Grinding mills are essential equipment in various industries, used to break down materials into smaller particles or powders. They come in different types, each designed for specific applications, materials, and operational requirements. The choice of grinding mill depends on factors such as the material's hardness, desired particle size, and production capacity. Common types include ball mills, rod mills, SAG mills, and vertical roller mills, each offering unique advantages and limitations. Understanding the differences between these mills is crucial for selecting the right equipment for your needs.
Key Points Explained:
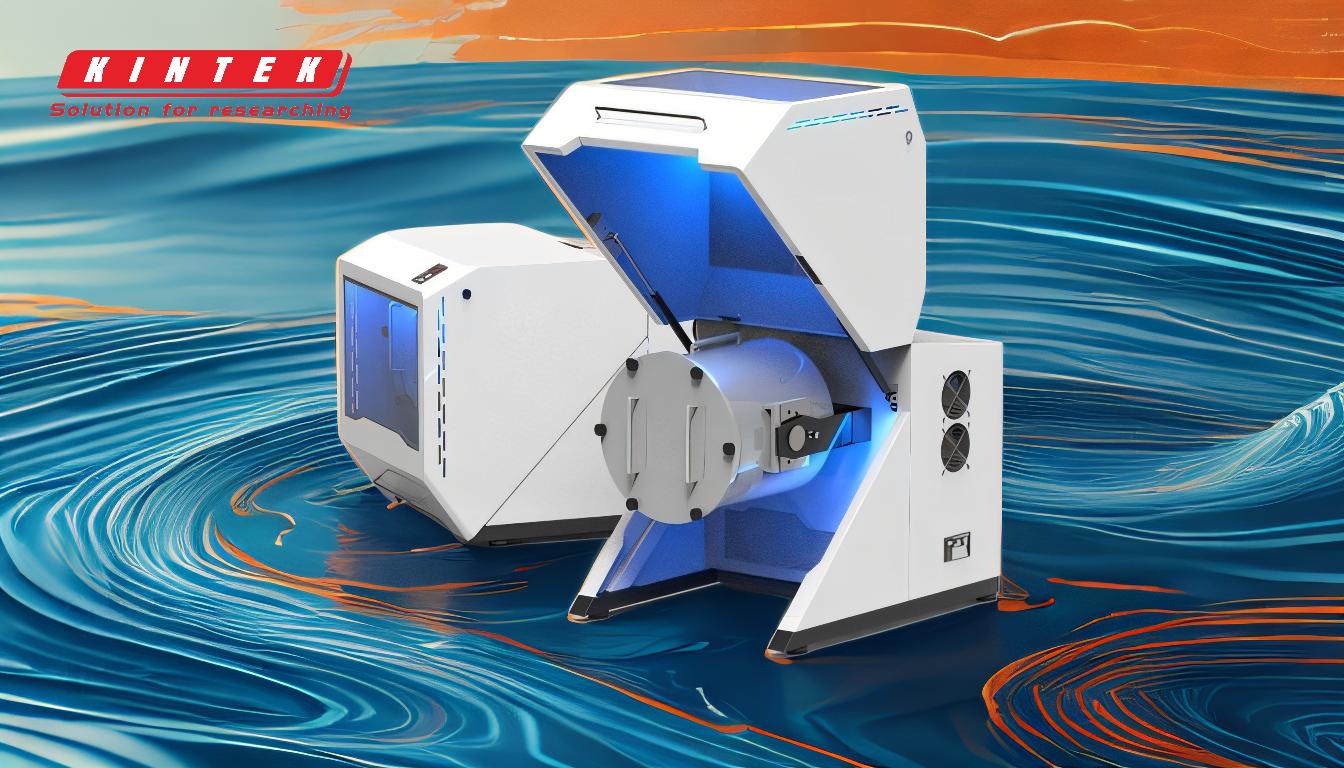
-
Ball Mills
- Description: Ball mills are cylindrical devices that rotate around a horizontal axis and are partially filled with grinding media (usually steel or ceramic balls).
- Working Principle: The material is fed into the mill and crushed by the impact and attrition of the grinding media as the mill rotates.
- Applications: Widely used in mining, cement, and chemical industries for grinding ores, clinker, and other materials.
-
Advantages:
- Capable of producing fine and ultra-fine powders.
- Suitable for both wet and dry grinding processes.
-
Limitations:
- High energy consumption.
- Requires regular maintenance due to wear and tear of grinding media.
-
Rod Mills
- Description: Rod mills are similar to ball mills but use long steel rods as grinding media instead of balls.
- Working Principle: The rods tumble and grind the material by rolling and sliding within the mill.
- Applications: Commonly used in the mining industry for grinding ores and minerals.
-
Advantages:
- Produces a more uniform particle size compared to ball mills.
- Less prone to over-grinding.
-
Limitations:
- Limited to coarse grinding applications.
