Filtration is a critical process in various industries, including pharmaceuticals, water treatment, and chemical manufacturing. The efficiency and effectiveness of filtration depend on several factors, which can be broadly categorized into the properties of the solution, the filter medium, and the operational conditions. Understanding these factors is essential for optimizing the filtration process, ensuring desired outcomes, and minimizing costs. Key factors include the nature of the particles in the solution, the characteristics of the filter medium, the pressure or vacuum applied, temperature, and the flow rate. Each of these factors interacts in complex ways, and their optimization requires a thorough understanding of the underlying principles.
Key Points Explained:
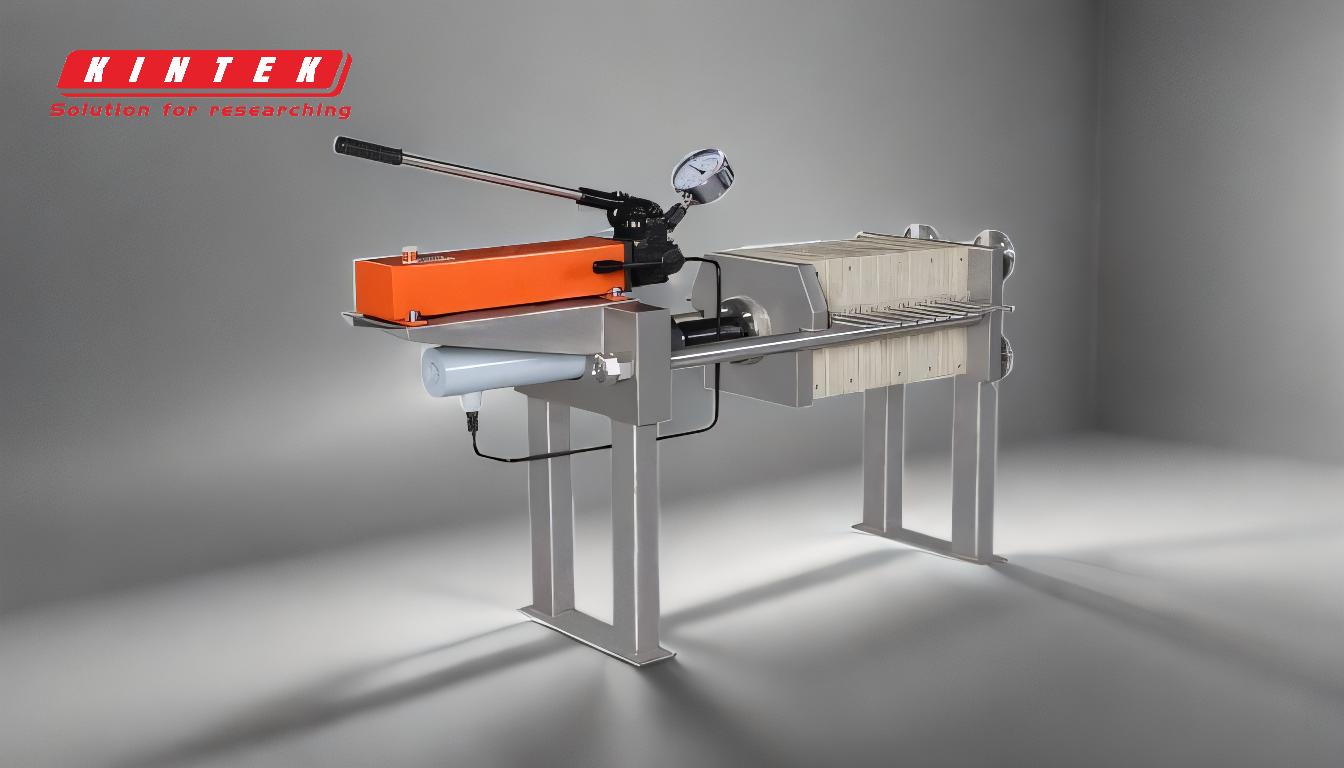
-
Nature of the Particles in the Solution:
- Particle Size: The size of the particles in the solution is one of the most critical factors affecting filtration. Larger particles are easier to filter out, while smaller particles may pass through the filter medium. The particle size distribution also plays a role; a wide distribution can lead to clogging of the filter medium.
