The ball milling process offers numerous advantages, making it a widely used method in various industries. It is cost-effective, easy to perform, and capable of producing fine powders with particle sizes as small as 10 microns. The process is versatile, suitable for both wet and dry grinding, and can handle toxic, abrasive, and sensitive materials due to its enclosed system. Ball milling also ensures sterility, low energy consumption, and minimal maintenance requirements. Additionally, it can create crystal defects, which are beneficial for specific applications, and offers continuous operation capabilities. These features make ball milling a reliable and efficient method for material processing.
Key Points Explained:
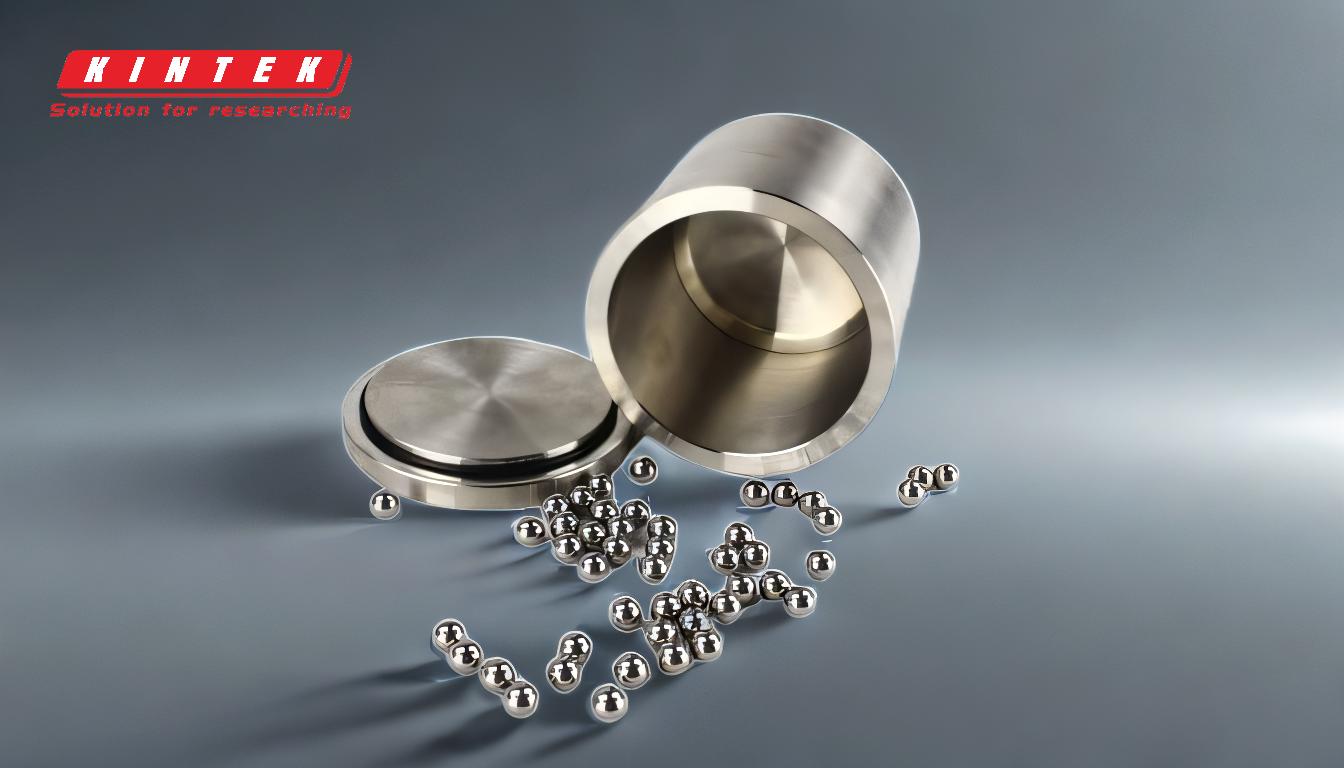
-
Cost-Effectiveness and Ease of Operation:
- Ball milling is an inexpensive method that is easy to set up and perform. This makes it accessible for a wide range of applications, from small-scale laboratories to large industrial operations.
