The size of the product in a ball mill is influenced by several factors, including the size and density of the grinding balls, the duration of grinding, the physical and chemical properties of the feed material, the rotation speed of the mill, the feed rate, and the design of the mill itself (such as drum diameter and length ratio). Smaller balls and longer grinding times typically produce finer particles, while the hardness and nature of the material being ground also play a significant role. Additionally, the efficiency of the milling process can be affected by the timely removal of the ground product and the shape of the mill's armor surface.
Key Points Explained:
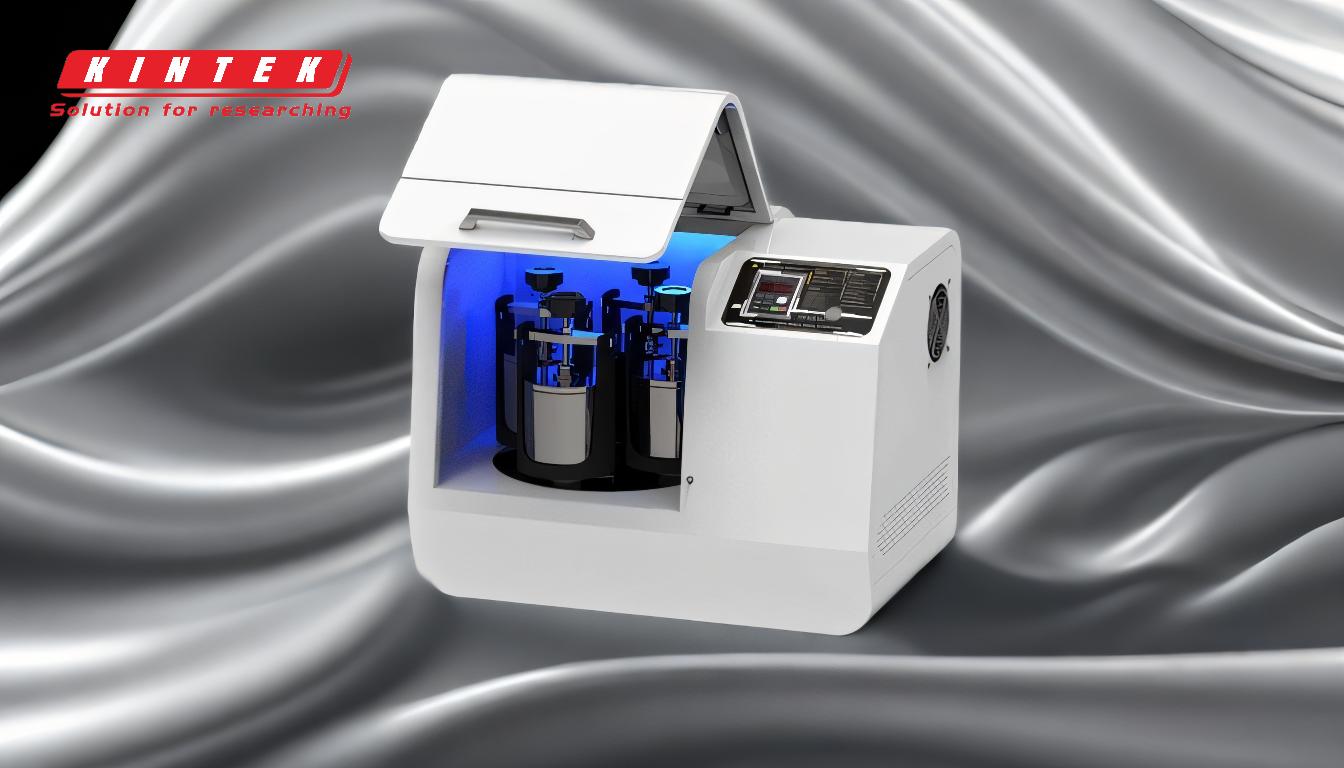
-
Grinding Ball Size and Density:
- Smaller Balls: Smaller grinding balls are more effective at producing finer particles because they have a larger surface area relative to their volume, allowing for more contact points with the material being ground.
- Density: Higher density balls can impart more energy to the material, leading to more effective grinding. However, the optimal size and density depend on the material being processed.
-
Grinding Time:
- Longer Grinding Times: Extending the grinding time allows for more collisions between the balls and the material, which generally results in smaller particle sizes. However, there is a point of diminishing returns where further grinding may not significantly reduce particle size.
-
Physical and Chemical Properties of Feed Material:
- Hardness: Harder materials require more energy to grind and may necessitate different ball sizes or longer grinding times.
- Nature of the Material: The brittleness, moisture content, and other properties of the feed material can affect how easily it is ground down.
-
Rotation Speed of the Mill:
- Optimal Speed: The rotation speed of the mill must be carefully controlled. If the speed is too low, the balls may not cascade effectively, reducing grinding efficiency. If the speed is too high, the balls may centrifuge, also reducing efficiency.
-
Feed Rate and Level in the Vessel:
- Feed Rate: A consistent and appropriate feed rate ensures that the mill is not overloaded, which can reduce grinding efficiency.
- Material Level: The level of material in the mill affects the grinding action. Too much material can cushion the impact of the balls, while too little can lead to inefficient grinding.
-
Mill Design:
- Drum Diameter and Length Ratio: The optimal ratio of drum diameter to length (L:D ratio) is typically between 1.56 and 1.64. This ratio affects the residence time of the material in the mill and the efficiency of the grinding process.
- Armor Surface Shape: The shape of the mill's interior surface can influence the movement of the balls and the material, affecting grinding efficiency.
-
Timely Removal of Ground Product:
- Efficiency: Timely removal of the ground product prevents over-grinding and ensures that the mill operates efficiently. Over-grinding can lead to energy waste and may degrade the quality of the final product.
-
Residence Time:
- Material Residence Time: The amount of time the material spends in the mill chamber directly affects the degree of milling. Longer residence times generally lead to finer particles, but must be balanced with other factors to avoid inefficiencies.
By carefully controlling these factors, operators can optimize the ball milling process to achieve the desired particle size distribution for their specific application.
Summary Table:
Factor | Impact on Particle Size |
---|---|
Grinding Ball Size & Density | Smaller balls and higher density produce finer particles. |
Grinding Time | Longer grinding times reduce particle size but may reach diminishing returns. |
Feed Material Properties | Harder or brittle materials require more energy and time to grind. |
Rotation Speed | Optimal speed ensures efficient grinding; too slow or too fast reduces effectiveness. |
Feed Rate & Material Level | Consistent feed rate and proper material level improve grinding efficiency. |
Mill Design | Drum diameter-to-length ratio (1.56–1.64) and armor surface shape affect grinding efficiency. |
Timely Product Removal | Prevents over-grinding and maintains efficiency. |
Residence Time | Longer residence times produce finer particles but must be balanced for efficiency. |
Optimize your ball milling process for superior results—contact our experts today!