Ball mills are widely used in various industries for grinding and mixing materials, offering several advantages such as producing fine powders, handling toxic materials safely, and being suitable for both wet and dry grinding. However, they also have notable disadvantages, including high energy consumption, noise, and limitations in handling certain materials. Understanding these pros and cons is crucial for equipment purchasers to make informed decisions based on their specific needs.
Key Points Explained:
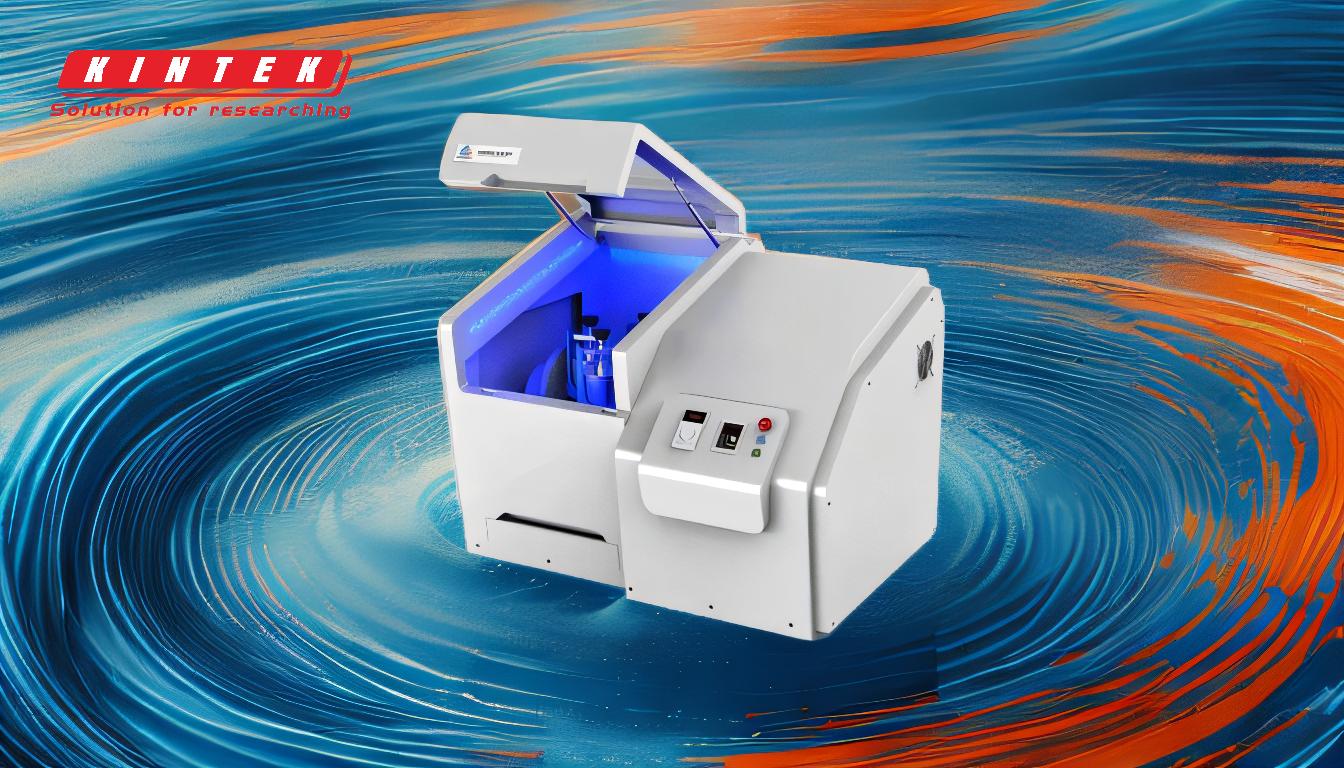
-
Advantages of Ball Mills:
-
Produces Very Fine Powder:
- Ball mills can produce powders with particle sizes as small as 10 microns, making them ideal for applications requiring fine grinding.
-
Suitability for Milling Toxic Materials:
- The enclosed form of ball mills allows for safe handling of toxic materials, preventing exposure and contamination.
-
Wide Range of Applications:
- Ball mills are versatile and can be used in various industries, including pharmaceuticals, chemicals, and mining.
-
Continuous Operation Capability:
- They can operate continuously, which is beneficial for large-scale production processes.
-
Effectiveness in Milling Abrasive Materials:
- Ball mills are effective in grinding abrasive materials, making them suitable for tough grinding tasks.
-
Suitability for Both Wet and Dry Grinding:
- They can handle both wet and dry grinding processes, providing flexibility in operation.
-
Sterility Maintenance:
- The closed container system helps maintain sterility, which is crucial in industries like pharmaceuticals.
-
Ease of Particle Size Reduction:
- Ball mills simplify the process of reducing particle size, which is essential for many industrial applications.
-
Low Energy Consumption:
- Compared to other grinding methods, ball mills can be more energy-efficient.
-
Easy Cleaning and Low Maintenance Costs:
- They are relatively easy to clean and maintain, leading to lower operational costs.
-
Produces Very Fine Powder:
-
Disadvantages of Ball Mills:
-
High Specific Energy Consumption:
- Ball mills consume a significant amount of energy, primarily due to wear of balls and wall armor, friction, and material heating.
-
Noise and Vibrations:
- The operation of ball mills can produce strong vibrations and noise, although using rubber balls can mitigate this to some extent.
-
Slow Process:
- Grinding in ball mills can be a slow process, which may not be suitable for time-sensitive applications.
-
Inability to Handle Certain Materials:
- Ball mills are not effective in reducing soft, tacky, and fibrous materials.
-
Wear and Contamination:
- Wear inside the cylinders can lead to contamination of the material being ground.
-
Limited Capacity:
- Ball mills have a limited capacity for handling large quantities, which can be a drawback for high-volume production needs.
-
High Specific Energy Consumption:
By weighing these advantages and disadvantages, purchasers can determine whether a ball mill is the right equipment for their specific grinding needs.
Summary Table:
Advantages | Disadvantages |
---|---|
Produces very fine powder (up to 10 microns) | High specific energy consumption |
Safe handling of toxic materials | Noise and vibrations |
Wide range of applications | Slow grinding process |
Continuous operation capability | Ineffective for soft, tacky, and fibrous materials |
Effective for abrasive materials | Wear and contamination risks |
Suitable for wet and dry grinding | Limited capacity for high-volume production |
Maintains sterility in pharmaceutical use | |
Low energy consumption compared to alternatives | |
Easy cleaning and low maintenance costs |
Still unsure if a ball mill is right for your needs? Contact our experts today for personalized advice!