- The simplicity of the process reduces the need for specialized training, further lowering operational costs.
-
Production of Fine Powder:
- One of the most significant advantages of ball milling is its ability to produce very fine powders with particle sizes less than or equal to 10 microns. This is particularly useful in industries requiring ultra-fine materials, such as pharmaceuticals, cosmetics, and advanced materials.
-
Versatility in Applications:
- Ball milling is suitable for a wide range of materials, including metals, ceramics, polymers, and composites. This versatility makes it a preferred choice across various industries.
- It can handle both wet and dry grinding processes, providing flexibility depending on the material and desired outcome.
-
Handling of Toxic and Abrasive Materials:
- The enclosed system of a ball mill makes it ideal for milling toxic materials safely, preventing exposure to harmful substances.
- It is also effective in milling abrasive materials, which can wear down other types of equipment. The robust design of ball mills ensures longevity and consistent performance even with challenging materials.
-
Continuous Operation Capability:
- Ball mills can operate continuously, which is beneficial for large-scale production. This continuous operation capability ensures a steady output, making it efficient for industrial applications.
-
Sterility and Low Contamination:
- The closed container system of ball mills helps maintain sterility, which is crucial in industries like pharmaceuticals and food processing.
- The process also minimizes contamination, ensuring the purity of the final product.
-
Low Energy Consumption and Maintenance:
- Ball milling is known for its low energy consumption compared to other grinding methods. This makes it an environmentally friendly and cost-effective option.
- The maintenance requirements are minimal, reducing downtime and operational costs.
-
Creation of Crystal Defects:
- The ball milling process can introduce crystal defects in materials, which can be beneficial for certain applications. These defects can enhance the material's properties, such as increased reactivity or improved mechanical strength.
-
Space Efficiency:
- Ball mills require minimal space for installation, making them suitable for facilities with limited space. This compact design is advantageous for small laboratories or crowded industrial environments.
-
Cryo-Milling Advantages:
- Cryo-milling, a variant of ball milling, offers additional benefits such as the ability to reduce materials to nanoscale powders in a short time (1–3 hours).
- The low-temperature processing eliminates hazardous reactions and emissions, making it a safer and more environmentally friendly option.
- It allows for the direct extraction of materials without the need for additional chemical methods, simplifying the process and reducing costs.
-
Uniform Particle Size Distribution:
- The vibration milling process, another variant, ensures efficient particle size reduction and uniform particle size distribution. This uniformity is crucial for applications requiring consistent material properties.
In summary, the ball milling process is a highly advantageous method for material processing due to its cost-effectiveness, versatility, ability to produce fine powders, and suitability for handling a wide range of materials. Its enclosed system ensures safety and sterility, while its low energy consumption and maintenance requirements make it an efficient and sustainable choice. The ability to create crystal defects and the additional benefits of cryo-milling further enhance its value in various industrial applications.
Summary Table:
Advantage | Key Benefits |
---|---|
Cost-Effectiveness | Inexpensive setup and operation, reduces training and operational costs. |
Fine Powder Production | Produces particles as small as 10 microns, ideal for pharmaceuticals and cosmetics. |
Versatility | Suitable for wet/dry grinding, metals, ceramics, polymers, and composites. |
Handling Toxic/Abrasive Materials | Enclosed system ensures safety and longevity with challenging materials. |
Continuous Operation | Steady output for large-scale industrial applications. |
Sterility and Low Contamination | Maintains purity, crucial for pharmaceuticals and food processing. |
Low Energy Consumption | Environmentally friendly and cost-efficient. |
Crystal Defects Creation | Enhances material properties like reactivity and mechanical strength. |
Space Efficiency | Compact design suitable for small labs or crowded facilities. |
Cryo-Milling Benefits | Nanoscale powder production, low-temperature processing, and reduced emissions. |
Uniform Particle Size | Ensures consistent material properties for various applications. |
Unlock the full potential of ball milling for your material processing needs—contact us today to learn more!