Sieve shakers, while efficient and widely used for particle size analysis, have several notable disadvantages. These include limitations in accuracy for fine materials, assumptions about particle shape, unreliable results for non-spherical particles, and challenges with very small particles. Additionally, sieves can become clogged or distorted, and the method itself is time-consuming and limited in resolution. Understanding these drawbacks is crucial for equipment and consumable purchasers to make informed decisions and ensure proper handling and maintenance of sieve shakers.
Key Points Explained:
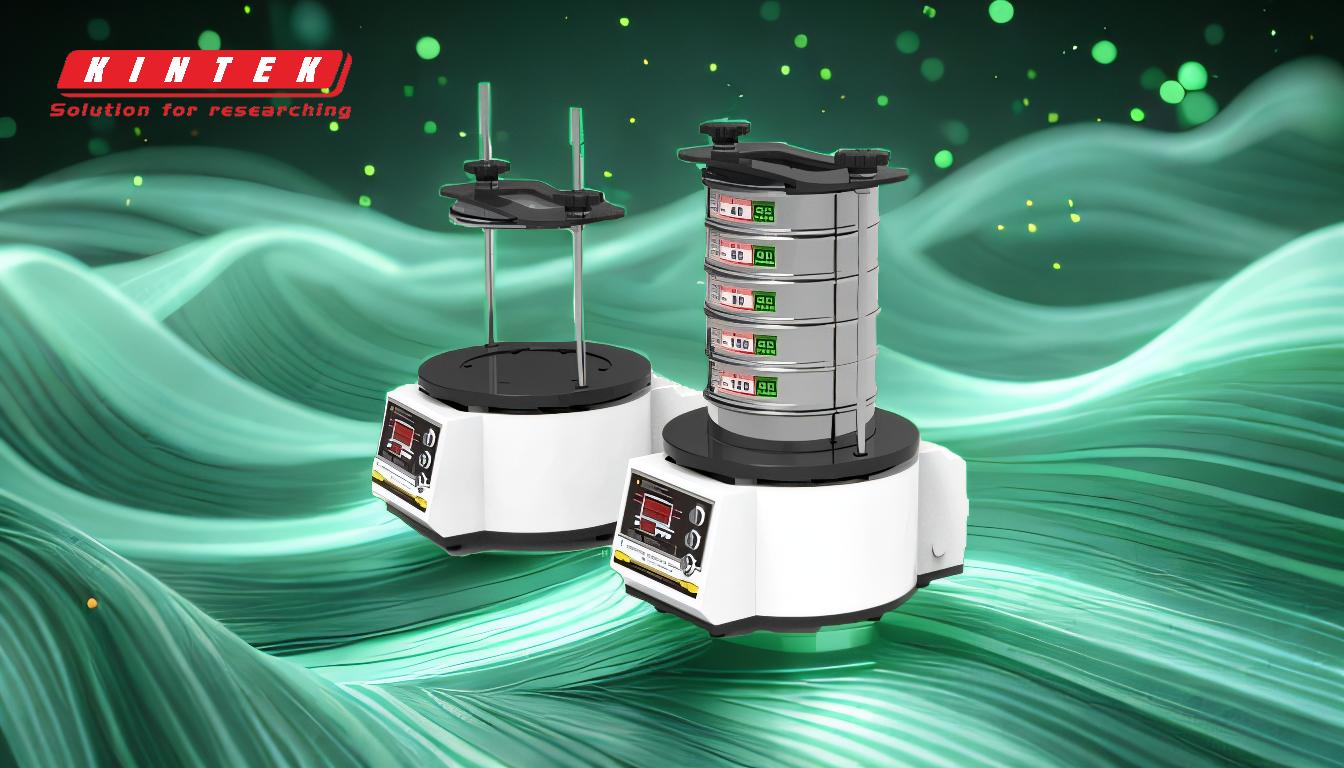
-
Reduced Accuracy for Fine Materials:
- Sieve shakers are less accurate for materials finer than 100 mesh. This is because finer particles can pass through the mesh more easily, leading to less precise measurements.
- For purchasers, this means that sieve shakers may not be suitable for applications requiring high precision with very fine particles.
