Grindability refers to the ease with which a material can be ground into fine particles. It is influenced by a variety of factors, including the material's physical and chemical properties, the grinding equipment used, and the operating conditions. Understanding these factors is crucial for optimizing grinding processes, improving efficiency, and reducing costs. Key factors include the hardness, toughness, and moisture content of the material, as well as the type of grinding equipment, grinding media, and operational parameters like feed rate and grinding time. Each of these elements interacts in complex ways to determine the overall grindability of a material.
Key Points Explained:
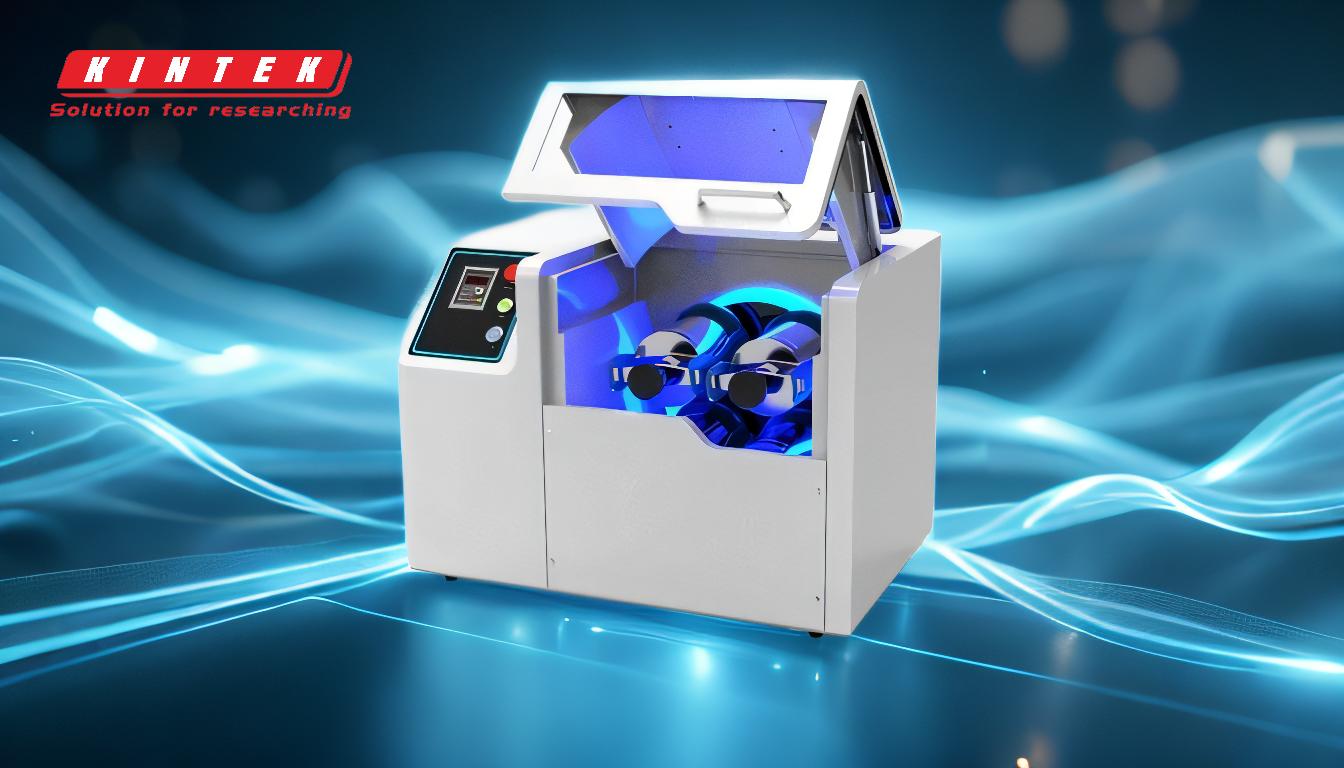
-
Material Properties:
- Hardness: Harder materials are generally more difficult to grind because they resist deformation and fracture. For example, minerals like quartz are harder and thus less grindable compared to softer materials like limestone.
