Ball mills are widely used in various industries for grinding and mixing materials, but they come with several drawbacks that can impact their efficiency, operational costs, and environmental footprint. These drawbacks include high energy consumption, significant wear and tear, noise pollution, and limitations in handling certain types of materials. Additionally, ball mills can be cumbersome due to their size and weight, and they may produce vibrations that affect their performance and the quality of the final product. Understanding these limitations is crucial for equipment and consumable purchasers to make informed decisions and optimize their operations.
Key Points Explained:
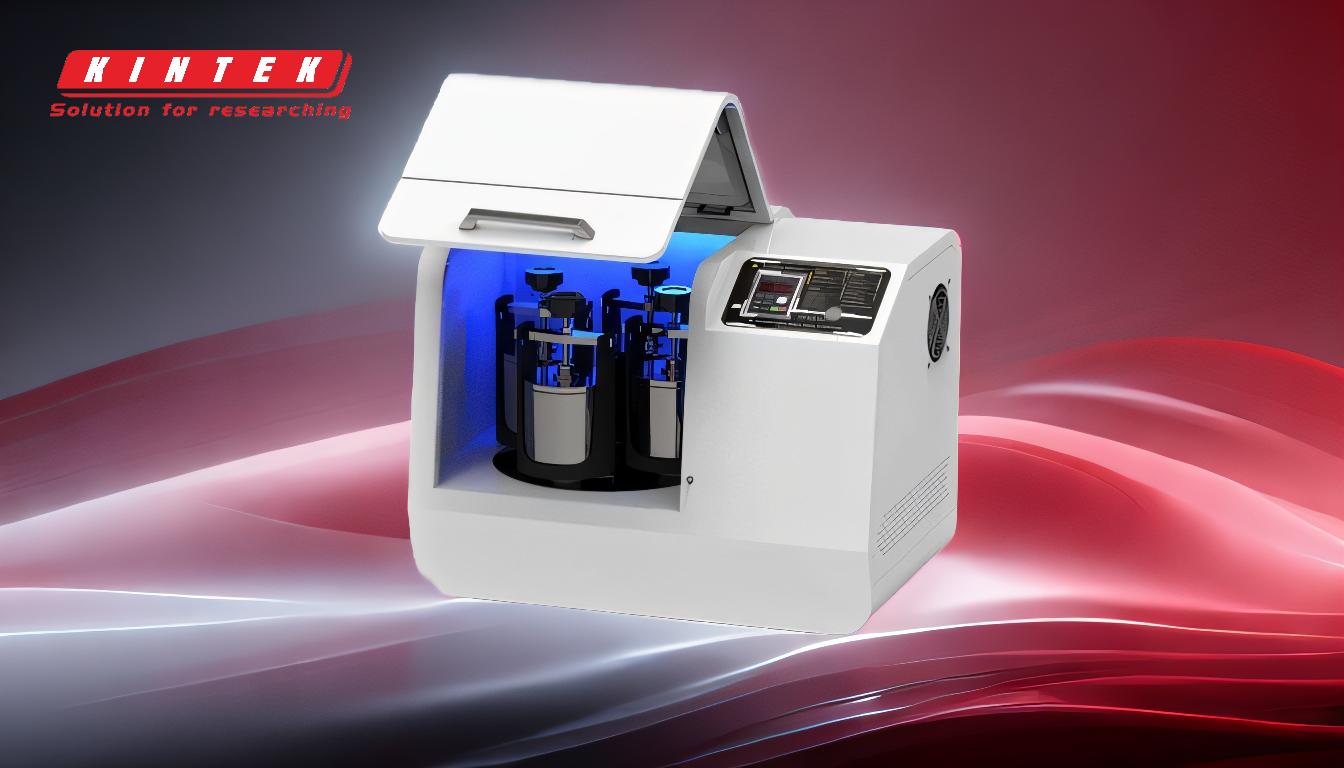
-
High Energy Consumption:
- Ball mills consume a significant amount of energy, primarily due to the friction between the grinding media (balls) and the material being processed. This friction, along with the wear of the balls and the mill's internal armor, contributes to high specific energy consumption.
- The energy efficiency of ball mills is often lower compared to other grinding technologies, making them less suitable for applications where energy conservation is a priority.
-
Wear and Tear:
- The grinding process in ball mills involves continuous contact between the grinding media and the mill's internal surfaces, leading to significant wear over time. This wear necessitates regular maintenance and the replacement of worn parts, such as balls and liners, which can increase operational costs.
- The wear also poses a risk of contamination, as particles from the grinding media or the mill's internal surfaces can mix with the material being processed, potentially affecting the quality of the final product.
-
Noise Pollution:
- Ball mills are known for producing loud noise during operation, primarily due to the high-speed rotation of the mill and the impact of the grinding media. This noise can be a significant issue in environments where noise control is important, such as in urban areas or facilities with strict workplace safety regulations.
- While the use of rubber balls can reduce noise levels to some extent, it does not eliminate the problem entirely.
-
Thermal Damage to Materials:
- The friction and impact forces generated during the grinding process can lead to the generation of heat, which may cause thermal damage to heat-sensitive materials. This can alter the properties of the material being processed, affecting the quality and consistency of the final product.
- Managing the temperature within the mill is crucial to prevent such damage, but it can be challenging, especially in continuous operation scenarios.
-
Handling Limitations:
- Ball mills are not well-suited for processing soft, tacky, or fibrous materials, as these can adhere to the grinding media or the mill's internal surfaces, reducing efficiency and potentially causing blockages.
- The capacity of ball mills is also limited, making them less suitable for applications requiring the processing of large quantities of material in a single batch.
-
Unhandiness and Large Weight:
- Ball mills are often bulky and heavy, making them difficult to transport and install. This can be a significant drawback in facilities where space is limited or where frequent relocation of equipment is required.
- The large size and weight also contribute to higher installation and maintenance costs, as specialized equipment and personnel may be needed for handling and servicing the mill.
-
Vibrations:
- The operation of ball mills can produce strong vibrations, which can affect the stability of the equipment and the quality of the grinding process. These vibrations can also lead to increased wear and tear on the mill's components, further exacerbating maintenance issues.
- In some cases, the vibrations can be transmitted to the surrounding environment, potentially causing disturbances in nearby equipment or structures.
In summary, while ball mills offer several advantages, such as the ability to produce fine powders and handle a wide range of materials, their drawbacks—including high energy consumption, wear and tear, noise pollution, and handling limitations—must be carefully considered. Equipment and consumable purchasers should weigh these factors against their specific operational needs and constraints to determine whether a ball mill is the most suitable choice for their application.
Summary Table:
Drawback | Key Impact |
---|---|
High Energy Consumption | Lower energy efficiency; high operational costs |
Wear and Tear | Increased maintenance costs; risk of contamination |
Noise Pollution | Loud operation; challenges in noise-sensitive environments |
Thermal Damage to Materials | Heat generation may damage heat-sensitive materials |
Handling Limitations | Poor performance with soft, tacky, or fibrous materials; limited capacity |
Unhandiness and Large Weight | Difficult to transport and install; higher installation costs |
Vibrations | Affects equipment stability and grinding quality; may disturb surroundings |
Need help choosing the right grinding equipment for your needs? Contact our experts today for personalized advice!