-
Assumption of Particle Shape:
- The method assumes that all particles are round or nearly spherical. However, many materials consist of elongated or flat particles, which can lead to inaccurate mass-based results.
- This limitation is significant for industries dealing with non-spherical particles, as it may necessitate the use of alternative analysis methods.
-
Unreliable Results for Non-Spherical Particles:
- Elongated and flat particles can behave differently during sieving, leading to unreliable mass-based results. This can affect the overall accuracy of the particle size distribution analysis.
- Purchasers should consider the nature of the materials they are analyzing and whether a sieve shaker is the most appropriate tool.
-
Unsuitability for Very Small Particles:
- Sieve shakers are unsuitable for particles smaller than 50 µm. For such fine particles, other methods like laser diffraction or sedimentation may be more appropriate.
- This limitation is crucial for industries dealing with nanomaterials or very fine powders, where alternative techniques might be necessary.
-
Potential Reduction in Particle Size:
- The sieving process can cause further reduction in particle size, leading to errors in the analysis. This is particularly problematic for friable materials that can break down during shaking.
- Purchasers should be aware of this potential issue, especially when dealing with fragile or easily degradable materials.
-
Risk of Sieve Clogging and Distortion:
- Sieves can become clogged or distorted if not properly handled and maintained. Clogging can reduce the efficiency of the sieving process, while distortion can lead to inaccurate results.
- Regular maintenance and proper handling are essential to mitigate these risks, which adds to the operational costs and effort required.
-
Limited Number of Size Fractions:
- Sieve analysis typically provides a limited number of size fractions, usually up to 8 sieves. This restricts the resolution of the particle size distribution and may not provide sufficient detail for some applications.
- For purchasers needing detailed particle size analysis, this limitation might necessitate the use of additional or alternative methods.
-
Time-Consuming Process:
- Sieve analysis can be a time-consuming process, especially when dealing with large sample sizes or multiple sieves. This can impact the overall efficiency of the analysis.
- Purchasers should consider the time requirements and whether the sieve shaker can meet their throughput needs.
-
Variations in Mesh Weave:
- Variations in the weave of the mesh material can affect the reproducibility of test results. These variations need to be accounted for in data presentation and analysis.
- This highlights the importance of using high-quality sieves and ensuring consistency in the sieving process to achieve reliable results.
-
Dry Particle Limitation:
- Sieve analysis is only effective with dry particles. Wet or moist materials can clog the sieves and affect the accuracy of the results.
- This limitation is significant for industries dealing with wet materials, as it may require additional sample preparation or alternative analysis methods.
In conclusion, while sieve shakers offer significant advantages in terms of efficiency and automation, they come with several limitations that need to be carefully considered. Purchasers should evaluate these disadvantages in the context of their specific applications and material characteristics to ensure they select the most appropriate particle size analysis method. Proper handling, maintenance, and awareness of the method's limitations are essential to achieve accurate and reliable results.
Summary Table:
Disadvantage | Key Details |
---|---|
Reduced Accuracy for Fine Materials | Less precise for particles finer than 100 mesh; unsuitable for high precision. |
Assumption of Particle Shape | Assumes round/spherical particles; unreliable for elongated or flat particles. |
Unreliable for Non-Spherical Particles | Mass-based results skewed for non-spherical particles. |
Unsuitable for Very Small Particles | Ineffective for particles smaller than 50 µm; alternatives like laser diffraction recommended. |
Potential Particle Size Reduction | Sieving may further reduce particle size, affecting analysis accuracy. |
Risk of Sieve Clogging and Distortion | Requires regular maintenance; clogging and distortion can lead to inaccuracies. |
Limited Number of Size Fractions | Typically up to 8 sieves; restricts resolution for detailed analysis. |
Time-Consuming Process | Lengthy process for large samples or multiple sieves. |
Variations in Mesh Weave | Affects reproducibility; requires high-quality sieves for consistency. |
Dry Particle Limitation | Only effective for dry particles; wet materials clog sieves. |
Need help choosing the right particle size analysis method? Contact our experts today for personalized advice!