Selective Laser Sintering (SLS) is a popular additive manufacturing process that uses a laser to sinter powdered material into a solid structure. The two main materials used in SLS are engineering polymers, primarily based on polyamides. Polyamide 12 (PA 12) is the most dominant material, accounting for approximately 90% of the SLS material market. This material is favored for its excellent mechanical properties, durability, and versatility in producing functional prototypes and end-use parts. Other polyamides, such as Polyamide 11 (PA 11), are also used but to a lesser extent. These materials are chosen for their ability to produce high-quality, durable parts with good surface finish and dimensional accuracy.
Key Points Explained:
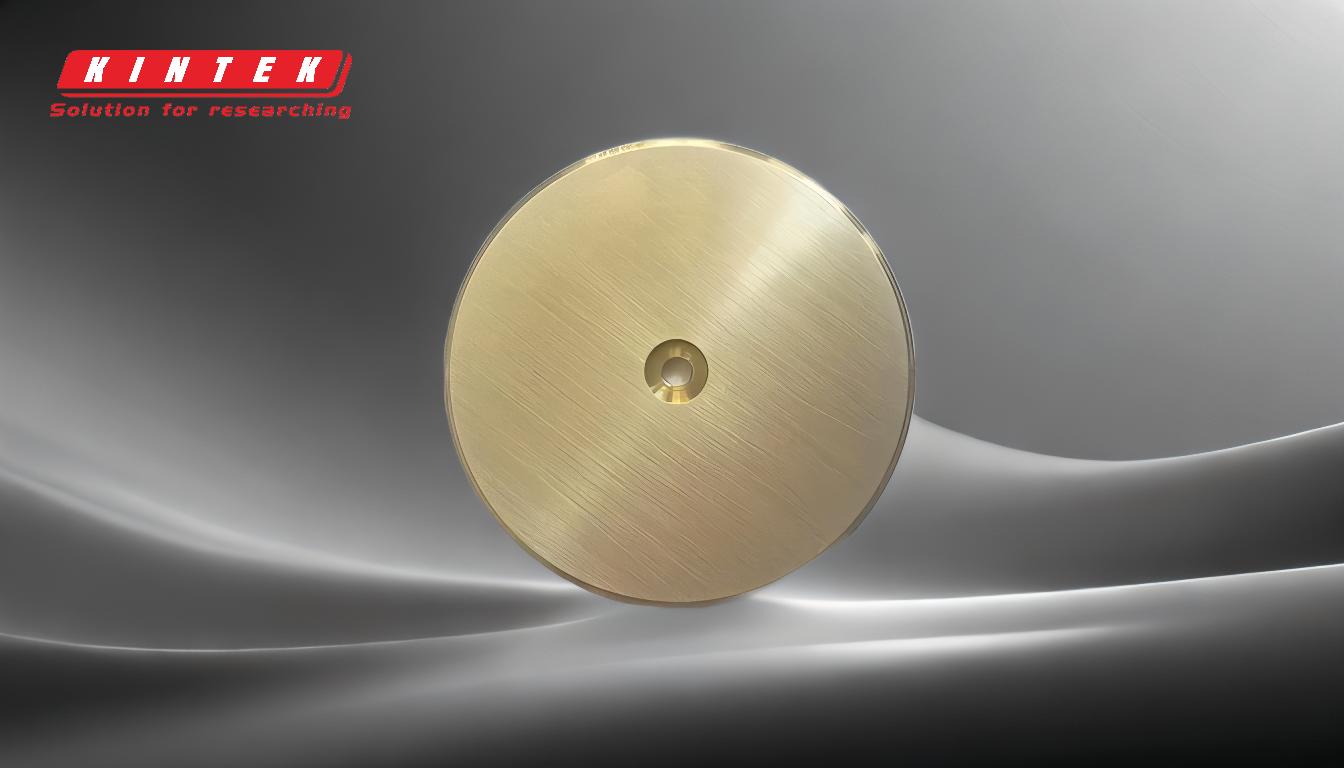
-
Polyamide 12 (PA 12):
- Dominance in the Market: PA 12 is the most widely used material in SLS, making up about 90% of the market. Its popularity is due to its excellent balance of mechanical properties, including strength, flexibility, and durability.
- Applications: PA 12 is used in a variety of applications, from functional prototypes to end-use parts in industries such as automotive, aerospace, and medical devices. Its ability to produce parts with high accuracy and good surface finish makes it ideal for these applications.
- Properties: PA 12 offers good chemical resistance, low moisture absorption, and excellent thermal stability, which are crucial for parts that need to withstand harsh environments.
-
Polyamide 11 (PA 11):
- Less Common but Significant: While PA 11 is not as widely used as PA 12, it still holds significance in the SLS material market. It is often chosen for specific applications where its unique properties are beneficial.
- Applications: PA 11 is used in applications that require higher impact resistance and flexibility compared to PA 12. It is also preferred for parts that need to be more ductile and less brittle.
- Properties: PA 11 has better impact resistance and flexibility than PA 12, making it suitable for parts that undergo significant mechanical stress. It also has good chemical resistance and is more environmentally friendly, as it is derived from renewable resources.
-
Other Materials:
- Thermoplastic Elastomers (TPE): These materials are used in SLS for applications requiring flexibility and elasticity. They are ideal for producing parts like gaskets, seals, and soft-touch components.
- Composites: Some SLS processes use composite materials, which combine polymers with fillers like glass or carbon fibers to enhance mechanical properties. These composites are used in high-performance applications where additional strength and stiffness are required.
-
Material Selection Considerations:
- Mechanical Properties: The choice of material in SLS is heavily influenced by the required mechanical properties of the final part. Factors such as tensile strength, elongation at break, and impact resistance are critical in determining the suitability of a material for a specific application.
- Surface Finish and Dimensional Accuracy: Materials must also provide a good surface finish and dimensional accuracy to meet the quality standards of the final product. PA 12 and PA 11 are known for their ability to produce parts with excellent surface finish and high precision.
- Environmental and Chemical Resistance: For parts exposed to harsh environments or chemicals, materials with good environmental and chemical resistance, like PA 12 and PA 11, are preferred.
-
Future Trends:
- Development of New Materials: The SLS material market is continuously evolving, with ongoing research and development aimed at introducing new materials with enhanced properties. This includes high-temperature polymers, biocompatible materials, and materials with improved sustainability profiles.
- Sustainability: There is a growing trend towards using more sustainable materials in SLS, such as bio-based polymers and recyclable materials. This aligns with the broader industry shift towards environmentally friendly manufacturing practices.
In summary, the two main materials used in Selective Laser Sintering are polyamide-based polymers, with Polyamide 12 being the most prevalent due to its excellent mechanical properties and versatility. Polyamide 11, while less common, is also significant for specific applications requiring higher impact resistance and flexibility. The choice of material depends on the desired mechanical properties, surface finish, and environmental resistance of the final part. As the SLS technology continues to advance, we can expect the development of new materials that offer enhanced performance and sustainability.
Summary Table:
Material | Key Properties | Applications |
---|---|---|
Polyamide 12 (PA 12) | Excellent mechanical properties, durability, chemical resistance | Functional prototypes, automotive, aerospace, medical devices |
Polyamide 11 (PA 11) | High impact resistance, flexibility, eco-friendly | Parts requiring ductility, renewable resource-based applications |
Thermoplastic Elastomers (TPE) | Flexibility, elasticity | Gaskets, seals, soft-touch components |
Composites | Enhanced strength, stiffness | High-performance applications |
Need help selecting the right SLS material for your project? Contact our experts today!