Ball milling is a mechanical process that involves the grinding, mixing, and homogenization of materials using a rotating cylinder filled with grinding media (balls). It is widely used in materials science, chemistry, and engineering to achieve particle size reduction, mechanical alloying, and structural modifications. The effects of ball milling are multifaceted, including changes in particle size, morphology, crystallinity, and chemical reactivity. These effects are influenced by factors such as milling time, speed, ball-to-powder ratio, and the properties of the materials being milled. Ball milling can lead to enhanced material properties, such as improved mechanical strength, catalytic activity, and electrochemical performance, making it a versatile tool in material synthesis and processing.
Key Points Explained:
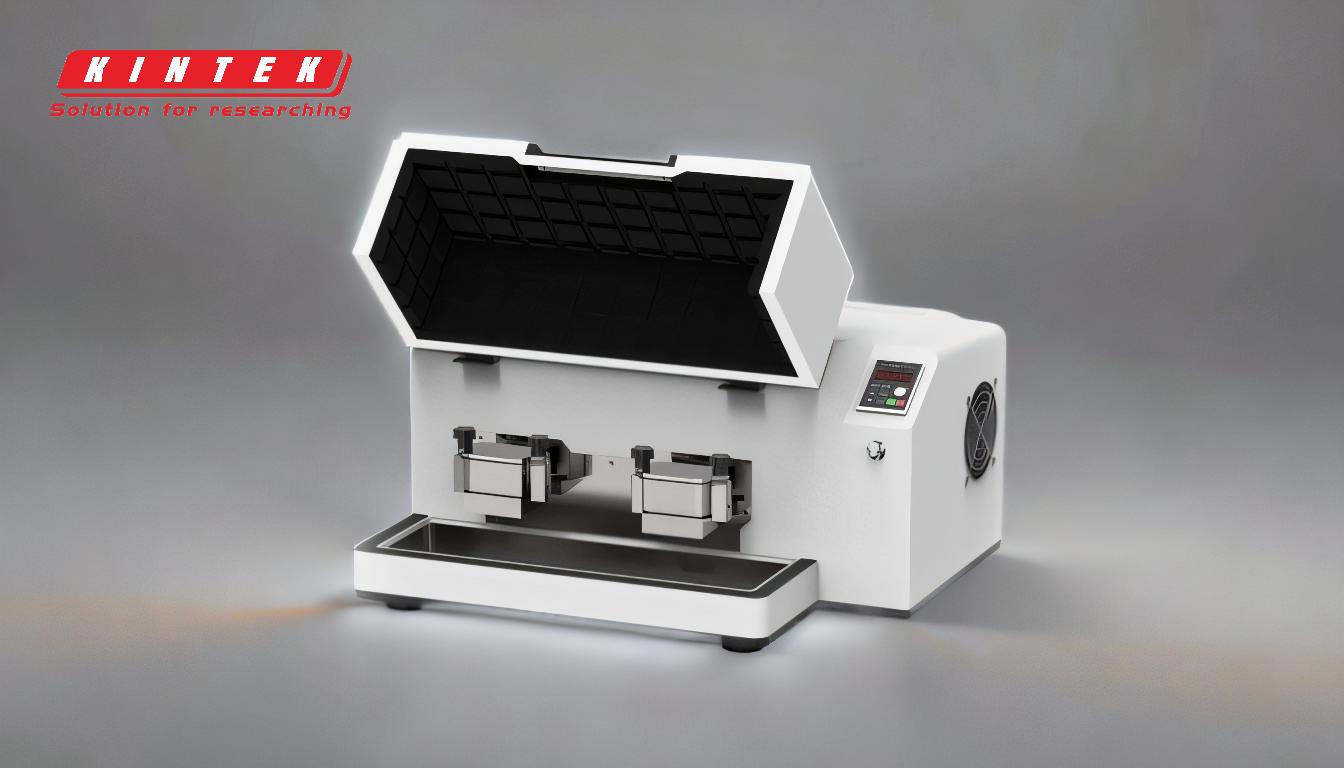
-
Particle Size Reduction:
- Ball milling is primarily used to reduce the particle size of materials. The repeated impact and friction between the grinding balls and the material lead to the breakdown of larger particles into smaller ones.