- Particle Shape: The shape of the particles can influence how they interact with the filter medium. Irregularly shaped particles may create a more porous filter cake, allowing for better flow, while spherical particles might pack more densely, reducing flow rates.
- Particle Concentration: Higher concentrations of particles can lead to faster clogging of the filter medium, reducing the efficiency of the filtration process. This is particularly important in continuous filtration processes where the filter medium needs to be replaced or cleaned frequently.
-
Characteristics of the Filter Medium:
- Pore Size: The pore size of the filter medium determines which particles can pass through and which are retained. A filter medium with smaller pores will capture smaller particles but may also reduce the flow rate.
- Material Composition: The material of the filter medium affects its chemical compatibility with the solution, its mechanical strength, and its ability to withstand high temperatures or pressures. Common materials include cellulose, glass fibers, and synthetic polymers.
- Surface Area: A larger surface area of the filter medium can increase the filtration capacity, allowing more solution to be processed before the filter becomes clogged. This is particularly important in large-scale industrial applications.
-
Operational Conditions:
- Pressure or Vacuum: The pressure or vacuum applied during filtration can significantly affect the flow rate and the efficiency of the process. Higher pressure can force more solution through the filter medium, but it can also compress the filter cake, reducing permeability.
- Temperature: Temperature can affect the viscosity of the solution and the solubility of the particles. Higher temperatures generally reduce viscosity, making the solution easier to filter, but they can also increase the solubility of certain particles, making them harder to capture.
- Flow Rate: The flow rate of the solution through the filter medium is a critical factor. Too high a flow rate can lead to incomplete filtration, while too low a flow rate can be inefficient. The optimal flow rate depends on the specific application and the characteristics of the solution and filter medium.
-
Chemical Properties of the Solution:
- pH Level: The pH level of the solution can affect the stability of the particles and the filter medium. Extreme pH levels can cause particles to dissolve or aggregate, affecting the filtration process.
- Ionic Strength: The ionic strength of the solution can influence the behavior of charged particles. High ionic strength can lead to particle aggregation, making them easier to filter, but it can also affect the stability of the filter medium.
-
Filter Cake Formation:
- Cake Thickness: The thickness of the filter cake that forms on the filter medium can affect the flow rate and the efficiency of the filtration process. A thicker cake can reduce flow rates but may also provide better filtration.
- Cake Compressibility: Some filter cakes are compressible, meaning they can be compacted under pressure, reducing permeability. This is particularly important in pressure filtration processes.
-
Pre-treatment of the Solution:
- Coagulation and Flocculation: Pre-treating the solution with coagulants or flocculants can aggregate small particles into larger ones, making them easier to filter. This is commonly used in water treatment processes.
- Sedimentation: Allowing the solution to settle before filtration can remove larger particles, reducing the load on the filter medium.
-
Maintenance and Cleaning of the Filter Medium:
- Backwashing: In some filtration systems, backwashing is used to clean the filter medium by reversing the flow of the solution. This can help to remove trapped particles and extend the life of the filter medium.
- Chemical Cleaning: Chemical cleaning agents can be used to dissolve or dislodge particles that are difficult to remove by physical means. This is particularly important in applications where the filter medium is reused.
By considering these factors, it is possible to optimize the filtration process for specific applications, ensuring efficient and effective separation of particles from the solution. Each factor interacts with the others in complex ways, and their optimization requires a thorough understanding of the underlying principles and the specific requirements of the application.
Summary Table:
Category | Key Factors |
---|---|
Particle Properties | Size, shape, concentration |
Filter Medium | Pore size, material composition, surface area |
Operational Conditions | Pressure/vacuum, temperature, flow rate |
Chemical Properties | pH level, ionic strength |
Filter Cake Formation | Thickness, compressibility |
Pre-treatment | Coagulation, flocculation, sedimentation |
Maintenance | Backwashing, chemical cleaning |
Need help optimizing your filtration process? Contact our experts today for tailored solutions!