Injection molding is a widely used manufacturing process for producing plastic parts. It involves melting plastic resin and injecting it into a mold to create a desired shape. The process is divided into four distinct stages: Clamping, Injection, Cooling, and Ejection. Each stage plays a critical role in ensuring the final product meets the required specifications. Below, we will explore these stages in detail, focusing on their significance and how they contribute to the overall success of the injection molding process.
Key Points Explained:
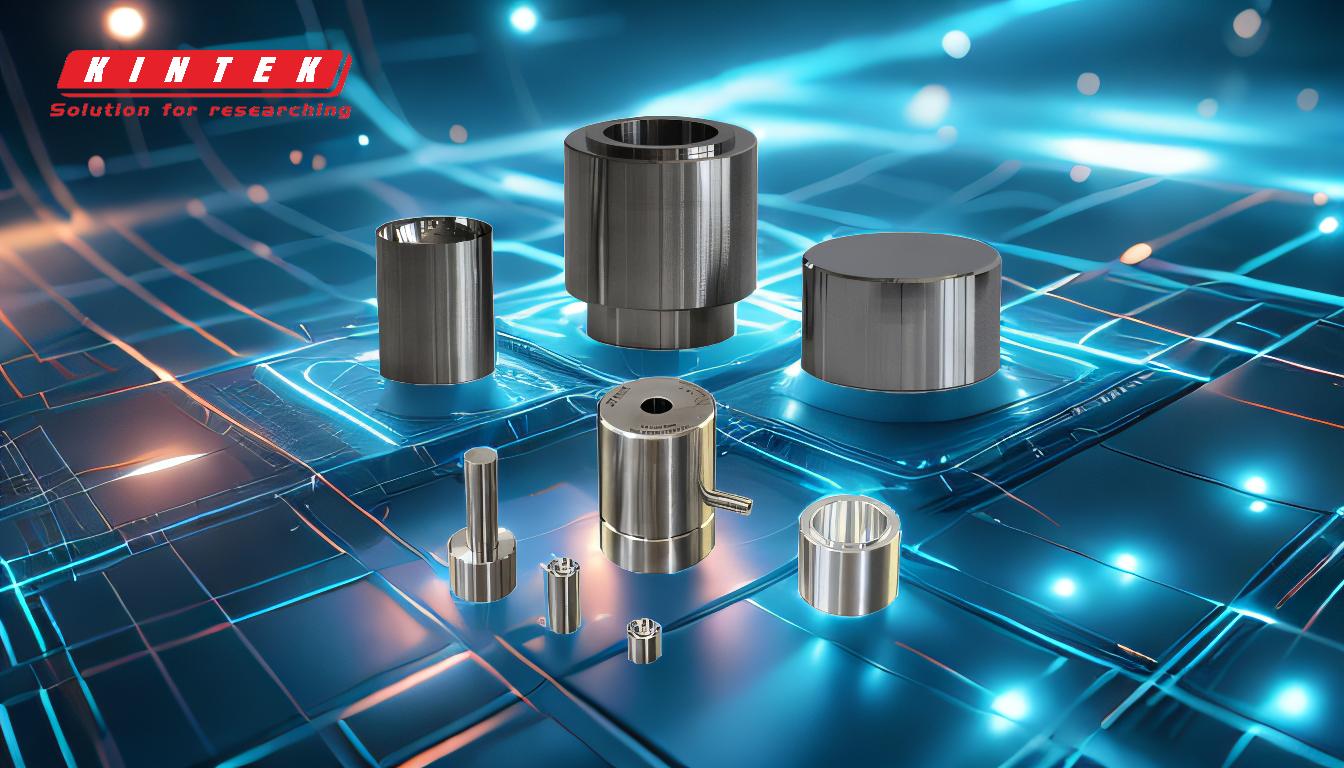
-
Clamping
- Purpose: The clamping stage ensures that the mold remains securely closed during the injection process.
- Process: The two halves of the mold (the stationary and moving halves) are brought together and held tightly by a clamping unit. This unit applies sufficient force to prevent the mold from opening due to the high pressure of the injected material.
-
Key Considerations:
- The clamping force must be carefully calculated based on the size of the mold and the material being used.
- Insufficient clamping force can lead to defects like flash (excess material escaping from the mold).
- Relevance for Purchasers: When selecting an injection molding machine, ensure the clamping force matches the requirements of the molds and materials you plan to use.
-
Injection
- Purpose: This stage involves injecting the melted plastic resin into the mold cavity.
- Process: The plastic resin is fed into the injection molding machine's barrel, where it is heated to a molten state. A screw or plunger then pushes the molten material into the mold under high pressure.
-
Key Considerations:
- The injection speed, pressure, and temperature must be precisely controlled to ensure proper filling of the mold.
- Variations in these parameters can lead to defects such as short shots (incomplete filling) or warping.
- Relevance for Purchasers: Ensure the injection molding machine has precise control over injection parameters to achieve consistent part quality.
-
Cooling
- Purpose: The cooling stage allows the molten plastic to solidify and take the shape of the mold.
- Process: After the mold is filled, the plastic begins to cool and harden. Cooling time depends on factors like the material's thermal properties, part thickness, and mold design.
-
Key Considerations:
- Proper cooling is essential to avoid defects like sink marks (depressions on the surface) or internal stresses.
- Cooling channels within the mold help regulate temperature and speed up the process.
- Relevance for Purchasers: Consider the cooling efficiency of the mold and machine, as longer cooling times can reduce production efficiency.
-
Ejection
- Purpose: The ejection stage removes the solidified part from the mold.
- Process: Once the part has sufficiently cooled, the mold opens, and ejector pins or plates push the part out of the mold cavity.
-
Key Considerations:
- The ejection system must be carefully designed to avoid damaging the part or the mold.
- Improper ejection can lead to defects like scratches or deformation.
- Relevance for Purchasers: Ensure the mold design and ejection system are compatible with the part geometry and material to minimize defects and downtime.
By understanding these four stages, purchasers can make informed decisions about equipment and materials, ensuring optimal production efficiency and part quality.
Summary Table:
Stage | Purpose | Key Considerations | Relevance for Purchasers |
---|---|---|---|
Clamping | Secures the mold during injection. | - Clamping force must match mold and material requirements. | Ensure the machine's clamping force aligns with your production needs. |
Injection | Injects molten plastic into the mold. | - Precise control of speed, pressure, and temperature is critical. | Choose a machine with advanced injection parameter controls for consistent quality. |
Cooling | Allows the plastic to solidify into the desired shape. | - Proper cooling prevents defects like sink marks or internal stresses. | Evaluate cooling efficiency to optimize production speed and part quality. |
Ejection | Removes the solidified part from the mold. | - Ejection system must avoid damaging the part or mold. | Ensure compatibility between mold design and part geometry to minimize defects. |
Optimize your injection molding process today—contact our experts for tailored solutions!