- Toughness: Tough materials absorb more energy before fracturing, making them harder to grind. Materials with high toughness, such as certain metals or polymers, require more energy to break down.
- Moisture Content: The presence of moisture can either aid or hinder grinding. In some cases, moisture can make materials more pliable and easier to grind, but excessive moisture can lead to clogging or reduced efficiency in dry grinding processes.
- Particle Size Distribution: The initial size of the particles can affect grindability. Larger particles may require more energy to break down, while a wide distribution of particle sizes can lead to uneven grinding.
-
Grinding Equipment:
- Type of Mill: Different types of mills (e.g., ball mills, rod mills, hammer mills) are suited to different materials and grinding tasks. The choice of mill can significantly affect grindability. For instance, ball mills are effective for fine grinding, while hammer mills are better for coarse grinding.
- Grinding Media: The size, shape, and material of the grinding media (e.g., balls, rods) can influence the efficiency of the grinding process. Larger media can break down larger particles more effectively, while smaller media are better for fine grinding.
- Mill Speed: The rotational speed of the mill affects the energy imparted to the grinding media and, consequently, the grinding efficiency. Optimal speed varies depending on the material and the desired particle size.
-
Operational Parameters:
- Feed Rate: The rate at which material is fed into the mill can affect grindability. Too high a feed rate can overload the mill, reducing efficiency, while too low a feed rate can lead to underutilization of the mill's capacity.
- Grinding Time: The duration of the grinding process can influence the final particle size distribution. Longer grinding times generally result in finer particles but may also lead to increased energy consumption and wear on the grinding media.
- Temperature: Grinding generates heat, which can affect the material's properties. Excessive heat can cause thermal degradation of the material or lead to changes in its physical properties, such as increased brittleness or reduced plasticity.
-
Environmental Factors:
- Ambient Conditions: Factors such as humidity and temperature in the grinding environment can affect the material's moisture content and, consequently, its grindability. For example, high humidity can increase the moisture content of the material, potentially leading to clogging in dry grinding processes.
- Air Flow: In some grinding processes, such as air-swept mills, the flow of air can help to remove fine particles and prevent clogging. Proper air flow management is essential for maintaining efficient grinding.
-
Material Composition:
- Chemical Composition: The chemical makeup of the material can influence its grindability. For example, materials with a high content of abrasive minerals may wear down grinding media more quickly, reducing the efficiency of the grinding process.
- Presence of Impurities: Impurities or foreign materials in the feed can affect grindability. For instance, the presence of hard impurities can increase wear on the grinding media and reduce the overall efficiency of the grinding process.
-
Energy Input:
- Energy Consumption: The amount of energy required to grind a material is a direct measure of its grindability. Materials that require less energy to achieve the desired particle size are considered more grindable. Energy input is influenced by all the factors mentioned above, including material properties, equipment type, and operational parameters.
In summary, grindability is a complex property influenced by a wide range of factors, including the material's physical and chemical properties, the type of grinding equipment used, and the operational conditions. Understanding these factors allows for the optimization of grinding processes, leading to improved efficiency and reduced costs. Each factor interacts with the others in complex ways, making it essential to consider the entire system when evaluating grindability.
Summary Table:
Factor | Description |
---|---|
Material Properties | Hardness, toughness, moisture content, and particle size distribution affect grindability. |
Grinding Equipment | Type of mill, grinding media, and mill speed impact grinding efficiency. |
Operational Parameters | Feed rate, grinding time, and temperature influence particle size and energy use. |
Environmental Factors | Humidity, temperature, and air flow affect moisture and clogging in grinding. |
Material Composition | Chemical makeup and impurities can alter wear and efficiency. |
Energy Input | Energy consumption directly measures grindability and process efficiency. |
Optimize your grinding process today—contact our experts for tailored solutions!