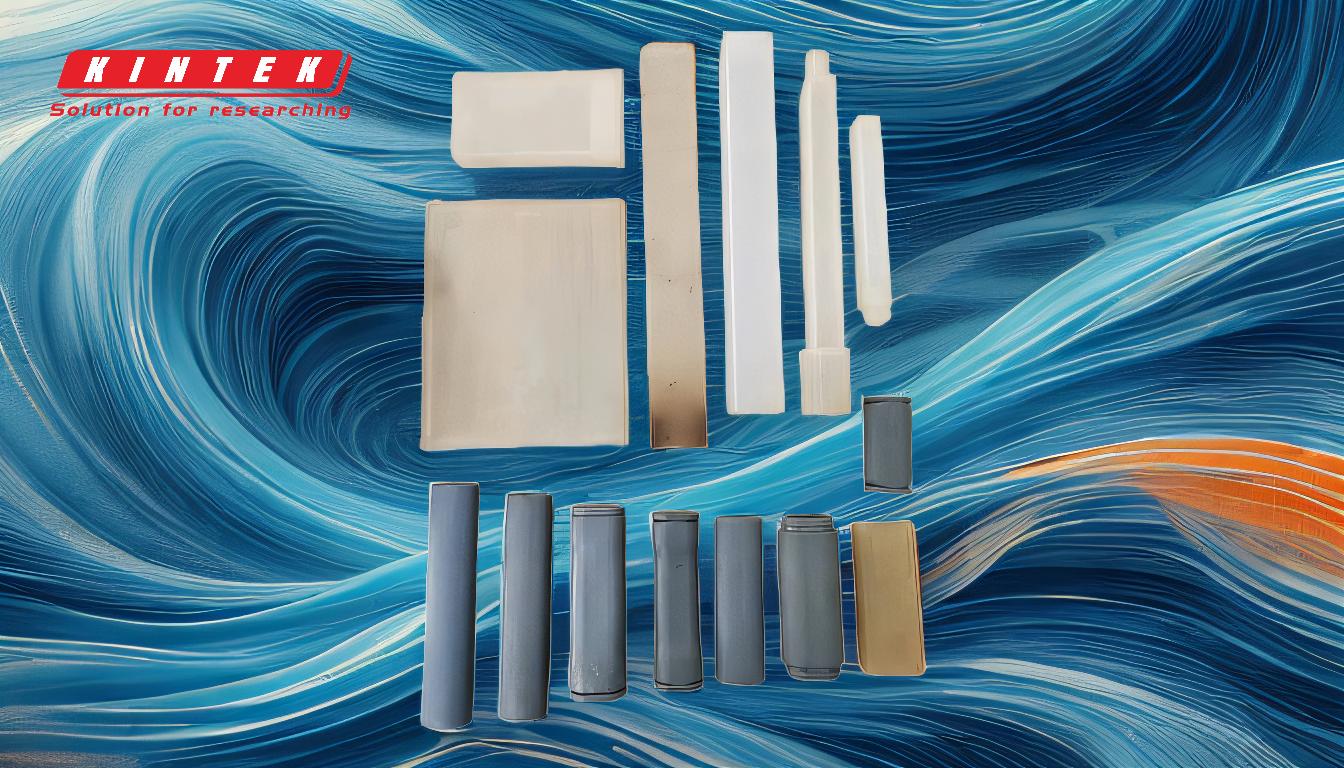
-
Higher Tooling Costs and Complexity:
- Isostatic pressing requires more complex tooling compared to uniaxial pressing, which increases initial setup costs.
- The process involves specialized equipment and flexible bags, adding to the overall expense.
-
Material Costs:
- The use of relatively expensive spray-dried powder is often necessary for fully automatic dry bag presses.
- This material requirement can significantly impact the overall cost of the process.
-
Post-Processing Costs:
- The lower accuracy of pressed surfaces adjacent to the flexible bag often necessitates subsequent machining.
- This additional step increases the total cost of production, as it requires extra labor and resources.
-
Production Rates:
- Isostatic pressing generally has lower production rates compared to extrusion or die compaction.
- Slower production can lead to higher costs per unit, especially for large-scale manufacturing.
-
Cost-Effective Advantages:
- Bonding Dissimilar Metals: Hot isostatic pressing is cost-effective for bonding dissimilar metals, which would otherwise be expensive using diffusion bonding.
- Complex Parts: The lower cost of molds makes isostatic pressing a cost-effective solution for producing complex parts.
- High-Density Compacts: The process achieves higher density for a given pressing pressure compared to mechanical pressing, reducing material waste and potentially lowering costs.
-
Specialized Applications:
- The ability to press compacts with very high length-diameter ratios, internal shapes, and weak powders offers unique advantages that can justify the higher costs in specific applications.
- The low distortion and consistent shrinkage on firing reduce the need for additional corrections, saving costs in the long run.
-
Wet Bag vs. Dry Bag Pressing:
- Wet bag pressing has lower tooling costs and is suitable for very large pressed parts, making it more cost-effective for certain applications.
- Dry bag pressing, while more automated, requires more expensive materials and has higher initial costs.
In summary, while isostatic pressing can be expensive due to higher tooling and material costs, slower production rates, and the need for post-processing, it offers significant cost advantages in specific scenarios such as bonding dissimilar metals, producing complex parts, and achieving high-density compacts. The decision to use isostatic pressing should be based on a thorough cost-benefit analysis tailored to the specific requirements of the project.
Summary Table:
Aspect | Details |
---|---|
Tooling Costs | Higher complexity and initial setup costs compared to uniaxial pressing. |
Material Costs | Requires expensive materials like spray-dried powder. |
Post-Processing Costs | Additional machining needed due to lower surface accuracy. |
Production Rates | Slower than extrusion or die compaction, increasing costs per unit. |
Cost-Effective Uses | Bonding dissimilar metals, producing complex parts, and high-density compacts. |
Specialized Applications | Ideal for parts with high length-diameter ratios and intricate designs. |
Wet vs. Dry Bag Pressing | Wet bag: lower tooling costs; Dry bag: higher automation but more expensive. |
Discover how isostatic pressing can meet your project's needs—contact us today for expert advice!