A colloid mill is a precision machine designed for particle size reduction, emulsification, homogenization, and dispersion of materials. It operates on the rotor-stator principle, where a rapidly rotating rotor and a stationary stator create shear forces in a narrow gap, breaking down solid materials into fine particles. The key components of a colloid mill include the rotor, stator, housing, drive system, adjustment mechanism, and optional features like overload pressure release mechanisms. These components are typically made from high-quality materials like stainless steel to ensure durability, hygiene, and compliance with industry standards such as cGMP. The mill is compact, easy to use, and requires minimal maintenance, making it suitable for various industries, including food, pharmaceuticals, and chemicals.
Key Points Explained:
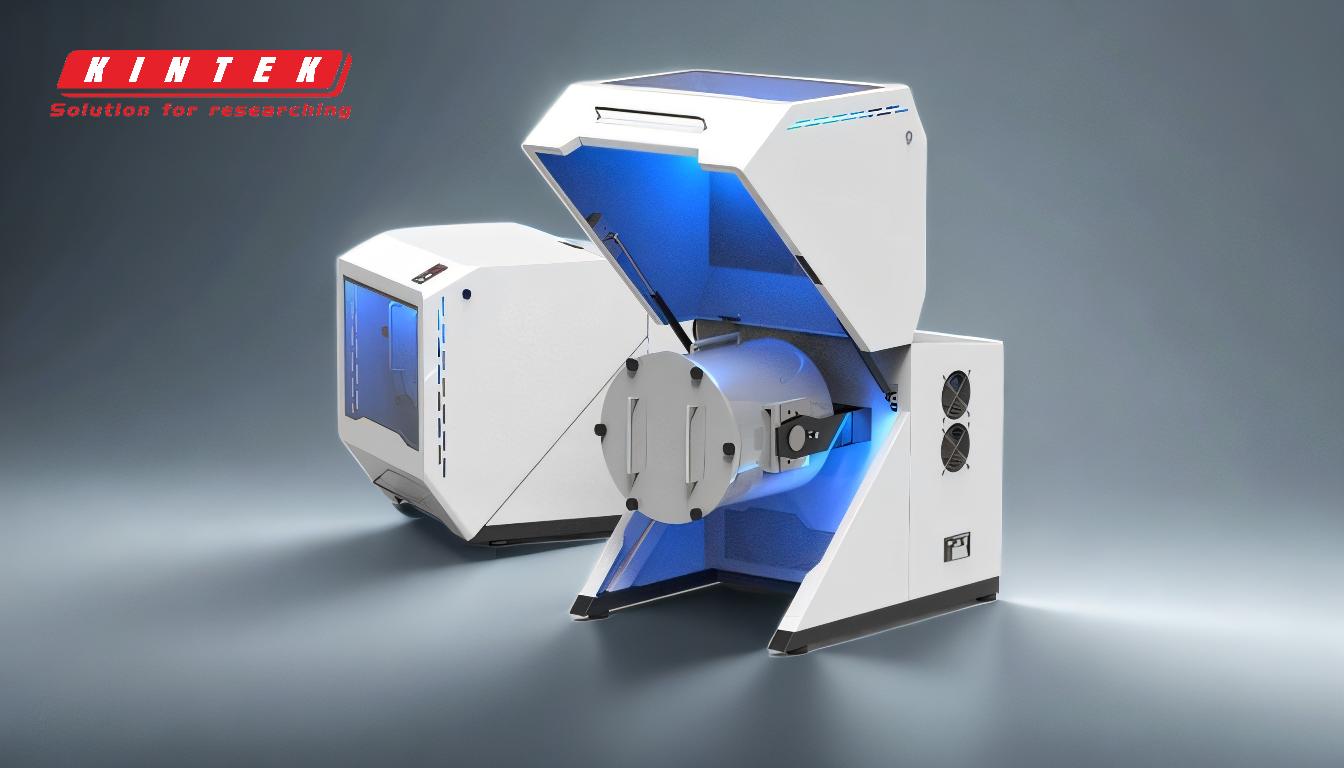
-
Rotor and Stator:
- The rotor is a rapidly rotating cone that generates high shear forces.
- The stator is a static cone that works in tandem with the rotor to create a narrow gap for material processing.
- Together, they form the core mechanism for particle size reduction and homogenization.
-
Housing:
- The housing encloses the rotor and stator, ensuring safety and preventing material leakage.
- It is typically made from stainless steel (e.g., SS 316) to ensure durability and compliance with hygiene standards.
-
Drive System:
- The drive system powers the rotor and can be configured in horizontal or vertical orientations.
- It is designed for efficiency and ease of operation, with options for different power requirements.
-
Adjustment Mechanism:
- This mechanism allows for precise adjustment of the gap between the rotor and stator.
- It ensures optimal processing conditions for different materials and desired particle sizes.
-
Optional Overload Pressure Release Mechanism:
- This feature protects the machine from damage due to excessive pressure or material overload.
- It enhances the longevity and reliability of the colloid mill.
-
Materials and Compliance:
- Contact parts are made from stainless steel (SS 316) for corrosion resistance and hygiene.
- Moving parts are covered with stainless steel (SS 304) for durability.
- Food-grade seals prevent contamination, making the mill suitable for food and pharmaceutical applications.
- The mill complies with cGMP standards, ensuring it meets regulatory requirements.
-
Mobility and Footprint:
- The colloid mill is compact, with a small footprint, making it suitable for facilities with limited space.
- Castor wheels are often included for easy mobility and repositioning.
-
Ease of Use and Maintenance:
- The design prioritizes user-friendliness, with simple controls and minimal maintenance requirements.
- This reduces downtime and operational costs, making it a cost-effective solution for various industries.
By understanding these components, a purchaser can evaluate the suitability of a colloid mill for their specific needs, ensuring optimal performance and compliance with industry standards.
Summary Table:
Component | Description |
---|---|
Rotor and Stator | Core mechanism for particle size reduction and homogenization. |
Housing | Stainless steel enclosure for safety and hygiene compliance. |
Drive System | Powers the rotor; available in horizontal or vertical configurations. |
Adjustment Mechanism | Allows precise gap adjustment for optimal material processing. |
Overload Pressure Release | Protects the machine from damage due to excessive pressure. |
Materials | SS 316 for contact parts, SS 304 for moving parts, and food-grade seals. |
Mobility | Compact design with castor wheels for easy repositioning. |
Ease of Use | User-friendly controls and minimal maintenance requirements. |
Ready to optimize your material processing? Contact us today to find the perfect colloid mill for your needs!