Vibro sifters, while widely used in various industries for particle separation and classification, come with several disadvantages that can impact their efficiency, accuracy, and suitability for certain applications. These include noise production during operation, limited screening accuracy and capacity, potential material contamination, and challenges with handling fine or irregularly shaped particles. Understanding these drawbacks is crucial for equipment or consumable purchasers to make informed decisions based on their specific needs and operational constraints.
Key Points Explained:
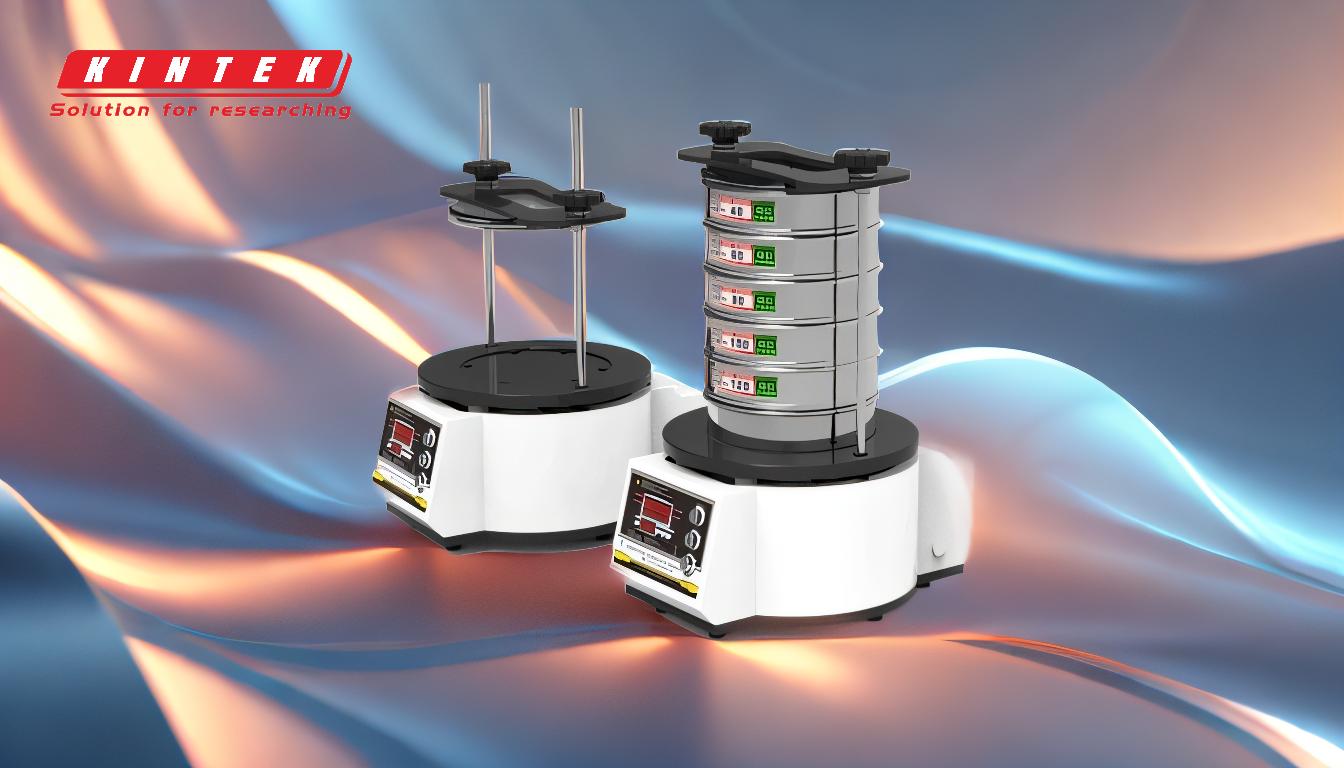
-
Noise Production During Operation
- Vibro sifters generate significant noise due to the mechanical vibrations required for their operation.
- This noise can create an uncomfortable working environment for staff and may require additional soundproofing measures or personal protective equipment (PPE) to mitigate.
- In office or laboratory settings, the noise can disrupt other activities, making vibro sifters less suitable for quiet environments.
-
Limited Screening Accuracy
- Vibro sifters are not ideal for materials requiring high precision in particle separation.
- The screening accuracy is limited by the design and vibration intensity, which may not effectively separate particles of very similar sizes.
- This limitation makes vibro sifters unsuitable for applications where precise particle size distribution is critical, such as in pharmaceutical or advanced material processing.
-
Limited Screening Capacity
- The capacity of a vibro sifter is influenced by its size and the manufacturing process.
- Larger equipment may offer higher capacity but can be impractical in settings with space constraints.
- For high-throughput applications, the limited capacity of vibro sifters may necessitate the use of multiple units, increasing costs and operational complexity.
-
Potential for Material Contamination
- The friction and vibration inherent in the operation of vibro sifters can lead to material contamination.
- This is particularly problematic for sensitive materials, such as food products or pharmaceuticals, where contamination can compromise product quality and safety.
- Regular maintenance and cleaning are required to minimize contamination risks, adding to operational costs.
-
Challenges with Fine or Irregularly Shaped Particles
- Vibro sifters are less effective for materials finer than 100 mesh or particles smaller than 50 µm.
- The assumption that particles are round or nearly spherical can lead to unreliable results for elongated or flat particles.
- Irregularly shaped particles may not pass through the sieve openings as expected, leading to inaccurate separation and potential clogging of the sieves.
-
Risk of Sieve Clogging and Distortion
- Improper handling or maintenance of sieves can result in clogging or distortion, reducing the efficiency and lifespan of the equipment.
- Clogging can occur when fine particles accumulate in the sieve openings, while distortion may result from excessive vibration or improper cleaning techniques.
- These issues necessitate regular inspection and replacement of sieves, adding to maintenance costs and downtime.
-
Further Reduction in Particle Size
- The intense vibrations of a vibro sifter can cause further reduction in particle size, particularly for brittle materials.
- This unintended size reduction can lead to errors in particle size distribution analysis and affect the quality of the final product.
- For applications requiring precise control over particle size, this drawback may render vibro sifters unsuitable.
In summary, while vibro sifters are versatile and widely used, their disadvantages—such as noise, limited accuracy and capacity, contamination risks, and challenges with fine or irregular particles—must be carefully considered. Purchasers should evaluate these factors against their specific operational requirements to determine whether a vibro sifter is the right choice for their application.
Summary Table:
Disadvantage | Key Details |
---|---|
Noise Production | High noise levels during operation, requiring soundproofing or PPE. |
Limited Screening Accuracy | Not suitable for high-precision particle separation. |
Limited Screening Capacity | Size and design constraints reduce throughput for high-volume applications. |
Material Contamination | Friction and vibration can lead to contamination of sensitive materials. |
Challenges with Fine/Irregular Particles | Less effective for particles finer than 100 mesh or irregular shapes. |
Sieve Clogging and Distortion | Requires regular maintenance to prevent clogging and distortion. |
Further Reduction in Particle Size | Vibrations may unintentionally reduce particle size, affecting product quality. |
Need help choosing the right equipment for your application? Contact our experts today for personalized advice!