Hot isostatic pressing (HIP) is a manufacturing process that uses high temperature and isostatic gas pressure to eliminate porosity and increase the density of materials such as metals, ceramics, polymers, and composites. The process involves placing the material in a sealed container, which is then subjected to uniform pressure (up to 300 MPa) and high temperatures (up to 2000°C) using an inert gas like argon. This combination of pressure and temperature allows the material to flow in the solid state, bonding at an atomic level and eliminating internal voids. The process is controlled by computers to ensure precise temperature, pressure, and time parameters, resulting in fully dense, defect-free materials.
Key Points Explained:
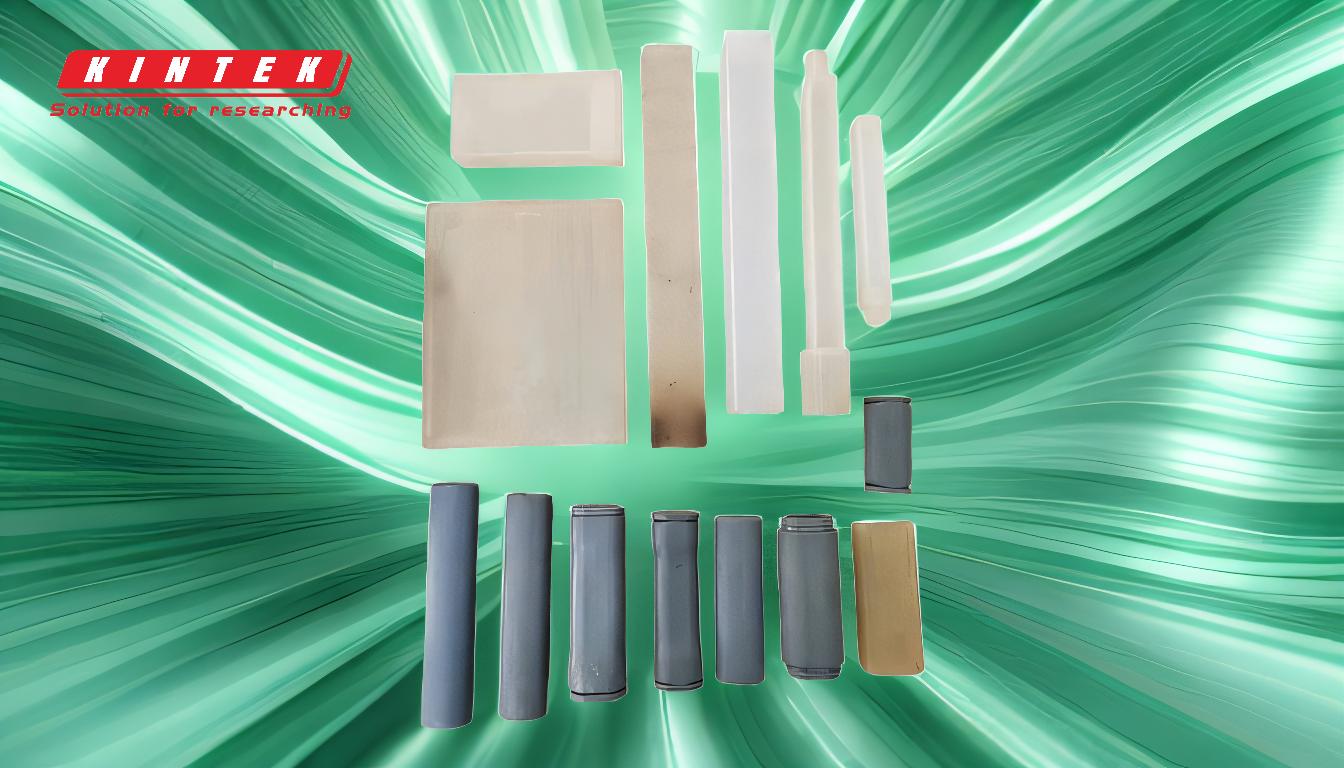
-
Pressure and Temperature Conditions:
- Pressure: The process applies hydrostatic pressure, typically ranging from 100 to 300 MPa, using an inert gas like argon or nitrogen. This pressure is applied uniformly in all directions, ensuring that the material is compressed evenly without distortion.
- Temperature: The temperature during HIP can range from 1000°C to 2200°C, depending on the material being processed. This high temperature facilitates the sintering and densification of the material.
-
Inert Gas as Pressure Medium:
- An inert gas, such as argon, is used as the pressure transfer medium. This gas is chemically unreactive, preventing any unwanted chemical reactions with the material being processed. The gas ensures that the pressure is applied uniformly across the surface of the material.
-
Material Preparation:
- Before HIP, the material (often in powder form) is placed into a metallic or glass container, known as a "can." This container is out-gassed to remove any air or moisture and then sealed to maintain the integrity of the environment during the HIP process.
-
Densification Mechanisms:
- Plastic Deformation: Initially, the high pressure causes plastic deformation, collapsing any voids or pores in the material.
- Creep and Diffusion: As the process continues, creep and diffusion mechanisms take over, further densifying the material and eliminating any remaining pores. This results in a fully dense, defect-free material.
-
Process Control:
- The HIP process is controlled by computers, which program the equipment to achieve the desired results. This includes controlling the temperature ramp-up, pressure application, and the duration of the process. The precise control ensures consistent and high-quality results.
-
Applications:
- HIP is used in various industries to improve the mechanical properties of materials. It is commonly used for sintering and densifying products, joining different parts and materials, and eliminating porosity in metals, ceramics, polymers, and composites.
-
Equipment:
- HIP equipment comes in various sizes and configurations, with chambers that can be loaded from the top or bottom. The equipment is designed to handle the high pressures and temperatures required for the process, and it ensures that the pressure is applied uniformly to the material without altering its shape.
-
Benefits:
- The HIP process results in materials with improved mechanical properties, such as increased strength, fatigue resistance, and durability. It also allows for the production of complex shapes and the joining of dissimilar materials, making it a versatile and valuable manufacturing technique.
By understanding these key points, one can appreciate the critical conditions and mechanisms involved in hot isostatic pressing, making it a powerful tool for material densification and enhancement.
Summary Table:
Key Aspect | Details |
---|---|
Pressure | 100–300 MPa, applied uniformly using inert gases like argon or nitrogen. |
Temperature | 1000°C to 2200°C, depending on the material. |
Inert Gas | Argon or nitrogen ensures uniform pressure and prevents chemical reactions. |
Material Preparation | Powdered material is placed in a sealed, out-gassed container ("can"). |
Densification Mechanisms | Plastic deformation, creep, and diffusion eliminate voids and pores. |
Process Control | Computer-controlled for precise temperature, pressure, and time settings. |
Applications | Used in metals, ceramics, polymers, and composites for sintering and joining. |
Benefits | Increased strength, fatigue resistance, and production of complex shapes. |
Discover how hot isostatic pressing can transform your materials—contact our experts today!