Sputter deposition, while widely used in thin-film coating applications, has several notable disadvantages that can impact its efficiency, cost, and suitability for certain processes. These include challenges in film structuring, contamination risks, low sputtering rates, non-uniform deposition, high costs, and energy inefficiency. Additionally, controlling stoichiometry and managing reactive sputtering processes can be complex. Understanding these drawbacks is crucial for selecting the appropriate deposition method for specific applications.
Key Points Explained:
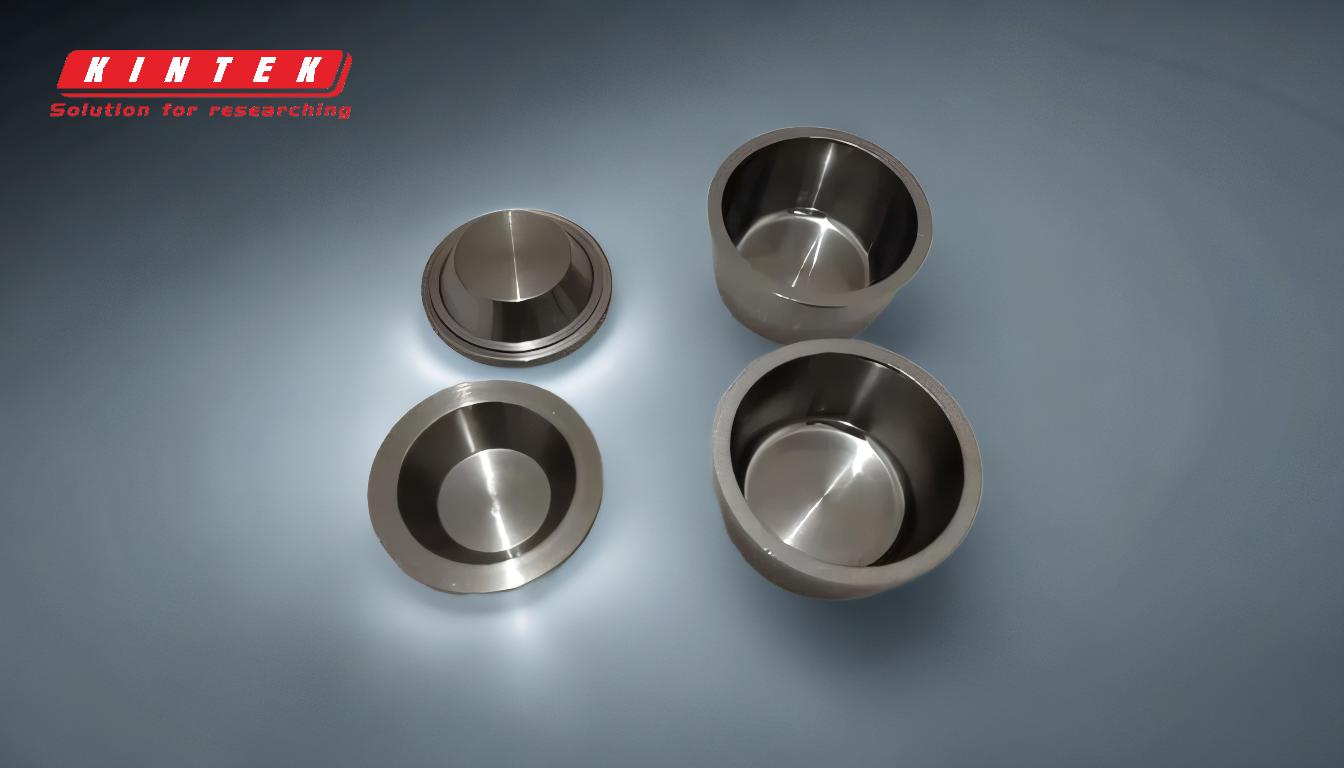
-
Difficulty in Combining with Lift-Off Processes:
- Sputter deposition is challenging to integrate with lift-off processes due to the diffuse transport of sputtered atoms. This makes full shadowing impossible, leading to potential contamination issues. The sidewall coverage and heating effects further complicate its use in liftoff applications, making it less desirable for such processes.
-
Contamination Risks:
- The sputtering process can introduce impurities from the source materials, leading to film contamination. Inert sputtering gases can also become impurities in the growing film. Additionally, gaseous contaminants can be activated in the plasma, increasing the risk of contamination.
-
Low Sputtering Rates:
- Sputter deposition typically has lower sputtering rates compared to thermal evaporation. This can result in slower deposition times, which may not be ideal for high-throughput applications.
-
Non-Uniform Deposition Flux:
- The deposition flux distribution in sputter deposition is often non-uniform. Achieving uniform film thickness requires the use of moving fixtures, which can add complexity and cost to the process.
-
Expensive Sputtering Targets:
- Sputtering targets are often expensive, and the material use can be inefficient. This contributes to higher overall costs, especially when using rare or specialized materials.
-
Energy Inefficiency:
- A significant portion of the energy incident on the target is converted into heat, which must be removed. This energy inefficiency can lead to increased operational costs and the need for effective cooling systems.
-
Challenges in Stoichiometry Control:
- Controlling the stoichiometry of the deposited film can be difficult, particularly in reactive sputter deposition. Precise control of gas composition is required to prevent target poisoning and achieve the desired film properties.
-
Complexity in Reactive Sputtering:
- Reactive sputter deposition involves additional complexities, such as the need to carefully control gas composition to avoid target poisoning. This can complicate the process and require more sophisticated equipment and monitoring.
-
Maintenance and Process Parameter Limitations:
- Sputtering is hindered by basic vacuum system realities, including limitations in process parameters and the need for user-supplied maintenance. This can increase the operational burden and require more frequent interventions to maintain process stability.
Understanding these disadvantages is essential for making informed decisions about the use of sputter deposition in various applications. While it offers several advantages, such as the ability to deposit a wide range of materials and achieve conformal coatings, the drawbacks must be carefully considered to ensure the chosen method aligns with the specific requirements of the application.
Summary Table:
Disadvantage | Description |
---|---|
Lift-Off Process Challenges | Difficult to integrate due to diffuse sputtered atom transport and contamination risks. |
Contamination Risks | Impurities from source materials and plasma-activated gaseous contaminants. |
Low Sputtering Rates | Slower deposition compared to thermal evaporation, impacting throughput. |
Non-Uniform Deposition | Requires moving fixtures for uniform film thickness, adding complexity and cost. |
Expensive Targets | High cost and inefficient use of sputtering targets, especially rare materials. |
Energy Inefficiency | Significant energy loss as heat, requiring effective cooling systems. |
Stoichiometry Control Issues | Difficult to control film composition, especially in reactive sputtering. |
Reactive Sputtering Complexity | Requires precise gas composition control to avoid target poisoning. |
Maintenance Challenges | Frequent user-supplied maintenance and process parameter limitations. |
Need help selecting the right deposition method for your application? Contact our experts today!