- Not suitable for fine or ultra-fine grinding.
-
SAG Mills (Semi-Autogenous Grinding Mills)
- Description: SAG mills are large grinding mills that use a combination of ore and grinding media (typically large rocks or steel balls) to break down materials.
- Working Principle: The ore is crushed by the impact of the grinding media and the grinding action between the particles.
- Applications: Primarily used in the mining industry for grinding large volumes of ore.
-
Advantages:
- High throughput and efficiency.
- Reduces the need for secondary grinding stages.
-
Limitations:
- High capital and operational costs.
- Requires a large footprint and significant energy input.
-
Vertical Roller Mills (VRM)
- Description: VRMs are advanced grinding mills that use rollers to crush and grind materials against a rotating table.
- Working Principle: The material is fed onto the rotating table and crushed by the rollers, which apply pressure and shear forces.
- Applications: Commonly used in the cement and power industries for grinding raw materials, coal, and clinker.
-
Advantages:
- High energy efficiency compared to traditional ball mills.
- Compact design and lower noise levels.
-
Limitations:
- Complex maintenance and operation.
- Limited to specific materials and applications.
-
Hammer Mills
- Description: Hammer mills use rotating hammers to crush and grind materials.
- Working Principle: The material is fed into the mill and struck by the hammers, which pulverize it into smaller particles.
- Applications: Used in agriculture, food processing, and recycling industries for grinding grains, biomass, and waste materials.
-
Advantages:
- Simple design and easy to operate.
- Suitable for a wide range of materials.
-
Limitations:
- Produces a wide range of particle sizes.
- High wear and tear on hammers and screens.
-
Attrition Mills
- Description: Attrition mills use a series of rotating disks or plates to grind materials through friction and shear forces.
- Working Principle: The material is fed between the rotating disks, where it is ground by the rubbing action.
- Applications: Used in the chemical, food, and pharmaceutical industries for fine grinding and mixing.
-
Advantages:
- Produces very fine and uniform particles.
- Suitable for heat-sensitive materials.
-
Limitations:
- Limited to small-scale operations.
- High maintenance due to wear of grinding disks.
-
Jet Mills
- Description: Jet mills use high-speed jets of compressed air or gas to grind materials through particle-on-particle impact.
- Working Principle: The material is fed into a chamber where it is accelerated by the jets and collides with other particles, resulting in size reduction.
- Applications: Used in the pharmaceutical, chemical, and food industries for ultra-fine grinding.
-
Advantages:
- Produces extremely fine particles with narrow size distribution.
- No moving parts, reducing wear and maintenance.
-
Limitations:
- High energy consumption.
- Limited to dry grinding applications.
-
Planetary Ball Mills
- Description: Planetary ball mills are smaller, high-energy mills that use multiple grinding jars rotating around a central axis.
- Working Principle: The grinding jars rotate in opposite directions, creating high-energy impacts that grind the material.
- Applications: Used in laboratories and small-scale production for grinding and mixing materials.
-
Advantages:
- High grinding efficiency and speed.
- Suitable for a wide range of materials, including hard and brittle substances.
-
Limitations:
- Limited capacity for large-scale production.
- High wear and tear on grinding jars and balls.
By understanding the different types of grinding mills and their specific applications, you can make an informed decision when selecting the right equipment for your needs. Each type of mill has its own set of advantages and limitations, so it's important to consider factors such as material properties, desired particle size, and production capacity when making your choice.
Summary Table:
Type of Mill | Applications | Advantages | Limitations |
---|---|---|---|
Ball Mills | Mining, cement, chemical industries | Produces fine/ultra-fine powders; suitable for wet/dry grinding | High energy consumption; requires regular maintenance |
Rod Mills | Mining industry | Uniform particle size; less prone to over-grinding | Limited to coarse grinding; not suitable for fine/ultra-fine grinding |
SAG Mills | Mining industry | High throughput; reduces need for secondary grinding | High capital/operational costs; large footprint and energy input |
Vertical Roller Mills | Cement, power industries | Energy-efficient; compact design; lower noise levels | Complex maintenance; limited to specific materials |
Hammer Mills | Agriculture, food processing, recycling | Simple design; suitable for a wide range of materials | Wide particle size range; high wear on hammers/screens |
Attrition Mills | Chemical, food, pharmaceutical industries | Produces fine/uniform particles; suitable for heat-sensitive materials | Limited to small-scale operations; high maintenance |
Jet Mills | Pharmaceutical, chemical, food industries | Produces ultra-fine particles; no moving parts | High energy consumption; limited to dry grinding |
Planetary Ball Mills | Laboratories, small-scale production | High grinding efficiency; suitable for hard/brittle materials | Limited capacity for large-scale production; high wear on jars/balls |
Need help selecting the right grinding mill for your application? Contact our experts today for personalized advice!