- The degree of size reduction depends on the milling time, speed, and the hardness of the material. Longer milling times and higher speeds generally result in finer particles.
- Applications: This effect is crucial in industries like pharmaceuticals (for drug formulation), ceramics (for fine powders), and metallurgy (for powder metallurgy).
-
Morphological Changes:
- Ball milling alters the shape and surface characteristics of particles. The process can transform irregularly shaped particles into more spherical or rounded forms due to the mechanical forces involved.
- Surface roughness and porosity may also change, which can affect properties like flowability, packing density, and reactivity.
- Applications: These changes are beneficial in fields like catalysis, where surface area and morphology significantly influence performance.
-
Crystallinity and Phase Transformations:
- Ball milling can induce changes in the crystallinity of materials. Prolonged milling can lead to amorphization (loss of crystalline structure) or the formation of nanocrystalline structures.
- Phase transformations, such as the conversion of one crystalline phase to another, can also occur due to the mechanical energy input.
- Applications: This is particularly useful in synthesizing metastable phases or enhancing the mechanical properties of materials.
-
Mechanical Alloying:
- Ball milling enables the synthesis of alloyed materials by mechanically mixing and bonding different elemental powders. The repeated deformation and cold welding of particles lead to the formation of homogeneous alloys.
- This process is especially valuable for creating alloys that are difficult to produce through conventional melting and casting methods.
- Applications: Used in the production of advanced materials like high-entropy alloys and nanocomposites.
-
Enhanced Chemical Reactivity:
- The mechanical energy from ball milling can increase the chemical reactivity of materials by introducing defects, dislocations, and fresh surfaces. This is known as mechanochemistry.
- Ball milling can facilitate chemical reactions at lower temperatures compared to traditional methods, making it an energy-efficient alternative.
- Applications: Useful in organic synthesis, solid-state reactions, and the production of reactive materials.
-
Nanostructured Materials:
- Ball milling is a common method for producing nanostructured materials, such as nanoparticles, nanocomposites, and nanocrystalline powders.
- The process allows for precise control over the size and distribution of nanostructures, which are critical for applications in electronics, energy storage, and catalysis.
- Applications: Nanostructured materials produced by ball milling are used in batteries, sensors, and coatings.
-
Limitations and Challenges:
- While ball milling offers numerous benefits, it also has limitations. Prolonged milling can lead to contamination from the grinding media or the milling container.
- Over-milling may cause excessive heat generation, leading to unwanted phase transformations or degradation of the material.
- Applications: Proper optimization of milling parameters is essential to avoid these issues.
-
Industrial and Research Applications:
- Ball milling is widely used in both industrial and research settings. It is a cost-effective and scalable method for material processing.
- In research, it is used to explore new materials and phenomena, such as mechanochemical synthesis and nanomaterial fabrication.
- Applications: Industries like mining, pharmaceuticals, and advanced materials rely on ball milling for production and innovation.
By understanding the effects of ball milling, researchers and engineers can optimize the process to achieve desired material properties and performance. The versatility of ball milling makes it a cornerstone technique in modern materials science and engineering.
Summary Table:
Effect | Description | Applications |
---|---|---|
Particle Size Reduction | Reduces particle size through impact and friction. | Pharmaceuticals, ceramics, metallurgy. |
Morphological Changes | Alters particle shape and surface characteristics. | Catalysis, material flowability, and packing density. |
Crystallinity Changes | Induces amorphization or nanocrystalline structures. | Metastable phase synthesis, mechanical property enhancement. |
Mechanical Alloying | Synthesizes alloys through mechanical mixing and bonding. | High-entropy alloys, nanocomposites. |
Enhanced Reactivity | Increases chemical reactivity via mechanochemistry. | Organic synthesis, solid-state reactions, reactive materials. |
Nanostructured Materials | Produces nanoparticles, nanocomposites, and nanocrystalline powders. | Batteries, sensors, coatings. |
Limitations | Contamination, heat generation, and over-milling risks. | Requires parameter optimization. |
Industrial Applications | Cost-effective and scalable material processing. | Mining, pharmaceuticals, advanced materials. |
Optimize your material processing with ball milling—contact our experts today to learn more!