Milling in the pharmaceutical industry is a critical process used to reduce particle size, improve dissolution rates, and ensure uniformity in drug formulations. The choice of milling technique depends on the material properties, desired particle size, and the specific application. Common types of milling include impact milling, shear milling, and compression milling, each with unique mechanisms and applications. Understanding these methods helps pharmaceutical manufacturers optimize drug performance, ensure regulatory compliance, and achieve consistent product quality.
Key Points Explained:
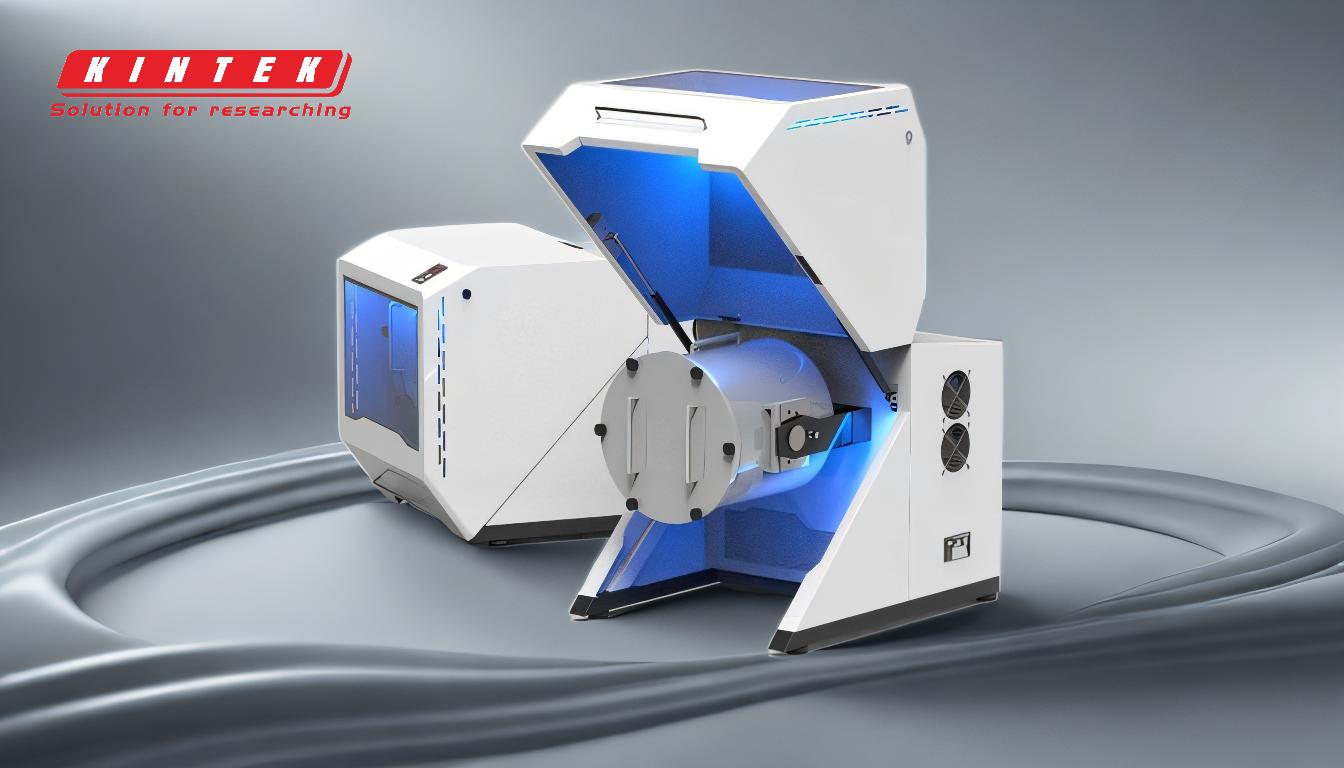
-
Impact Milling:
- Mechanism: Impact milling involves the collision of particles with a high-speed rotor or hammer, breaking them into smaller sizes through impact forces.
