Pyrolysis oil is a complex mixture derived from the thermal decomposition of biomass. It primarily consists of oxygenated organic compounds, polymers, and water, with a high aromatic content and some aliphatic hydrocarbons. The oil contains up to 40% oxygen by weight, making it significantly different from petroleum products. Its components range from low molecular weight compounds like formaldehyde and acetic acid to high molecular weight phenols, anhydrosugars, and oligosaccharides. The oil is dark brown, corrosive, thermally unstable, and has a distinctive smoky odor. It is also prone to polymerization and viscosity changes over time.
Key Points Explained:
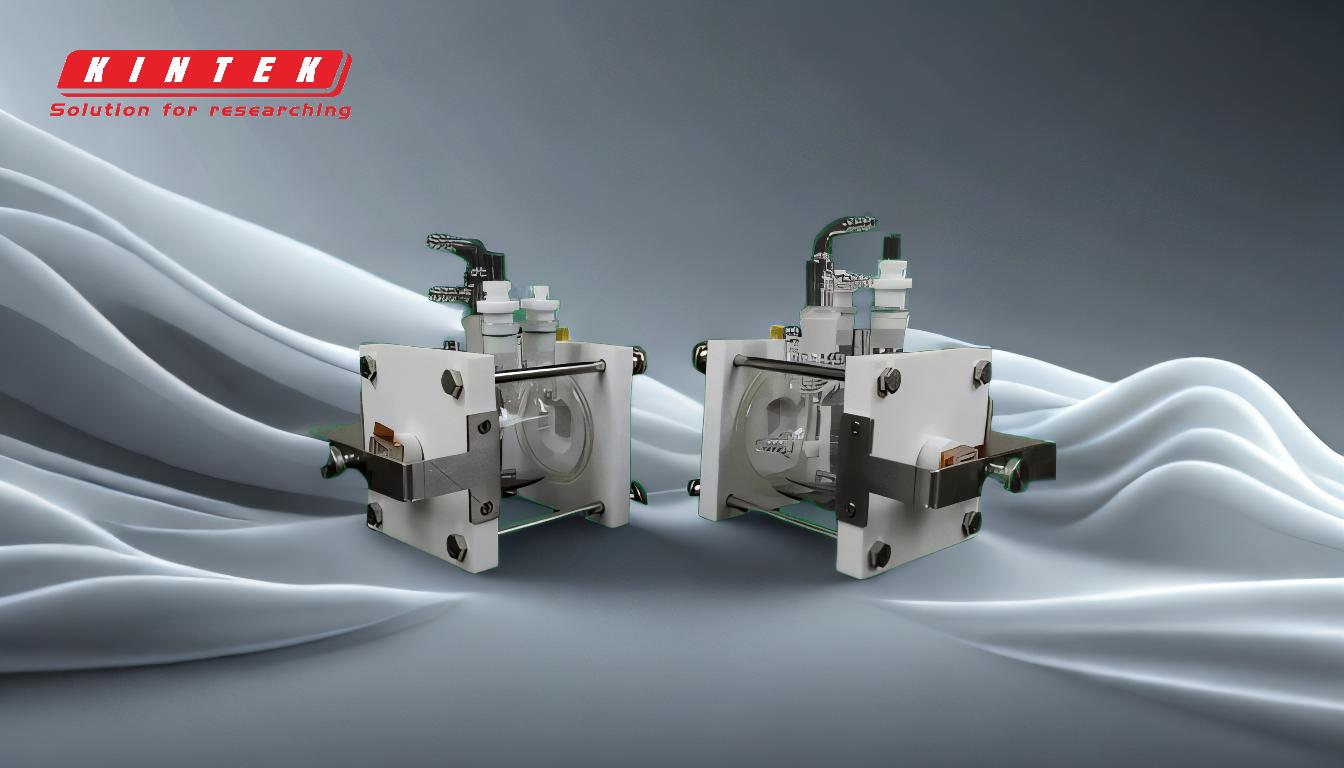
-
Primary Composition of Pyrolysis Oil:
- Pyrolysis oil is a complex mixture of oxygenated organic compounds, polymers, and water.
- It contains up to 40% oxygen by weight, which is a defining characteristic.
- The oil is composed of both low and high molecular weight compounds, including:
- Low molecular weight compounds: Formaldehyde, acetic acid, and other simple organic molecules.
- High molecular weight compounds: Phenols, anhydrosugars, and oligosaccharides.
-
Aromatic and Aliphatic Content:
- The oil has a high aromatic content, which contributes to its chemical complexity.
- It also contains some aliphatic hydrocarbons, which are simpler in structure compared to aromatic compounds.
-
Physical and Chemical Properties:
- Color and Odor: Pyrolysis oil is dark brown and has a distinctive acrid, smoky smell.
- Corrosiveness: The oil is corrosive, which can cause irritation or health issues upon exposure.
- Thermal Instability: It is thermally unstable and prone to polymerization when exposed to air.
- Viscosity Changes: Over time, the oil's viscosity increases due to condensation reactions, making it unstable and difficult to handle.
-
Water Content:
- Pyrolysis oil contains a significant proportion of water, typically between 20-30 wt-%.
- This high water content contributes to its immiscibility with fossil fuels and its non-volatile nature.
-
Differentiation from Petroleum Products:
- The high oxygen content and the presence of water make pyrolysis oil significantly different from petroleum products.
- It is non-volatile, immiscible with fossil fuels, and thermally unstable, which limits its direct use as a fuel.
-
Health and Safety Concerns:
- The corrosive nature and potential for irritation or health issues make handling pyrolysis oil a safety concern.
- Proper storage and handling procedures are necessary to mitigate these risks.
-
Applications and Challenges:
- Despite its complex composition, pyrolysis oil has potential applications in biofuels and chemical production.
- However, its instability and corrosive nature present significant challenges for its use and storage.
In summary, pyrolysis oil is a complex and chemically diverse mixture with a high oxygen content, significant water proportion, and a range of low to high molecular weight compounds. Its properties, including corrosiveness, thermal instability, and viscosity changes, make it distinct from traditional petroleum products and necessitate careful handling and processing.
Summary Table:
Aspect | Details |
---|---|
Primary Composition | Oxygenated organic compounds, polymers, water (up to 40% oxygen by weight). |
Molecular Weight Range | Low (formaldehyde, acetic acid) to high (phenols, anhydrosugars). |
Aromatic Content | High, contributing to chemical complexity. |
Physical Properties | Dark brown, smoky odor, corrosive, thermally unstable. |
Water Content | 20-30 wt-%, immiscible with fossil fuels. |
Health Concerns | Corrosive, requires careful handling. |
Applications | Biofuels, chemical production (with challenges). |
Learn more about pyrolysis oil and its applications—contact our experts today!