Plastic pyrolysis is a process that converts plastic waste into valuable products like pyrolysis oil, gas, and char. The type of reactor used in this process plays a critical role in determining the efficiency, scalability, and suitability for specific types of plastics. Common reactors include fluidized bed reactors, fixed bed reactors, and cyclone reactors, each designed for different pyrolysis processes such as fast or slow pyrolysis. These reactors are constructed from high-temperature-resistant materials like Q245R and Q345R steel, ensuring durability and heat transfer efficiency. The choice of reactor depends on factors like feedstock type, desired products, and process requirements.
Key Points Explained:
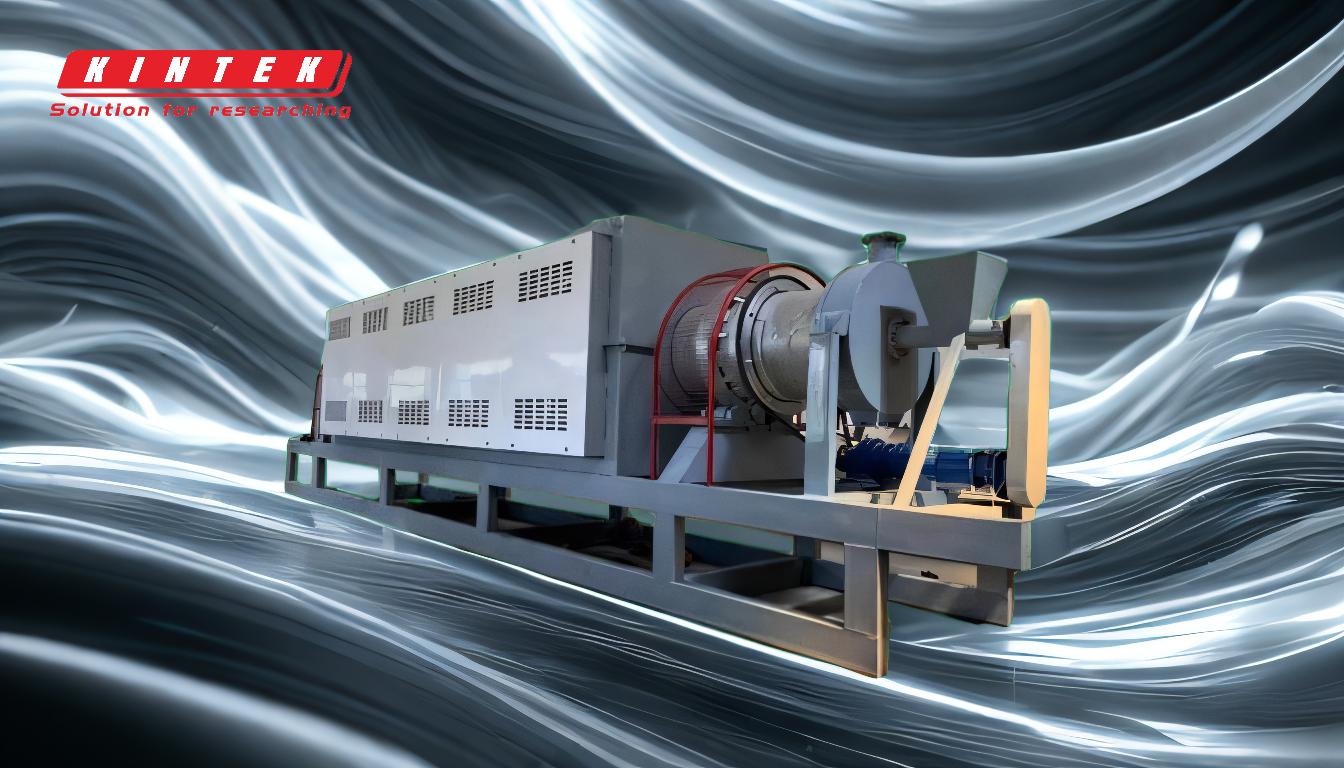
-
Types of Reactors in Plastic Pyrolysis:
-
Fluidized Bed Reactors:
- These reactors suspend plastic particles in a gas or liquid, ensuring even heating and efficient heat transfer.
- They are ideal for fast pyrolysis due to their ability to handle high heating rates and short residence times.
- Subtypes include bubbling fluidized bed pyrolyzers and circulating fluid beds, which offer enhanced control over heat transfer and feedstock handling.
-
Fixed Bed Reactors:
- These reactors use a stationary bed of material, making them suitable for slow pyrolysis processes.
- They are simpler in design and operation but may have limitations in heat transfer efficiency and scalability.
-
Cyclone Reactors:
- These reactors utilize centrifugal forces to separate and process materials, making them effective for handling fine particles and ensuring high throughput.
- They are often used in conjunction with other reactor types to improve overall system efficiency.
-
Fluidized Bed Reactors:
-
Material Suitability:
- Pyrolysis reactors can process a wide range of plastics, including HDPE, LDPE, PP, PS, and PC.
- However, plastics like PVC and PET are not suitable due to their chemical composition, which can release harmful gases like chlorine during pyrolysis.
-
Construction and Durability:
- Reactors are typically made of high-temperature-resistant materials such as Q245R and Q345R steel.
- These materials ensure a service life of 5-8 years and maintain heat transfer efficiency, even under extreme conditions.
-
Process Steps in Plastic Pyrolysis:
- The process begins with plastic waste shredding and drying, followed by preprocessing to remove non-plastic contaminants.
- The pyrolysis step involves heating the plastic in the reactor to break it down into oil, gas, and char.
- Post-pyrolysis steps include distillation and purification of the pyrolysis oil, followed by storage and dispatch.
-
Advantages of Different Reactor Types:
- Fluidized Bed Reactors: High heat transfer efficiency, short residence time, and suitability for fast pyrolysis.
- Fixed Bed Reactors: Simplicity in design and operation, ideal for slow pyrolysis.
- Cyclone Reactors: Effective for handling fine particles and improving system throughput.
By understanding the different types of reactors and their specific applications, equipment purchasers can make informed decisions to optimize their plastic pyrolysis processes.
Summary Table:
Reactor Type | Key Features | Best For |
---|---|---|
Fluidized Bed | High heat transfer, short residence time, handles high heating rates | Fast pyrolysis |
Fixed Bed | Simple design, stationary bed, easy operation | Slow pyrolysis |
Cyclone | Centrifugal force, handles fine particles, high throughput | Fine particle processing |
Ready to optimize your plastic pyrolysis process? Contact our experts today for tailored solutions!