No, PVD (Physical Vapor Deposition) and powder coating are not the same. While both are surface coating techniques used to enhance durability, corrosion resistance, and aesthetics, they differ significantly in their processes, materials, applications, and environmental impact. PVD involves depositing thin layers of metals, alloys, or ceramics in a vacuum at high temperatures, resulting in dense, durable, and environmentally friendly coatings. Powder coating, on the other hand, uses electrostatic charges to apply organic polymers at lower temperatures, offering a wider range of colors and finishes but being less durable and more prone to fading over time. PVD is more specialized and expensive, requiring advanced equipment, while powder coating is cost-effective and widely used for various industrial and decorative applications.
Key Points Explained:
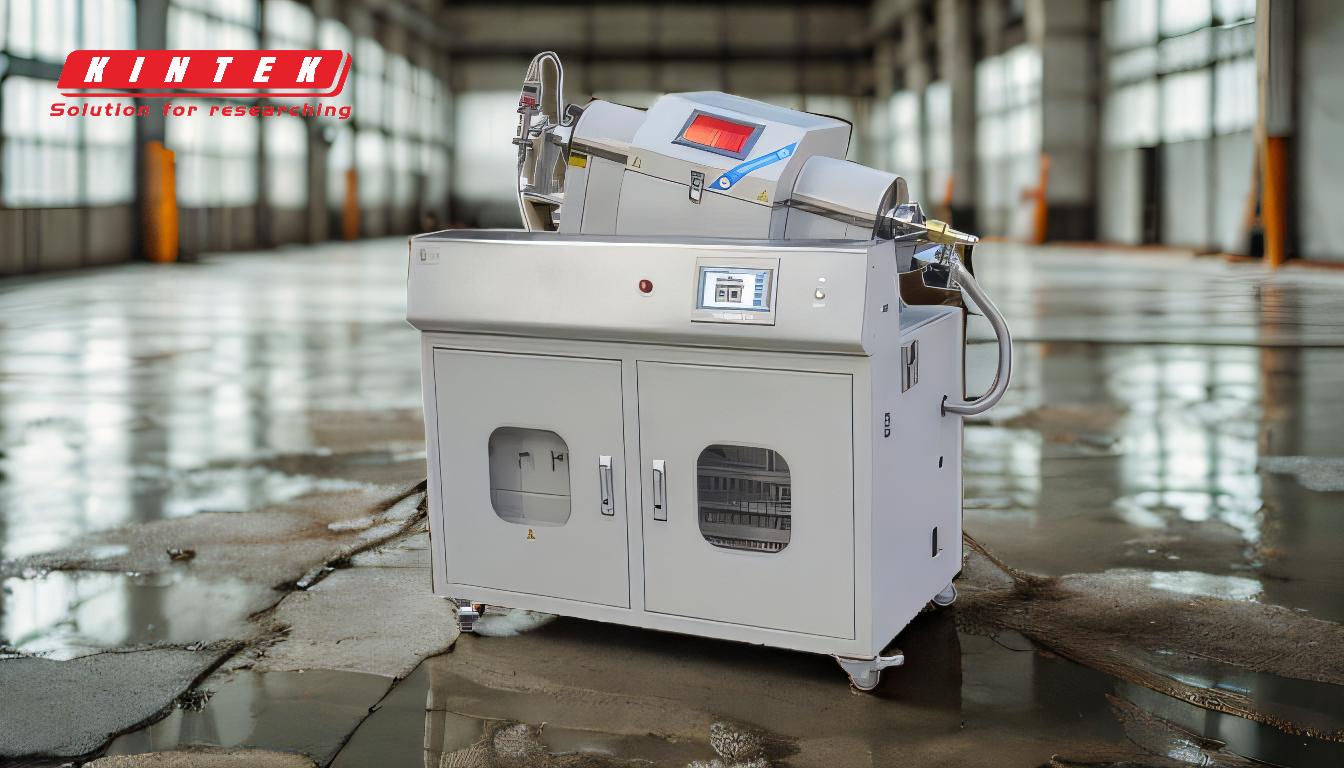
-
Definition and Process:
-
PVD Coating:
- PVD is a vacuum-based coating process where materials like metals, alloys, or ceramics are vaporized and deposited onto a substrate in thin layers (0.5 to 5 microns).
- It involves high temperatures and physical processes, creating dense and durable coatings.
-
Powder Coating:
- Powder coating uses an electrostatic charge to apply dry polymer powder to a surface, which is then cured at lower temperatures to form a hard finish.
- It is limited to organic polymers and does not require a vacuum or high-temperature environment.
-
PVD Coating:
-
Materials Used:
-
PVD Coating:
- Can deposit a wide range of materials, including metals (e.g., titanium, chromium), alloys, and ceramics.
- This versatility allows for specialized applications requiring high durability and specific material properties.
-
Powder Coating:
- Limited to organic polymers, such as epoxy, polyester, or acrylic.
- Offers a broader range of colors and finishes, making it ideal for decorative purposes.
-
PVD Coating:
-
Durability and Performance:
-
PVD Coating:
- Known for its exceptional durability, corrosion resistance, and longevity.
- Less prone to fading or discoloration over time, making it suitable for high-performance applications.
-
Powder Coating:
- While durable, it is generally less robust than PVD coatings.
- Can fade or degrade over time, especially when exposed to harsh environmental conditions.
-
PVD Coating:
-
Environmental Impact:
-
PVD Coating:
- More environmentally friendly, as it produces no waste or harmful gases.
- Considered an ethical alternative to traditional coating methods like chrome plating.
-
Powder Coating:
- Also environmentally friendly compared to liquid coatings, as it produces minimal waste and volatile organic compounds (VOCs).
- However, it may involve some waste during application.
-
PVD Coating:
-
Cost and Equipment:
-
PVD Coating:
- Requires specialized equipment, including large vacuum chambers, making it more expensive and less accessible for small-scale applications.
- Higher upfront costs but longer-lasting results.
-
Powder Coating:
- Less expensive and widely available, requiring simpler equipment.
- More cost-effective for large-scale or decorative projects.
-
PVD Coating:
-
Applications:
-
PVD Coating:
- Commonly used in industries requiring high-performance coatings, such as automotive, aerospace, medical devices, and cutting tools.
- Ideal for applications where durability, precision, and material versatility are critical.
-
Powder Coating:
- Widely used for industrial and decorative purposes, including automotive parts, appliances, furniture, and architectural components.
- Suitable for projects where aesthetics and cost-effectiveness are prioritized.
-
PVD Coating:
In summary, PVD and powder coating serve different purposes and are chosen based on the specific requirements of the application. PVD is more advanced, durable, and environmentally friendly but comes at a higher cost and complexity. Powder coating is more accessible, cost-effective, and versatile in terms of colors and finishes but is less durable over time.
Summary Table:
Aspect | PVD Coating | Powder Coating |
---|---|---|
Process | Vacuum-based, high-temperature deposition of metals, alloys, or ceramics. | Electrostatic application of dry polymer powder, cured at lower temps. |
Materials | Metals, alloys, ceramics. | Organic polymers (e.g., epoxy, polyester). |
Durability | Highly durable, corrosion-resistant, and long-lasting. | Less durable, prone to fading over time. |
Environmental Impact | No waste or harmful gases, eco-friendly. | Minimal waste and VOCs, but some waste during application. |
Cost | Expensive, requires specialized equipment. | Cost-effective, widely available. |
Applications | Automotive, aerospace, medical devices, cutting tools. | Automotive parts, appliances, furniture, architectural components. |
Still unsure which coating is right for your project? Contact us today for expert advice!