The particle size distribution in milling is influenced by several factors, including the size and density of grinding balls, milling time, number of grinding cycles, residence time, feed rate, rotation speed, and temperature. Smaller grinding balls and longer milling times generally produce smaller particles, as they increase the frequency of collisions and the energy transferred to the material. The number of grinding cycles and residence time directly affect the degree of size reduction, with more cycles leading to finer particles. Additionally, the nature of the material being milled, the feed rate, and the rotation speed of the mill also play significant roles. Temperature can influence the balance between defect generation and recombination, affecting the final grain size.
Key Points Explained:
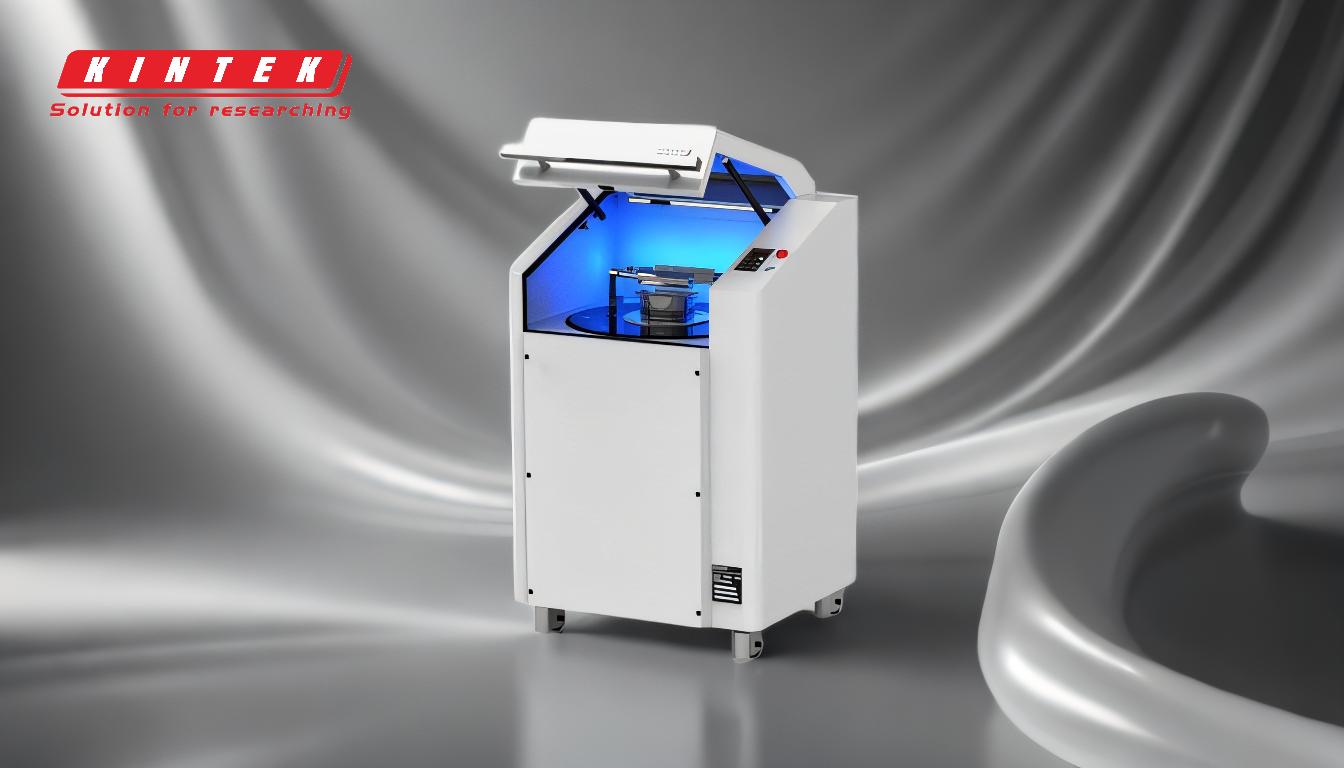
-
Grinding Ball Size and Density:
- Explanation: Smaller grinding balls are more effective at producing smaller particles because they increase the frequency of collisions and the energy transferred to the material. The density of the balls also affects the impact force, with denser materials providing more effective milling.
- Impact on Particle Size: Smaller and denser balls lead to finer particles due to increased collision frequency and energy transfer.
-
Milling Time and Number of Grinding Cycles:
- Explanation: Longer milling times and more grinding cycles allow for more collisions and energy transfer, leading to greater size reduction. Each cycle contributes to the erosion of larger particles into smaller fragments.
- Impact on Particle Size: Increased milling time and cycles result in a higher number of smaller particles, as larger particles are progressively broken down.
-
Residence Time:
- Explanation: The time the material spends inside the mill chamber affects the degree of size reduction. Longer residence times allow for more interactions between the grinding media and the material.
- Impact on Particle Size: Longer residence times generally lead to finer particles due to increased exposure to grinding forces.
-
Feed Rate and Level in the Vessel:
- Explanation: The rate at which material is fed into the mill and the level of material in the vessel can influence the efficiency of the milling process. Optimal feed rates ensure consistent milling, while the level affects the interaction between the material and the grinding media.
- Impact on Particle Size: Proper feed rates and vessel levels ensure efficient milling, leading to more uniform particle size distribution.
-
Rotation Speed of the Cylinder:
- Explanation: The speed at which the mill cylinder rotates affects the kinetic energy of the grinding balls and the frequency of collisions. Higher speeds can increase the energy transferred to the material.
- Impact on Particle Size: Higher rotation speeds can lead to finer particles due to increased collision frequency and energy transfer.
-
Nature of the Grinding Material:
- Explanation: The physical and chemical properties of the material being milled, such as hardness and brittleness, influence how it responds to milling. Harder materials may require more energy to achieve size reduction.
- Impact on Particle Size: The nature of the material determines the ease with which it can be milled, affecting the final particle size distribution.
-
Temperature:
- Explanation: Temperature can influence the balance between defect generation and recombination during milling. Higher temperatures may facilitate defect recovery, affecting the final grain size.
- Impact on Particle Size: Temperature control is crucial for achieving the desired particle size, as it affects the material's response to milling forces.
By understanding and optimizing these factors, one can achieve the desired particle size distribution in milling processes. Each factor plays a critical role in the efficiency and effectiveness of the milling process, and their interplay determines the final outcome.
Summary Table:
Factor | Impact on Particle Size |
---|---|
Grinding Ball Size & Density | Smaller, denser balls lead to finer particles due to increased collision frequency and energy transfer. |
Milling Time & Cycles | Longer milling times and more cycles result in finer particles by breaking down larger fragments. |
Residence Time | Longer residence times lead to finer particles due to increased exposure to grinding forces. |
Feed Rate & Vessel Level | Optimal feed rates and vessel levels ensure efficient milling and uniform particle size. |
Rotation Speed | Higher speeds increase collision frequency and energy transfer, producing finer particles. |
Grinding Material Nature | Material hardness and brittleness determine ease of milling and final particle size. |
Temperature | Temperature affects defect generation and recombination, influencing final grain size. |
Need help optimizing your milling process? Contact our experts today for tailored solutions!