- Applications: Ideal for brittle materials and coarse grinding, often used in the initial stages of particle size reduction.
- Equipment: Hammer mills and pin mills are commonly used for impact milling.
- Advantages: High throughput, efficient for coarse grinding, and suitable for heat-sensitive materials due to minimal heat generation.
- Limitations: May produce a wide particle size distribution and is less effective for fine grinding.
-
Shear Milling:
- Mechanism: Shear milling relies on cutting or shearing forces to break down particles, often using blades or rotating discs.
- Applications: Suitable for fibrous or tough materials, and for achieving finer particle sizes compared to impact milling.
- Equipment: Knife mills and cutting mills are typical examples.
- Advantages: Effective for materials that are difficult to grind using impact methods, and can produce a narrower particle size distribution.
- Limitations: May generate heat, which can be problematic for heat-sensitive materials.
-
Compression Milling:
- Mechanism: Compression milling involves applying pressure to particles, causing them to fracture or deform under compressive forces.
- Applications: Often used for hard, brittle materials and for achieving very fine particle sizes.
- Equipment: Roller mills and ball mills are commonly used for compression milling.
- Advantages: Produces uniform particle sizes and is effective for fine grinding.
- Limitations: Can be energy-intensive and may generate heat, requiring cooling mechanisms.
-
Other Milling Techniques:
- Jet Milling: Uses high-speed jets of air or gas to collide particles, resulting in fine and ultra-fine particles. Suitable for heat-sensitive materials and achieving micron-sized particles.
- Cryogenic Milling: Involves cooling materials to very low temperatures (using liquid nitrogen) before milling, making brittle materials easier to grind. Ideal for heat-sensitive or elastic materials.
- Wet Milling: Uses a liquid medium to aid in particle size reduction, often employed for materials that are difficult to grind in dry conditions.
-
Selection Criteria for Milling Techniques:
- Material Properties: Consider hardness, brittleness, and thermal sensitivity of the material.
- Desired Particle Size: Choose a method that can achieve the required particle size distribution.
- Scale of Operation: Ensure the equipment can handle the required throughput.
- Regulatory Compliance: Verify that the milling process meets pharmaceutical standards for quality and safety.
-
Importance of Milling in Pharma:
- Enhanced Dissolution Rates: Smaller particle sizes increase the surface area, improving the dissolution rate of active pharmaceutical ingredients (APIs).
- Uniformity: Ensures consistent drug performance and dosage accuracy.
- Process Efficiency: Optimizes downstream processes such as blending, granulation, and tablet compression.
- Regulatory Compliance: Adherence to particle size specifications is critical for meeting regulatory standards.
By understanding the different types of milling and their applications, pharmaceutical manufacturers can select the most appropriate method for their specific needs, ensuring optimal drug performance and regulatory compliance.
Summary Table:
Milling Technique | Mechanism | Applications | Equipment | Advantages | Limitations |
---|---|---|---|---|---|
Impact Milling | Collision of particles with a high-speed rotor | Brittle materials, coarse grinding | Hammer mills, pin mills | High throughput, minimal heat generation | Wide particle size distribution |
Shear Milling | Cutting or shearing forces | Fibrous or tough materials, finer grinding | Knife mills, cutting mills | Narrow particle size distribution | Heat generation |
Compression Milling | Pressure to fracture particles | Hard, brittle materials, fine grinding | Roller mills, ball mills | Uniform particle sizes | Energy-intensive, heat generation |
Jet Milling | High-speed air/gas collisions | Heat-sensitive materials, micron-sized particles | Jet mills | Fine and ultra-fine particles | Requires specialized equipment |
Cryogenic Milling | Cooling with liquid nitrogen | Heat-sensitive or elastic materials | Cryogenic mills | Ideal for brittle materials | Requires cooling mechanisms |
Wet Milling | Liquid medium for particle reduction | Difficult-to-grind materials | Wet mills | Effective for specific materials | Requires liquid handling |
Need help selecting the right milling technique for your pharmaceutical needs? Contact our experts today for tailored solutions!